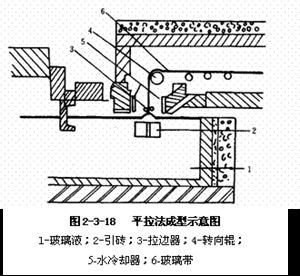
引自lib_ra的博客 第一节 概 述 玻璃是一种具有各种优良性能和易加工的材料,它广泛用于各个领域,如建筑玻璃、日用玻璃、光学玻璃、电真空玻璃、药用玻璃、仪器玻璃、激光玻璃等。它们的品种与用途虽各不相同,但它们的生产工艺却有如下相近的生产流程:成分设计 — 原料加工— 配合料制备 — 坩埚窑熔化或池窑熔化 — 成型 — 一次制品 — 退火窑退火 — 缺陷检验 —一次制品—深加工 —检验 — 二次制品; 在上述流程中,不同制品的差异处在于:有各自的成分设计和各自的成型方法;一次制品经深加工可得二次制品。例如,窗用玻璃在成分设计上采用钠钙硅玻璃系统,由浮法成型制得一次制品窗用玻璃;光学玻璃在成分设计上采用磷酸盐玻璃系统,由压制法成型,经研磨、抛光而制得一次制品光学透镜,等等。 把一次制品经深加工后,增添了新的性质与新的用途,这种玻璃称二次制品,常称深加工玻璃。例如,把一次制品的窗用玻璃,经磁控离子溅射法制成二次制品镀膜玻璃,使玻璃增加了彩色和反射光的性质,等等。以下按上述生产流程叙述玻璃生产工艺。第二节 原料与配合料的制备 一 ?原料的选择 原料的选择与配合料的制备是玻璃生产工艺的重要组成部分,它直接影响制品的产量、质量与成本。因此,能否获得优质高产的配合料对后续的熔制工艺和成型工艺的关系极大。在新品种玻璃投产前必须选用原料,有时为配合工艺要求,需要在日常生产中改变原料品种,因此选择原料是一项重要工作。不同的玻璃品种对原料的要求不尽相同,但也有一些选择原料的共同准则,这些准则是:(1)原料的质量应符合玻璃制品的技术要求,其中包括化学成分稳定、含水量稳定、颗粒组成稳定、有害杂质少 ( 主要指 Fe 2 O 3 )等。(2) 便于在日常生产中调整成分;(3) 适于熔化与澄清,挥发与分解的气体无毒性;(4) 对耐火材料的侵蚀要小;(5)原料应易加工、矿藏量大、分布广、运输方便、价格低等。 对所选原料在使用前应进行破粉碎试验、熔制试验和制品的物性检验。 第三节 原料 玻璃原料通常分为主要原料及辅助原料。 主要原料:在一般玻璃中,它的主要成分有 SiO 2 、 Na 2 O 、 CaO 、Al 2 0 3 、 MgO等五种成分,为引入上述成分而使用的原料称主要原料。辅助原料:为使玻璃获得某种必要的性质,或为加速玻璃熔制过程而引入的原料通称为辅助原料。以下分别叙述上述两类原料。一?引人 SiO 2 的原料SiO 2是玻璃中最主要的成分,它使玻璃具有高的化学稳定性、力学性能、电学性能、热学性能,但含量过多时使熔制的玻璃液粘度过大,为此需相应提高熔化温度。引入2 的原料主要有硅砂和砂岩。1.硅砂也称石英砂,它主要由石英颗粒所组成。质地纯净的硅砂为白色,一般硅砂因含有铁的氧化物和有机质而呈淡黄色、红褐色。评价硅砂的质量主要有以下三个指标:(1) 硅砂的化学组成。它的主要成分是 SiO 2 ,另含有少量的 Al 2 O 3 、 Na 2O 、 K 2 O 、 CaO 等无害杂质。主要的有害杂质为氧化铁,它能使玻璃着成蓝绿色而影响玻璃透明度。有些硅砂中尚含有 Cr 20 3 ,它的着色能力比 Fe 2 O= 大 30-50 倍,使玻璃着成绿色; TiO 2使玻璃着成黄色,若与氧化铁同时存在可使玻璃着成黄褐色。(2)硅砂的颗粒组成。它是评价硅砂质量的重要指标。它的颗粒大小与颗粒组成对原料制备、玻璃熔制、蓄热室堵塞均有直接影响。通常颗粒度越细,其铝铁含量也越大。硅砂的粒径应在0.15 ~ O .8mm 之间。(3)硅砂的矿物组成。与其伴生的无害矿物有长石、高岭石、白云石、方解石等;与其伴生的有害矿物主要有赤铁矿、磁铁矿、钛铁矿等。2.砂岩 是由石英颗粒和粘性物质在地质高压下胶结而成的坚实致密的岩石。根据粘性物质的性质可分为粘土质砂岩、长石质砂岩和钙质砂岩。所以砂岩成分不仅取决于石英颗粒,而且与粘性物质的种类和含量有关。砂岩中的有害杂质是氧化铁。表2 — 3 — 1 为硅质原料的成分范围。表 2 — 3 — 1 硅质原料的成分范围 ( % ) Si0 2 Al 2 0 3 Fe2 0 3 CaO MgO R 2 O 硅砂 90-98 1-5 0.1-0.2 0.1-1 0-0.2 1-3 砂岩 95-980.3-0.5 0.1-0.3 0.05-0.15 0.1-0.15 0.2-0.15 二、引人 Al 2 0 3 的原料引入 A12 0 3 的原料主要有长石和高岭土。1 .长石 在自然界中的长石有:呈淡红色的钾长石 (K 2 O · A1 2 0 3 ·6SiO 2 ) 、呈白色的钠长石 (Na 2 O · Al 2 O 3 · 6SiO 2 ) 和钙长石 (CaO · Al 2 O3 · 6SiO 2 ) 。在矿物中它们常以不同的比例存在,所以长石的化学组成波动较大。对长石的质量要求是: A1 2 O 3 >16 %; Fe 2 0 3 < 0.3 %; R 2 0 > 12 %。2 .高岭土 又称粘土 (Al 2 O 3 · 2SiO2 · 2H 2 0) ,由于所含 SiO 2 及 A1 2 0 3 均为难熔氧化物,所以在使用前应进行细磨。对高岭土的质量要求是:A1 2 0 3 > 25 %; Fe 2 O 3 < O.4 %。表 2 — 3 — 2 为长石和高岭土的成分范围。表 2 — 3— 2 长石和高岭土的成分范围 ( % ) Si0 2 Al 2 0 3 Fe 2 0 3 CaO MgO R 2 O 长石 55 ~65 18 ~ 21 O . 15 ~ 0 . 4 0 . 15 ~ O . 8 - 13 ~ 16 高岭土 40 ~ 60 30 ~40 0.1 ~ O.45 O . 15 ~ O . 8 0 . 05 ~ 0.5 0.1 — 1.35 三、引人 Na 2 0的原料主要有纯碱和芒硝。1 .纯碱 (Na 2 C 0 3 ) 纯碱是微细白色粉末,易溶于水,它是一种含杂质少的工业产品,主要杂质有NaCl( 不大于 1 % ) 。纯碱易潮解、结块,它的水含量通常波动在 9 %~ 10%之间,应储存在通风干燥的库房内。对纯碱的质量要求是: Na 2 C 0 3 > 98 %; NaCl < 1 %; Na 2 SO4 < 0.1 %; Fe 2 0 3 < O.1 %。2 .芒硝 (Na 2 SO 4 ) 有无水芒硝和含水芒硝 (Na 2SO 4 · 10H 2 0) 两类。使用芒硝不仅可以代碱,而且又是常用的澄清剂,为降低芒硝的分解温度常加入还原剂 (主要为碳粉、煤粉等 ) 。使用芒硝也有如下缺点:热耗大、对耐火材料的侵蚀大、易产生芒硝泡,当还原剂使用过多时, Fe 2 O 3还原成 FeS 而使玻璃着成棕色。对芒硝的质量要求是: Na 2 SO 4 > 85 %; NaCl < 2 %; CaSO 4 <4 %; Fe 2 0 3 < O . 3 %; H 2 0 < 5 %。四、引人 CaO 的原料 主要有石灰石、方解石。上述原料均为CaCO 3 ,后者的纯度比前者高。对含钙原料的质量要求是: CaO ≥ 50 %; Fe 2 0 3 < 0.15 %。五、引人MgO 的原料 主要为白云石 (MgCO 3 · CaCO 3 ) ,呈蓝白色、浅灰色、黑灰色。对白云石的质量要求是: MgO ≥20 %; CaO ≤ 32 %; Fe 2 0 3 < 0.15 %。六、澄清剂凡在玻璃熔制过程中能分解产生气体,或能降低玻璃粘度促使玻璃液中气泡排除的原料称澄清剂。常用的澄清剂可分为以下三类:1.氧化砷和氧化锑 均为白色粉末。它们在单独使用时将升华挥发,仅起鼓泡作用。与硝酸盐组合作用时,它低温吸收氧气,在高温放出氧气而起澄清作用。由于As 2 0 3 的粉状和蒸气都是极毒物质,目前已很少使用,大都改用 Sb 2 O 3 。2.硫酸盐原料 主要有硫酸钠,它在高温时分解逸出气体而起澄清作用,玻璃厂大都采用此类澄清剂。3 .氟化物类原料 主要有萤石 (CaF2 ) 及氟硅酸钠 (Na 2 SiF 6 )。萤石是天然矿物,是由白、绿、蓝、紫色组成的微透明的岩石。氟硅酸钠是工业副产品。在熔制过程中,此类原料是以降低玻璃液粘度而起澄清作用。对耐火材料侵蚀大,产生的气体(HF 、 SiF 4 ) 污染环境,目前已限制使用。七、着色剂根据着色机理,着色剂可分为以下三类:1.离子着色剂 锰化合物的原料有:软锰矿 (MnO 2 ) 、氧化锰 (Mn 2 0 3 ) 、高锰酸钾 (KMnO 4 ) 。 Mn2 O 3 使玻璃着成紫色,若还原成 MnO 则为无色。钴化合物的原料有:绿色粉末的氧化亚钴 (C 0 O) 、深紫色的 Co 2 O3 和灰色的 C0 3 0 4 。热分解后的 CoO 使玻璃着成天蓝色。 铬化合物的原料有:重铬酸钾 (K 2 Cr 2 O 7 )、铬酸钾 (K 2 CrO 4 ) 。热分解后的 Cr 2 0 3 使玻璃着成绿色。 铜化合物的原料有:蓝绿色晶体的硫酸铜(CuSO 4 ) 、黑色粉末的氧化铜 (CuO) 、红色结晶粉末的氧化亚铜 (Cu 2 O) 。热分解后的 CuO使玻璃着成湖蓝色。2 .胶体着色剂金化合物的原料有:三氯化金 (AuCl 3 ) 的溶液,为得到稳定的红色玻璃,应在配合料中加入Sn0 2 。银化合物的原料有:硝酸银 (AgNO 3 ) 、氧化银 (Ag 2 0) 、碳酸银 (Ag 2 CO 3 ) 。其中以AgN0 3 所得的颜色最为均匀,添加 Sn0 2 能改善玻璃的银黄着色。铜化合物的原料有: Cu 2 O 及 CuSO 4 ,添加SnO 2 能改善铜红着色。3 .化合物着色剂硒与硫化镉:常用原料有金属硒粉、硫化镉、硒化镉。单体硒使玻璃着成肉红色; CdSe着成红色; CdS 使玻璃着成黄色; Se 与 CdS的不同比例可使玻璃着成由黄到红的系列颜色。八、脱色剂主要指减弱铁氧化物对玻璃着色的影响。根据脱色机理可分为化学脱色剂和物理脱色剂两类。常用的物理脱色剂有Se 、 MnO 2 、 NiO 、 C0 2 0 3 等;常用的化学脱色剂有 As 2 0 3 、 Sb 2 0 3 、 Na 2S 、硝酸盐等。九、氧化剂和还原剂 在熔制玻璃时能释出氧的原料称氧化剂,能吸收氧的原料称还原剂。属氧化剂的原料主要有硝酸盐 (硝酸钠、硝酸钾、硝酸钡 ) 、氧化铈、 As 2 0 5 、 Sb 2 0 5 等。属还原剂的原料主要有碳 ( 煤粉、焦炭、木屑 )、酒石酸钾、氧化锡等。十、乳浊剂 使玻璃产生乳白不透明的原料称乳浊剂。最常用的原料有氟化物 ( 萤石、氟硅酸钠 ) 、磷酸盐 (磷酸钙、骨灰、磷灰石 ) 等。十一、其他玻璃工业所采用的原料主要是矿物原料与工业原料两类。随着工业发展,新的矿物原料不断发现,工业废渣、尾矿的不断增加,影响了环境,为此,应根据玻璃制品的要求而选用新矿与废渣来改变现有的原料结构。国内目前采用的有含碱矿物、矿渣、尾矿,用它们来引入部分氧化钠。这些原料主要有以下品种:1.天然碱 其中含较多的 Na 2 CO 3 和 Na 2 SO 4 ,是一种较好的天然矿物原料,它的成分为: SiO 2 5% ~6 %; Na 2 C 0 3 67 %; Na 2 S0 4 17 %; Fe 2 0 3 0.3 %。2.珍珠岩 它是火山喷出岩浆中的一种酸性玻璃熔岩,其成分随各地而异,一般为灰绿、绿黑,并有珍珠状光泽。其成分主要为: Si0 2 73%; Al 2 O 3 13 %; R 2 0 9 %; Fe 2 O 3 0.9 %~ 4 %。3. 钽铌尾矿 其主要成分为:Si0 2 70 %; Al 2 O 3 17 %; R 2 O8 %; Fe 2 0 3 0.1%。它是目前应用较多的一种代碱尾矿。4.碎玻璃 它是生产玻璃时的废品,常用作回炉料。对制品质量要求不高的小型企业也可全部采用碎玻璃来生产玻璃制品。 第四节 原料的加工一? 工艺流程 若采用块状原料进厂都必须经过破碎、粉碎、筛分而后经称量、混合制成配合料,其一般工艺流程如下: 0 &&image.height>0){if(image.width>=700){this.width=700;this.height=image.height*700/image.width;}}">各厂的工艺流程并不相同,这主要表现在以下几个方面:1.破粉碎系统的选择 一般日用玻璃厂由于熔化量不大,常以粉料进厂,直接拆包把粉料送入粉料仓,因此原料车间不设原料的破粉碎。日熔化量大的平板玻璃厂,一般以块料进厂,则须设原料的破粉碎设备。原料的破粉碎系统可分为单系统、多系统与混合系统。单系统是指各种原料共用一个破碎、粉碎、筛分系统;多系统是指每一种原料单独使用一套。实际上,大中型厂大都采用混合系统,即把用量较多的原料组成多系统,而把用量较少、性质相近的原料组成单系统。2.设备的选择 不同的工艺流程对设备的选择也不尽相同,例如,采用排库或塔库的工艺流程时,前者的每种原料多使用单独称量,而后者使用集中称量。二、原料的破碎与粉碎日熔化量较大的平板玻璃厂一般都是矿物原料块状进厂。为此,必须进行破碎与粉碎。根据矿物原料的块度、硬度和需要的粒度等来选择加工处理方法和相应的设备。要进行破粉碎的原料有砂岩、长石、石灰石、萤石、白云石等。 砂岩是胶结致密、莫氏硬度为7的坚硬矿物。早先是把砂岩煅烧水淬后再进行破粉碎,由于劳动强度大、能耗高、生产率低而不再使用煅烧的方法,目前一般直接由破碎机破碎。采用的粗碎设备是各种型号的颚式破碎机,常用的有复摆式的颚式破碎机。可供选用的中碎与细碎的设备有反击式破碎机、锤式破碎机及对辊破碎机。 颚式破碎机的构造简单、维修方便、机体坚固,能处理粒度范围大和硬度大的矿物。因此,至今它仍是广泛使用的粗碎设备。其不足之处是破碎比不大,一般为4 ~ 6。它不宜用于片状岩石和湿的塑性物料的破碎。反击式破碎机适宜对硬脆矿物进行中碎,具有破碎比大、效率高、电耗小、生产能力大、产物粒度均匀、构造简单等优点,其不足之处是板锤和反击板磨损大,须经常更换。它主要用来进行砂岩的中碎。 对辊破碎机的优点是过粉碎的物料少,能破碎坚硬的物料,设备的磨损小,常用作中块砂岩的细碎设备。其缺点是入料粒度不能过大、产量偏低、噪声和震动大。锤式破碎机适于中等硬度物料的中、细碎,具有较高的粉碎比(10 ~ 50) ,产品粒度较细、机体紧凑,但锤子的磨损较大。它主要用于白云石、石灰石、长石、萤石、菱镁石等原料的中细碎。图 2 —3 — 1 ~图 2 — 3 — 4 为上述设备的示意图。 0 &&image.height>0){if(image.width>=700){this.width=700;this.height=image.height*700/image.width;}}">图 2 — 3 — 1 颚式破碎机 图 2 — 3 — 2 反击式破碎机 0 &&image.height>0){if(image.width>=700){this.width=700;this.height=image.height*700/image.width;}}">图 2 — 3 — 3 对辊机 三、原料的筛分 原料粉碎后都必须进行筛分。生产中常用的筛分设备主要有六角筛和机械振动筛两种。在小型厂常采用摇筛。六角筛适用于筛分砂岩、白云石、长石、石灰石、纯碱、芒硝等粉料,但不适用于含水量高的物料。其优点是运转平稳、密闭性好、振动小、噪声小,其缺点是筛面利用率仅为整个筛面的1/6,因而产量低。目前大型厂都采用机械振动筛来筛分砂岩粉。 机械振动筛主要用来筛分砂岩。其优点是筛分效率高、构造简单、维修方便、密闭性好,能分出多种粒级的物料,电耗低。其缺点是振动和噪声大。若筛与筛间分隔不当易蹦大颗粒。图2 — 3 — 5 及图 2 — 3 — 6 为六角筛示意图和机械振动筛的示意图。四、配合料的制备1.配合料的称量 根据所设计的玻璃成分及给定的原料成分,进行料方计算,确定配料单,按配料单逐个进行原料的称量。常用的秤有台秤、耐火材料秤、标尺式自动秤、多杆秤、自动电子秤等。当工艺上采用排库,一般就采用单独称量,即一种原料单独使用一个秤,通常采用耐火材料秤;当工艺布置采用塔库,则采用集中称量,即各种原料共用一个秤进行称量,此时往图2 — 3 — 4 锤式破碎机 图 2 — 3 — 5 六角筛结构示意图 0 &&image.height>0){if(image.width>=700){this.width=700;this.height=image.height*700/image.width;}}">0 &&image.height>0){if(image.width>=700){this.width=700;this.height=image.height*700/image.width;}}">往采用多杆秤;小型厂一般采用磅秤;自动化程度高的大厂则采用标尺式自动秤;若配料采用电脑控制,则采用自动电子秤;其优点是可以实行远距离给定、远距离操作及回零指示,这样可达到配料线自动化。对秤的精度要求是根据玻璃成分允许波动范围而定,一般要求成分稳定在 0.05 %~ O.1 %之间,对 SiO 2 要求在 0.2%以内,所以要求秤在使用时的称量精度在 1/500 以上,为保证这一精度,要求秤在出厂时的精度达到 1/1000 。2.配合料的混合 配合料的质量与原料的混合工艺、混合机的结构密切相关。影响原料混合质量的因素包括原料的物理性质 (密度、颗粒组成、表面性质等 )、加料顺序、加水量、加水方式、混合时间、是否加入碎玻璃等。按混合机的结构不同可分为:转动式、盘式、桨叶式三类,相应的混合机有鼓形混合机、强制式混合机、桨叶式混合机。 鼓形混合机在结构上与混凝土搅拌机相近。其优点是容量大、效率高、混合质量好,当加入碎玻璃时能防止产生料蛋及减少疙瘩,但动力消耗大,维修不便。强制式混合机由一个能旋转的底盘和两个带有耙子的轴组成。底盘与耙子的旋转方向相反,从而达到强制混合的目的。这种混合机的混合质量优于其他各种混合机。 桨叶式混合机是一种结构简单的混合机。在横向圆筒内,中间主轴旋转,带动焊在其上的括板回转,使配合料搅拌混合,它的使用和维修均较方便,适合于中小企业。3.配合料制备的质量控制 配合料的质量对玻璃制品的产量和质量有较大的影响。虽然不同的玻璃制品对配合料的质量有不同的要求,但在一些基本要求上是一致的。因此,在生产过程中必须控制各个工艺环节以保证配合料的质量。现分述如下。(1)原料成分的控制,分为厂外、厂内控制两类: 厂外控制:要求矿山的原料成分波动范围小,因此,应使用同一矿山与同一矿点的原料。 厂内控制:对进厂的原料成分要勤加分析,各种原料应分别堆放,不能混放,对不同时间进厂的原料也应分别堆放。(2)原料的水分控制。原料的水分波动将直接影响称量的精度,对易潮解的原料,如纯碱、芒硝等,应在库中存放;对水分波动较大的硅砂应进行自然干燥或强制干燥;对防尘用水应严格控制用量。对各种原料应定期检测水分含量。(3)原料的粒度控制。目前一般均采用筛分法以控制粒度的上限,有时由于混合质量较差而产生料蛋时,往往把配合料进行再筛选,这有利于提高玻璃的熔制质量。(4)称量误差程度的控制。称量误差程度直接影响各原料间的配比。它的误差取决于秤的精度误差、容量误差及操作误差。当所称的原料量越接近秤的全容量时,就越接近秤本身所标定的精度,即容量误差越小。因此,在选用秤时必须遵循大料用大秤、小料用小秤的原则。操作误差主要有工人的读数误差、库闸关闭不严造成的漏料误差以及加料过猛造成的冲击误差。(5)混合均匀度的控制。混合均匀度主要与下列因素有关: 混合机的选型:根据工作原理可分为重力式 ( 如鼓形混合机等 ) 和强制式 (如盘式混合机等 )两类。后者在物料混合过程中与物料的粒度、形状、密度和容积密度无关,因而它的混合质量优于前者。进料顺序的影响:合理的进料顺序能防止原料结块,并使难熔原料表面附有易熔原料。一般的进料顺序是:先加难熔的硅砂和砂岩,并同时加水混合,使硅质原料表面附有一层水膜,然后加入纯碱,使其部分溶解于水膜之中,最后加入白云石、石灰石、萤石及已预混合的芒硝和碳粉。混合时间的影响:混合均匀度与混合时间有关,混合时间过长与过短都不利于配合料的混合均匀。它的最佳值应由实验决定。(6)其他。在配合料的运输过程中往往会产生分料、飞料与沾料等。 第五节 玻璃的熔制 ? 玻璃熔制过程概述合格配合料经高温加热形成均匀的、无缺陷的并符合成型要求的玻璃液的过程称为玻璃的熔制过程。玻璃熔制是玻璃生产最重要的环节,玻璃制品的产量、质量、成品率、成本、燃料耗量、窑炉寿命等都与玻璃熔制过程密切相关。因此,进行合理的玻璃熔制是非常重要的。玻璃熔制过程是一个很复杂的过程,它包括一系列的物理的、化学的和物理化学的现象和反应,其综合结果是使各种原料的混合物形成了透明的玻璃液。配合料在高温加热过程中所发生的变化如表 2-3-3 所示。从加热配合料直到熔成玻璃液,常可根据熔制过程中的不同实质而分为五个阶段:硅酸盐形成阶段;玻璃形成阶段;玻璃液的澄清阶段;均化阶段;玻璃液的冷却阶段。玻璃熔制的五个阶段互不相同各有特点,但又彼此关联,在实际熔制过程中并不严格按上述顺序进行。例如,在硅酸盐形成阶段中有玻璃形成过程,在澄清阶段中又包含有玻璃液的均化。熔制的五个阶段,在池窑中是在不同空间同一时间内进行,在坩埚炉中是在同一空间不同时间内进行。表 2 — 3 — 3 配合料加热时的各种过程 物理过程 化学过程 物理化学过程 1 .配合料加热 1 .固相反应 1 .共熔体的生成2 .配合料脱水 2 .各种盐类分解 2 .固态溶解、液态互溶 3 .各个组分熔化 3 .水化物分解 3.玻璃液、炉气、气泡间的相互作用 4 .晶相转化 4 .结晶水分解 4 .玻璃液与耐火材料间的作用 5 .个别组分的挥发 5.硅酸盐的形成与相互作用 以下分别叙述玻璃熔制的五个阶段。 二、玻璃的熔制 ( 一 ) 硅酸盐的形成硅酸盐生成反应在很大程度上是在固体状态下进行的,配合料各组分在加热过程中经过了一系列的物理的、化学的和物理化学变化,结束了主要反应过程,大部分气态产物逸散,到这一阶段结束时配合料变成了由硅酸盐和剩余SiO 2 组成的烧结物。对普通钠钙硅玻璃而言,这一阶段在 800 ~ 900℃ 终结。 从加热反应看,其变化可归纳为以下几种类型:多晶转化:如 Na 2 SO 4 的多晶转变,斜方晶型 - 单斜晶型; 盐类分解;如 CaCO 3 CaO+CO 2 ;生成低共熔混合物:如 Na 2 SO 4 -Na 2 CO 3 ; 形成复盐:如 MgC0 3 +CaCO 3 - ——MgCa(CO 3 ) 2 ; 生成硅酸盐:如 CaO+SiO 2 —— CaSiO 3 ; 排除结晶水和吸附水:如 Na 2 SO4 · 10H 2 O —一 Na 2 SO 4 +10H 2 O 。 ( 二 ) 玻璃的形成烧结物继续加热时,在硅酸盐形成阶段生成的硅酸钠、硅酸钙、硅酸铝、硅酸镁及反应后剩余的 SiO2开始熔融,它们间相互溶解和扩散,到这一阶段结束时烧结物变成了透明体,再无未起反应的配合料颗粒,在 1200 ~ 1250℃范围内完成玻璃形成过程。但玻璃中还有大量气泡和条纹;因而玻璃液本身在化学组成上是不均匀的,玻璃性质也是不均匀的。由于石英砂粒的溶解和扩散速度比之其他各种硅酸盐的溶扩散速度低得多,所以玻璃形成过程的速度实际上取决于石英砂粒的溶扩散速度。石英砂粒的溶扩散过程分为两步,首先是砂粒表面发生溶解,而后溶解的SiO 2向外扩散。这两者的速度是不同的,其中扩散速度最慢,所以玻璃的形成速度实际上取决于石英砂粒的扩散速度。由此可知,玻璃形成速度与下列因素有关:玻璃成分、石英颗粒直径以及熔化温度。除SiO 2 与各硅酸盐之间的相互扩散外,各硅酸盐之间也相互扩散,后者的扩散有利于 SiO 2 的扩散。硅酸盐形成和玻璃形成的两个阶段没有明显的界限,在硅酸盐形成阶段结束前,玻璃形成阶段就已开始,而且两个阶段所需时间相差很大。例如,以平板玻璃的熔制为例,从硅酸盐形成开始到玻璃形成阶段结束共需32min ,其中硅酸盐形成阶段仅需 3 ~ 4min ,而玻璃形成却需要 28 ~ 29min 。 ( 三 ) 玻璃液的澄清玻璃液的澄清过程是玻璃熔化过程中极其重要的一环,它与制品的产量和质量有着密切的关系。对通常的钠钙硅玻璃而言,此阶段的温度为 1400~ 1500℃ 。在硅酸盐形成与玻璃形成阶段中,由于配合料的分解、部分组分的挥发、氧化物的氧化还原反应、玻璃液与炉气及耐火材料的相互作用等原因析出了大量气体,其中大部分气体将逸散于空间,剩余气体中的大部分将溶解于玻璃液中,少部分以气泡形式存在于玻璃液中,也有部分气体与玻璃液中某种组分形成化合物,因此,存在于玻璃液中的气体主要有三种状态,即可见气泡、物理溶解的气体、化学结合的气体。随玻璃成分、原料种类、炉气性质与压力、熔制温度等不同,在玻璃液中的气体种类和数量也不相同。常见的气体有: CO 2 、 O 2 、 N2 、 H 2 0 、 S0 2 、 CO 等,此外尚有 H 2 、 NO 2 、 NO 及惰性气体。熔体的“无泡”与“去气”是两个不同的概念,“去气”的概念应理解为全部排除前述三类气体,但在一般生产条件下是不可能的,因而澄清过程是指排除可见气泡的过程。从形式上看,此过程是简单的流体力学过程,实际上还包括一个复杂的物理化学过程。以下介绍与玻璃澄清机理有关的几个主要方面。 1 .在澄清过程中气体间的转化与平衡在高温澄清过程中,溶解在玻璃液内的。气体、气泡中的气体及炉气这三者间会相互转移与平衡,它决定于某类气体在上述三相中的分压大小,气体总是由分压高的一相转入分压低的另一相中。依据道尔顿分压定律可知,气体间的转化与平衡除与上述气体的分压有关外,还与气泡中所含气体的种类有密切关系。气体在玻璃液中的溶解度与温度有关。在高温下(1400 ~ 1500℃ ) 气体的溶解度比低温 (1100 ~ 1200℃ ) 时为小。由上可知,气体间的转化与平衡决定于澄清温度、炉气压力与成分、气泡中气体的种类和分压、玻璃成分、气体在玻璃液中的扩散速度。 2.在澄清过程中气体与玻璃液的相互作用在澄清过程中气体与玻璃液的相互作用有两种不同的状态。一类是纯物理溶解,气体与玻璃成分不产生相互的化学作用;另一类是气体与玻璃成分间产生氧化还原反应,其结果是形成化合物,随后在一定条件下又析出气体,这一类在一定程度上还有少量的物理溶解。(1)O 2 与熔融玻璃液的相互作用。氧在玻璃液中的溶解度首先决定于变价离子的含量, O 2 使变价离子由低价转为高价离子,如2FeO + 0 &&image.height>0){if(image.width>=700){this.width=700;this.height=image.height*700/image.width;}}">O2 0 &&image.height>0){if(image.width>=700){this.width=700;this.height=image.height*700/image.width;}}">Fe2 0 3 。氧在玻璃液中的纯物理溶解度是微不足道的。 (2)SO 2与熔融玻璃液的相互作用。无论何种燃料一般都含有硫化物,因而炉气中均含有 SO 2 气体,它能与配合料、玻璃液相互作用形成硫酸盐,如:xNa 2 O · ySi0 2 +S0 2 + 0 &&image.height>0){if(image.width>=700){this.width=700;this.height=image.height*700/image.width;}}">02 0 &&image.height>0){if(image.width>=700){this.width=700;this.height=image.height*700/image.width;}}">Na2 SO 4 · (x-1)Na 2 O · ySiO 2 由上可知, SO 2 在玻璃液中的溶解度与玻璃中的碱含量、气相中 0 2的分压、熔体温度有关。单纯的 SO 2 气体在玻璃液中的溶解度较上述反应式为小。 (3)CO 2与熔融玻璃液的相互作用。它能与玻璃液中某类氧化物生成碳酸盐而溶解于玻璃液中,如: BaSi0 3 +C0 2 0 &&image.height>0){if(image.width>=700){this.width=700;this.height=image.height*700/image.width;}}">BaC03 +Si0 2 (4)H 2 0与熔融玻璃液的相互作用。熔融玻璃液吸收炉气中的水汽的能力特别显著,甚至完全干燥的配合料在熔融后其含水量可达 0.02 %。当在1450℃ 熔体中通 1h 的水蒸气后,其含水量可达 O.075 %。 H 2 O在玻璃熔体中并不是以游离状态存在,而是进入玻璃网络。如 : 三 Si — O — Si 三 + H 2 0 —— 0&&image.height>0){if(image.width>=700){this.width=700;this.height=image.height*700/image.width;}}">2(三 Si — OH) Na + 或 2( 三 Si 一 0 一 Si 三 )+Na 2 0+H 2 0 — 一 0&&image.height>0){if(image.width>=700){this.width=700;this.height=image.height*700/image.width;}}">(三 Si — O--H …… 0- 一 Si 三 ) 其他如 CO 、 H 2 、 N 2、惰性气体与玻璃液的相互作用,或化学结合,或物理溶解。 3 .澄清剂在澄清过程中的作用机理为加速玻璃液的澄清过程,常在配合料中添加少量澄清剂。根据澄清剂的作用机理可把澄清剂分为三类。 (1)变价氧化物类澄清剂。这类澄清剂的特点是在低温下吸收氧气,而在高温下放出氧气,它溶解于玻璃液中经扩散进入核泡,使气泡长大而排除。这类澄清剂如As 2 O 3 、 Sb 2 O 3 ,其作用如下: AS 2 0 3 +0 2 0 &&image.height>0){if(image.width>=700){this.width=700;this.height=image.height*700/image.width;}}">As2 0 5 (2) 硫酸盐类澄清剂。它分解后产生 O 2 和 SO 2 ,对气泡的长大与溶解起着重要的作用。属这类澄清剂的主要有硫酸钠Na 2 SO 4 。它的澄清作用与玻璃熔化温度密切相关,在 1400 ~ 1500℃ 就能充分显示其澄清作用。 (3)卤化物类澄清剂。它主要降低玻璃粘度,使气泡易于上升排除。属这类澄清剂的主要有氟化物,如 CaF 2 、 NaF 2。氟化物在熔体中是以形成 [FeF 6 ] 3- 无色基团、生成挥发物 SiF 4 、断裂玻璃网络而起澄清作用。如 : Na 十 三Si — O — Si 三 + NaF —— 0 &&image.height>0){if(image.width>=700){this.width=700;this.height=image.height*700/image.width;}}">三Si — O- F — Si 三 4 .玻璃性质对澄清过程的影响排除玻璃液中的气泡主要有两种方式同时进行,大于临界泡径的气泡上升到液面后排除,小于临界泡径的气泡,在玻璃液的表面张力作用下气泡中的气体溶解于玻璃液而消失。如前所述,在上述过程中伴随有各种气体的交换。因此,玻璃液的粘度和表面张力与澄清密切相关,实际上前者的作用大大高于后者。玻璃液的粘度 η 与气泡上升速度 V 有如下关系 0 &&image.height>0){if(image.width>=700){this.width=700;this.height=image.height*700/image.width;}}">(2-3-1 ) 式中: g ——重力加速度, r ——气泡半径; d 、 d '——玻璃液的密度和气泡中气体的密度。 (四 )玻璃液的均化 玻璃液的均化包括对其化学均匀和热均匀两方面的要求,本节主要叙述玻璃液的化学均匀性。在玻璃形成阶段结束后,在玻璃液中仍带有与主体玻璃化学成分不同的不均体,消除这种不均体的过程称玻璃液的均化。对普通钠钙硅玻璃而言,此阶段温度可低于澄清温度下完成,不同玻璃制品对化学均匀度的要求也不相同。当玻璃液存在化学不均体时,主体玻璃与不均体的性质也将不同,这对玻璃制品产生不利的影响。例如,两者热膨胀系数不同,则在两者界面上将产生结构应力,这往往就是玻璃制品产生炸裂的重要原因;两者光学常数不同,则使光学玻璃产生光畸变;两者粘度不同,是窗用玻璃产生波筋、条纹的原因之一,等等。由此可见,不均匀的玻璃液对制品的产量与质量有直接影响。玻璃液的均化过程通常按下述三种方式进行。 1 .不均体的溶解与扩散的均化过程玻璃液的均化过程是不均体的溶解与随之而来的扩散。由于玻璃是高粘度液体,其扩散速度远低于溶解速度。扩散速度取决于物质的扩散系数、两相的接触面积、两相的浓度差,所以要提高扩散系数最有效的方法是提高熔体温度以降低熔体的粘度,但它受制于耐火材料的质量。显然,不均体在高粘滞性、静止的玻璃液中仅依靠自身的扩散是极其缓慢的,例如,为消除 1mm 宽的线道,在上述条件下所需时间为 277h。 2 .玻璃液的对流均化过程熔窑和坩埚内的各处温度并不相同,这导致玻璃液产生对流,在液流断面上存在着速度梯度,这使玻璃液中的线道被拉长,其结果不仅增加了扩散面积,而且会增加浓度梯度,这都加强了分子扩散,所以热对流起着使玻璃液均化的作用。热对流对玻璃液的均化过程也有其不利的一面,加强热对流往往同时加剧了对耐火材料的侵蚀,这会带来新的不均体。在生产上常采用机械搅拌,强制玻璃液产生流动,这是行之有效的均化方法。 3 .因气泡上升而引起的搅拌均化作用当气泡由玻璃液深处向上浮升时,会带动气泡附近的玻璃液流动,形成某种程度的翻滚,在液流断面上产生速度梯度,导致不均体的拉长。在玻璃液的均化过程中,除粘度对均化有重要影响外,玻璃液与不均体的表面张力对均化也有一定的影响。当不均体的表面张力大时,则其面积趋向于减少,这不利于均化。反之,将有利于均化过程。在生产上对池窑底部的玻璃液进行鼓泡,也可强化玻璃液的均化,这是行之有效的方法。对坩埚炉常采用往埚底压入有机物或无机气化物的方法,可产生大量气体达到强制搅拌的目的。( 五 ) 玻璃液的冷却 为了达到成型所需粘度就必须降温,这就是熔制玻璃过程冷却阶段的目的。对一般的钠钙硅玻璃通常要降到 1000 ℃左右,再进行成型。在降温冷却阶段有两个因素会影响玻璃的产量和质量,即玻璃的热均匀度和是否产生二次气泡。在玻璃液的冷却过程中,不同位置的冷却强度并不相同,因而相应的玻璃液温度也会不同,也就是整个玻璃液间存在着热不均匀性,当这种热不均匀性超过某一范围时会对生产带来不利的影响,例如造成产品厚薄不均、产生波筋、玻璃炸裂等。在玻璃液的冷却阶段,它的温度、炉内气氛的性质和窑压与前阶段相比有了很大的变化,因而可以认为它破坏了原有的气相与液相之间的平衡,要建立新的平衡。由于玻璃液是高粘滞液体,要建立平衡是比较缓慢的,因此,在冷却过程中原平衡条件改变了,虽不一定出现二次气泡,但又有产生二次气泡的内在因素。二次气泡的特点是直径小 ( 一般小于 0 . 1mm ) 、数量多 ( 每 1cm 2 玻璃中可达几千个小气泡 ) 、分布均 (密布于整个玻璃体中 ) 。二次气泡又称再生泡,或称尘泡。 生产实践表明,产生二次气泡的主要情况有: (1)硫酸盐的热分解。在澄清的玻璃液中往往残留有硫酸盐,这种硫酸盐可能来源于配合料中的芒硝以及炉气中的 SO 2 、 O 2 与玻璃中的Na 2 0 的反应结果。当已冷却的玻璃液由于某种原因又被再次加热,或炉气中存在还原气氛,这样就使硫酸盐分解而产生二次气泡。 (2)物理溶解的气体析出。在玻璃液中有纯物理溶解的气体,气体的溶解度随温度升高而降低,因而冷却后的玻璃液若再次升温就放出二次气泡。 (3)玻璃中某些组分易产生二次气泡,例如 BaO 2 随温度的变化: 低温 Ba0 2 0 &&image.height>0){if(image.width>=700){this.width=700;this.height=image.height*700/image.width;}}">BaO+02 高温 三、影响玻璃熔制过程的因素在玻璃生产中往往需要不断地研究燃料耗量、熔窑生产率、窑的侵蚀、产品的产质量、产品成本等,而这些与玻璃熔制过程的状况密切相关。因此,研究影响玻璃熔制过程的因素是必要的。以下叙述一些主要因素。1 .玻璃成分 玻璃成分对玻璃熔制速度有很大的影响,例如玻璃中 SiO 2 、. Al 2 0 3含量提高时,其熔制速度就减慢;当玻璃中 Na 2 O 、 K 2 0 增加时,其熔制速度就加快。 2 .配合料的物理状态对熔制过程影响较大的因素有: (1) 原料的选择。当同一玻璃成分采用不同原料时,它将在不同程度上影响配合料的分层 ( 如重碱与轻碱 )、挥发量 ( 硬硼石与硼酸 ) 、熔化温度 ( 铝氧粉 Al 2 O 3 的熔点为 2050℃ ,钾长石为 1170℃ ) 等。(2) 原料的颗粒组成。其中影响最大的是石英的颗粒度,这是由于它具有较高的熔化温度和小的扩散速度。其次是白云石、石灰石、长石的颗粒度3.熔窑的温度制度熔窑的熔制温度是最重要的因素。温度越高,硅酸盐反应越强烈,石英颗粒的溶解与扩散越快,玻璃液的去泡和均化也越容易。试验表明,在 1450~ 1650℃ 范围内,每升高 10℃ 可使熔化能力增加 5 %~ 10%。因此,提高熔窑温度是强化玻璃熔融,提高熔窑生产率的最有效措施。但必须注意:随着温度的升高,耐火材料的侵蚀将加快,燃料耗量也将大幅度提高。4 .采用加速剂和澄清剂大部分加速剂是化学活性物质。它通常并不改变玻璃成分和性质,其分解产物也可组成玻璃成分,它们往往降低熔体的表面张力、粘度,增加玻璃液的透热性,所以加速剂往往也是澄清剂。澄清剂是用来加速玻璃液的澄清过程。属于此类的物质有:硝酸盐、硫酸盐、氟化物、变价氧化物等。 5 .采用高压与真空熔炼 在石英光学玻璃生直排式筛粉机产工艺中常采用真空和高压熔炼技术来消除玻璃液中的气泡。采用高压使可见气泡溶解于玻璃液中,采用真空法能使可见气泡迅速膨胀而排除。6 .辅助电熔在用燃料加热的熔窑作业中,同时向玻璃液通入电流使之增加一部分热量,从而可以在不增加熔窑容量下增加产量,这种新的熔制方式称为辅助电熔。一般分别设在熔化部、加料口、作业部,可提高料堆下的玻璃液温度40 ~ 70℃ ,这就大大提高了熔窑的熔化率。 7 .机械搅拌与鼓泡在窑池内进行机械搅拌或鼓泡是提高玻璃液澄清速度和均化速度的有效措施。 四、玻璃熔窑玻璃熔窑的作用是把合格的配合料熔制成无气泡、条纹、析晶的透明玻璃液,并使其冷却到所需的成型温度。所以玻璃熔窑是生产玻璃的重要热工设备,它与制品的产质量、成本、能耗等有密切关系。玻璃熔窑可分为池窑与坩埚窑两大类。把配合料直接放在窑池内熔化成玻璃液的窑称池窑;把配合料放入窑内的坩埚中熔制玻璃的窑称坩埚窑。凡玻璃品种单一、产量大的都采用池窑。若产品品种多、产量小的都采用坩埚窑。以下主要介绍池窑。玻璃池窑有各种类型,按其特征可分为以下几类: 1 .按使用的热源分 (1)火焰窑。以燃烧燃料为热能来源。燃料可以有煤气、天然气、重油、煤等。 (2)电热窑。以电能作热能来源。它又可分为电弧炉、电阻炉及感应炉。 (3) 火焰 - 电热窑。以燃料为主要热源,电能为辅助热源。 2.按熔制过程的连续性分 (1)间歇式窑。把配合料投入窑内进行熔化,待玻璃液全部成型后,再重复上述过程。它是属于间歇式生产,所以窑的温度是随时间变化的。 (2)连续式窑。投料、熔化与成型是同时进行的。它是属于连续生产,窑温是稳定的。 3 .按废气余热回收分 (1)蓄热式窑。由废气把热能直接传给格子体以进行蓄热,而后在另一燃烧周期开始后,格子体把热传给助燃空气与煤气,回收废气的余热。 (2)换热式窑。废气通过管壁把热量传导到管外的助燃空气达到废气余热回收。 4 .按窑内火焰流动走向分 (1)横火焰窑。火焰的流向与玻璃液的走向呈垂直向。 (2) 马蹄焰窑。火焰的流向是先沿窑的纵向前进而后折回呈马蹄形。 (3)纵火焰窑。火焰沿玻璃液流方向前进,火焰到达成型部前由吸气口排至烟道。根据我国目前的能源情况,国内所有玻璃厂都采用火焰窑,或用重油,或用煤气为燃料。大中型平板玻璃厂一般均采用横焰蓄热式连续池窑来熔化玻璃,图2 — 3 — 7 为其平面图,图 2 — 3 — 8 为其立面图。 0 &&image.height>0){if(image.width>=700){this.width=700;this.height=image.height*700/image.width;}}">图 2 — 3 — 7 浮法窑平面图 l- 投料口; 2- 熔化部; 3 、 6- 小炉; 4- 冷却部; 5- 流料口 0&&image.height>0){if(image.width>=700){this.width=700;this.height=image.height*700/image.width;}}">图 2 — 3 — 8 浮法窑立面图 1- 小炉口; 2- 蓄热室; 3- 格子体; 4- 底烟道; 5- 联通烟道; 6- 支烟道;7- 燃油喷嘴 从图 2-3-7 可以看出,配合料由投料口 1 进入熔化部 2 ,由窑的一侧的小炉 3喷焰加热,火焰把热量传给配合料,熔化与澄清后的玻璃液进入冷却部 4 ,经流槽口 5 进入锡槽。燃烧后的废气进入另一侧的小炉 6 。从图 2-3-8 可以看出,燃烧后的废气进入小炉口 1 ,在蓄热室 2 中废气把热量传给格子体 3,使格子体的温度上升,废气经蓄热室下部烟道 4 、联通烟道 5 进入支烟道 6 ,汇至总烟道由烟囱把废气排放于大气中。 0&&image.height>0){if(image.width>=700){this.width=700;this.height=image.height*700/image.width;}}">通常每隔20min 火焰就换向一次,即通过换向设备,使气流 ( 废气与助燃空气 ) 的流向相反。其过程为助燃空气经换向设备进入支烟道 6、联通烟道 5 进入蓄热室下部烟道 4 ,助燃空气在蓄热室 2 上升过程中,被已加热的格子体 3 所加热,它经小炉口 1进入熔窑内火焰空间,与此同时,设在小炉口 1 下部的燃油喷嘴 7同时喷射雾化油,与助燃空气形成火焰燃烧,它把燃烧热传给配合料以进行熔化,燃烧后废气进入另一侧的小炉口中。 图 2 — 3 — 9为换向闸板。 上述类型的平板玻璃窑以重油为燃料,熔化温度为 1580 ~ 1600℃ ,熔化率为 2 ~ 2.5t/(m 2 · d),窑的使用周期为 5 ~ 8 年。 五、窑用耐火材料 近 40年来,由于耐火材料的质量有了显著的提高,新型耐火材料又不断涌现,使玻璃工业在高温强化熔融技术上取得了很大的进展。例如,熔化温度由1450℃ 提高到 1580 ~ 1600℃ ,熔化率由 1.2 t/(m 2 · d) 提高到 3 t/(m 2 · d),窑的使用周期由 1.5 年延长到 5 ~ 8 年,由熔制造成的缺陷大幅度降低,等等。熔窑用耐火材料在长期使用中,要经受高温、火焰、碱性飞料、玻璃液等的物理化学侵蚀作用。因而玻璃窑用耐火材料除应具备一般工业炉用耐火材料的基本性质外,还必须满足玻璃熔制工艺上的特殊要求。包括(1) 有足够高的耐火度; (2) 有相当高的高温力学强度; (3) 高温体积稳定性好; (4)抗玻璃液、碱性飞料、火焰的侵蚀能力强。此外,还有对玻璃液不产生污染、热稳定性好以及对尺寸公差、价格等的要求。 耐火材料按其耐火度可分为1580 ~ 1770℃ 的普通耐火制品; 1770 ~ 2000℃ 的高耐火制品;> 2000℃的特高耐火制品。按其化学成分可分为: SiO 2 系、 Al 2 O 3 -SiO 2 、 A1 2 03-SiO 2 -ZrO2系、 MgO 系等。以下介绍玻璃熔窑常用的耐火材料。 1 .硅氧质耐火材料 (SiO 2 系 ) (1) 硅砖。是以 SiO 2为主体的耐火材料。它是由纯度高、结晶细密的石英质岩石与少量石灰乳混合后经煅烧而成。其中熟料是废硅砖粉。其成分范围是: SiO 2 94%~ 98 %; Ca01.5 %; 3.5 %; Al 2 O 3 0.2 %~ 2 %; Fe 2 O 3 0.3 %~ 3.0%; R 2 O0 ~ O.5 %,国家标准规定有三种牌号,如表 2 — 3 — 4 所示。 表 2 — 3 — 4硅砖的理化性能指标 项 目 GB 一 96 GB 一 95 GB 一 94 SiO 2 ( % ) 95.5 95 94 Fe 2 03 ( % ) 1.0 1.2 1.5 耐火度 (℃) 1710 1710 1710 O.2MPa 荷重软化温度 (℃) 不低于1650 1650 1630 单重 <15k 的硅砖的显气孔率 ( % ) 不大于 20 21 22 常温耐压强度 (MPa)不小于 29.4 29.4 24.5 真密度 (g/cm 3 ) 不大于 2.37 2.38 2.38硅砖的主要耐火矿相是鳞石英和方石英、少量未转化的残余石英,此外还有极少量的玻璃相。硅砖中各种不同变体的晶型转化都伴随有体积的变化,如表2 — 3 — 5 所示。最大的热膨胀发生在 300℃ 以下,因此,在烤窑时须特别注意;在 700℃以上一般不会对硅砖砌体造成破坏。硅砖的热稳定性较差, 850℃ 的硅砖在水中急冷而不破坏的次数只有 1 ~ 2次。硅砖是酸性耐火材料,有良好的抗酸性渣性能,但对碱性组分的耐蚀能力差,抗玻璃液的冲刷能力也差。 由于硅砖的荷重软化温度高、抗玻璃液中R 2 O 的能力差,所以它适用于砌筑各种碹体、山墙、冷却部胸墙等。不适宜砌筑与玻璃液相接触的池壁等。 表 2-3-5 硅砖中 SiO2 各种晶型的转化 晶 型 α→β( 升温.℃ ) β→α ( 降温 . ℃ ) 体积变化 ( % ) 鳞石英 117 和 163163 和 117 ±0.2 和 ±O.2 方石英 220 ~ 275 241 ~ 195 ±2.8 石英 575 575 ±O.82(2)白泡石。又称泡沙石或白砂石。是一种天然的耐火材料,它是由高岭石粘结的石英砂岩。外观选择应以青灰色、致密坚硬、不含杂质和条纹者为佳。其主晶相以石英和高岭石为主。有明显的层状构造和各向异性。白泡石的耐火度波动在1650 一 1730℃ 之间。 白泡石的膨胀性与硅砖不同, 700 ~ 800℃时的热膨胀系数最大,此时最易炸裂。煅烧后的白泡石,荷重软化温度与耐压强度都有明显提高,残余膨胀小,体积稳定,抗热冲击性也大为改善,所以一般都采用煅烧后的白泡石作耐火材料。在中小型池窑上已广泛用作池壁砖。2 .硅酸铝质耐火材料 (Al 2 O 3 -Si0 2 系 ) (1) 粘土砖。是由耐火粘土为主要原料制成的耐火砖。 Al 2 O3 的含量在 30 %~ 46 %,主晶相是莫来石与部分 SiO 2 晶体 ( 以方石英为主 ) ,并有相当数量的玻璃相。耐火度可达1580 ~ 1750℃ ,但荷重软化温度只有 1300 ~ 1450℃ 。因此,允许的使用温度也相应降低,一般为 1300℃以下。它主要用于熔窑温度较低的部位,如池底砖、熔化部和冷却部最下层的池壁砖、大梁砖、蓄热室下部的墙、炉条碹、格子砖下部、烟道碹等。(2) 高铝砖。它以高铝矾土为原料,在 1500℃ 下烧制而成。随 Al 2 O 3 的增加,又可分为硅线石制品、莫来石制品、莫来石- 刚玉制品、刚玉 - 莫来石制品以及刚玉制品。随 A1 2 0 3 含量不同,其主晶相也不相同, Al 2 O 3含量低时以莫来石晶相为主,含量高时以刚玉晶相为主,其中均含有少量的玻璃相。 根据国家标准,高铝砖按理化性能分为四种牌号, A1 2 03 含量低的高铝砖与粘土砖的理化性能相近,表 2 — 3 — 6 列出了高铝砖的理化性能。 表 2 — 3 — 6 高铝砖的理化性能性 能 LZ-75 LZ-65 LZ-55 LZ-48 A1 2 0 3 ( % ) 75 65 55 48 耐火度 ( ℃ )1790 1790 1770 1750 O.2MPa 荷重软化温度不低于 ( ℃ ) 1520 1500 1470 1420重烧线变化: ( 1500 ℃ ,2h ,% ) ±O . 1 ~ O . 4 ±O . 1 ~ O . 4 ±O . 1 ~ O .4 ( 1450 ℃ ,2h ,% ) ±O . 1 ~ 10 -4 显气孔率 ( % ) 23 23 22 22 常温耐压强度(MPa) 53.9 49 44.1 39.2高铝砖的耐火度、荷重软化温度、抗玻璃液侵蚀的能力都比粘土砖高。因此,它主要用于温度较高的承重部位,如蓄热室的间隔墙和侧墙、蓄热室的半圆碹等。3 .电熔耐火材料 (A1 2 O 3 -Si0 2 -ZrO 2 系 )把耐火材料的原料放在电弧炉中进行熔化,再浇注成型、缓慢冷却而成。其特点是结构致密、气孔率低、容积密度大、力学强度高、荷重软化温度高、耐蚀性能优良。(1) 电熔锆莫来石砖 ( 又称黑铁砖 ) 它是最早的电熔耐火材料,其成分与理化性能如表 2 — 3 — 7 所示。 表 2-3-7电熔锆莫来石砖的成分与理化性质 Al 2 0 3 ( % ) 不小于 ZrO ( % ) Si0 2 ( % ) 耐火度 ( ℃ )不小于 荷重软化温度 ( ℃ ) 不小于 容积密度 (g/cm 3 ) 显气孔率 ( % ) 不小于 常温耐压强度 (MPa) 不小于最高使用温度 ( ℃ ) 热膨胀率 ( % ) (O ~ 1000℃ ) 70 7-10 19-22 1700 17002.85-3.2 10 294 1700 0.55-0.70 (2) 电熔锆刚玉砖 ( 又称白铁砖 ) 其主要晶相为紧密共存的刚玉(α-Al 2 0 。 ) 和斜锆石 (Zr0 2 ),玻璃相的含量很少。这种砖的最大特点是组织稳定而致密,抗玻璃液侵蚀的性能强,比铝氧系统的电熔耐火材料还好,是目前抗玻璃液侵蚀最佳的材料。电熔锆刚玉砖成分范围为: A1 2 0 3 47 %~ 51 %; ZrO 2 30 %~ 43 %; Si0 2 10 %~ 18%。一般把电熔锆刚玉砖中按 ZrO 2 含量分为 30 # 、 33 # 、 35 # 、 40 # 等若干级,其理化性能如表2-3-8 所示。 电熔锆莫来石砖和电熔锆刚玉砖主要用于熔窑投料池、池壁、流液洞、喷嘴砖、下间歇砖等与玻璃液相接触的部位。 表2-3-8 电熔锆刚玉砖的理化性能 牌号 耐火度 ( ℃ ) 不小于 荷重软化温度 ( ℃ ) 不小于 最高使用温度 ( ℃ )容积密度 (g/cm 3 ) 热膨胀率 ( % ) ( 1000℃ ) 导热系数 [Kj/ ( m.h.℃ ) ] 常温耐压强度(MPa) 600℃ 1000℃ 30 # 1700 1650 1700 3.1-3.4 0.55-0.8 13.4 14.729.4 33 # 1730 1650 1700 3.2-3.6 0.55-0.8 13.4 14.7 29.4 35 # 17501700 1700 3.4-3.8 0.6-0.85 13.3 14.7 29.4 40 # 1780 1700 17003.45-4.1 0.6-0.9 13.3 14.7 29.4 4 .碱性耐火材料 (MgO 系 )目前在玻璃窑上使用的碱性耐火材料有:镁砖、镁硅砖、镁铬砖、铬镁砖等。 镁砖是以方镁石为原料制成, MgO 的含量为 80 %~ 85%。按生产工艺不同,可分为烧结镁砖和不烧结镁砖。前者以烧结镁砂为原料,加入含亚硫酸盐的纸浆废液作结合剂,在 1600 ~ 1700℃下烧成,其主矿相为方镁石,含少量玻璃相。不烧结镁砖是在烧结镁砂中加入矿化剂和低温结合剂,经加压成型、干燥而成制品。其三种牌号的理化性能如表2 — 3 — 9 所示。 镁砖的抗碱性能强,抗酸能力差,它主要用于蓄热室上部的格子体和蓄热室墙的上半部。 表 2 — 3 — 9镁砖的理化性能 项 目 MZ-91 MZ-89 MZ-87 MgO( % ) 不小于 91 89 87 CaO( % ) 不大于 33 3 O.20MPa 荷重软化温度 (℃) 大于 1550 1540 1520 显气孔率 ( % ) 不大于 18 20 20重烧线变化 ( %, 1650℃ 2h) 不大于 0.5 0.6 常温耐压强度 (MPa) 大于 58.8 49 39.2六、熔窑的节能玻璃工业是能耗最多的工业之一。在玻璃生产中常把熔窑的单位热耗作为熔窑热效率的主要技术经济指标。目前平板玻璃熔窑的热效率高的可达 30%~ 40 %,低的一般不超过 25 %,平板玻璃的单位热耗水平较先进的为 4600 ~ 7100Kj/kg 玻璃液,而较差的为10880 ~ 11700kJ/kg 玻璃液。 为降低能耗通常采用以下措施: 1 .高温熔化制度实践证明,高温熔化制度是提高熔窑产量、改善玻璃质量、降低单位热耗的有效途径。表 2 — 3-10 、表 2 — 3 — 11表示了熔化温度与玻璃形成时间与熔化率之间的关系。 表 2-3-10 在不同温度下玻璃形成的时间 玻璃熔化温度 (℃) 14001450 1500 1550 1600 1650 1700 熔化时间 (min) 53.7 36.4 20.9 10.0 4.02.4 1.6 表 2 — 3 — 11 在不同温度下的熔化率 玻璃熔化温度 (℃) 1370 1420 1470 1500 15301600 熔化率 (kg/m 2 .d) 350 700 1050 1500 1800 3000 为提高熔化温度应采取如下措施:(1) 使用高质量的优质耐火材料; (2) 采用高热值燃料; (3) 提高空气预热温度, (4) 富氧燃烧。 2 .熔窑保温加强窑体保温,减少窑体的热散失是降低单位热耗的有效措施,如表 2 — 3 — 12 所示。 表 2 — 3 — 12蓄热式熔窑保温前后的热损失 热耗项目 无保温 ( % ) 有保温 ( % ) 1 .玻璃熔化热 2 .废气热损失 3 .池底热损失 4.窑顶热损失 5 .胸墙热损失 6 .熔化部池壁热损失 7 .通过吊墙的热损失 8 .通过加料口的热损失 9 .冷却流液洞的热损失10 .冷却池壁的热损失 11 .蓄热室、小炉的热损失 12 .其他热损失 19.1 18.30 10.00 9.80 4.706.90 2.80 2.70 2.20 6.20 13.30 4.00 19.10 18.30 5.80 3.40 3.30 3.211.68 1.26 2.20 6.20 6.20 3.08 合 计 100 73.63 由上例可知,采用熔窑保温措施后可降低热耗约26 %。 3 .废气余热利用 由表 2 — 3 — 12 可知,由废气带走的热损失占燃料总热量的 18.30%,若能部分回收可大大降低燃料耗量。一般常采用余热锅炉,所产生的蒸汽供生产及生活使用。 4 .改进玻璃的熔化工艺通过改进玻璃熔化工艺可以提高配合料的熔化速度,降低单位能耗,又提高了玻璃液的质量。常用的措施有配合料的压块、粒化、采用新式投料机、采用碎玻璃垫层加料法等。5 .改进燃烧技术 为使燃料充分燃烧常采用的措旅有火焰增碳技术、油掺水技术以及降低燃烧时的空气过剩系数等。 6.采用鼓泡与机械搅拌技术 可加速玻璃液的热交换,提高熔化能力,强化澄清与均化,特别是提高深层玻璃液的温度。此项技术是节能的有效措施。7 .改进熔窑结构 主要有加宽投料池、改进蓄热室及小炉结构等。 8 .采用辅助电熔及实现生产自动化。 第六节 玻璃的成型 玻璃的成型方法可以分为两类:热塑成型和冷成型,后者包括物理成型 ( 研磨和抛光等 ) 和化学成型 ( 高硅氧质的微孔玻璃 )。通常把冷成型归属到玻璃冷加工中,玻璃成型通常指热塑成型。 玻璃的成型方法有吹制法 ( 空心玻璃等 ) 、压制法 ( 烟缸等 )、压延法 ( 压花玻璃等 ) 、浇铸法 ( 光学玻璃等 ) 、拉制法 ( 窗用玻璃等 ) 、离心法 ( 玻璃棉等 ) 、烧结法 (泡沫玻璃等 ) 、喷吹法 ( 玻璃珠等 ) 、焊接法 ( 仪器玻璃等 ) 、浮法 ( 板玻璃等 ) 以及上述几种方法的组合,如压 -吹法等。 以下就窗用平板玻璃的成型方法作概要的介绍。 ? 浮法成型浮法是指熔窑熔融的玻璃液在流入锡槽后在熔融金属锡液的表面上成型平板玻璃的方法。 熔窑的配合料经熔化、澄清、冷却成为 1150 ~1100 ℃左右的玻璃液,通过熔窑与锡槽相连接的流槽,流入熔融的锡液面上,在自身重力、表面张力以及拉引力的作用下,玻璃液摊开成为玻璃带,在锡槽中完成抛光与拉薄,在锡槽末端的玻璃带已冷却到600 ℃ 左右,把即将硬化的玻璃带引出锡槽,通过过渡辊台进入退火窑。其过程如图 2 — 3 — 10 所示。 0&&image.height>0){if(image.width>=700){this.width=700;this.height=image.height*700/image.width;}}">1 .浮法玻璃的成型机理 浮法玻璃的成型是在锡槽中进行的。玻璃液由熔窑经流槽进入锡槽后,其成型过程包括自由展薄、抛光、拉引等,为此讨论以下四个相应问题: (1)玻璃液在锡液面上的浮起高度。玻璃液与锡液互不浸润、互无化学反应。锡液的密度大于玻璃液,因而玻璃液浮于锡液表面,如图 2 — 3 —1l 所示。其浮起高度和 h h ,和沉入深度 h 2 可用下式表示: 0 &&image.height>0){if(image.width>=700){this.width=700;this.height=image.height*700/image.width;}}">(2-3-2 ) 0 &&image.height>0){if(image.width>=700){this.width=700;this.height=image.height*700/image.width;}}">式中:d g 、 d τ ——玻璃液与锡液的密度; H ——玻璃液在锡液面上的自由厚度。 (2)浮法玻璃的自由厚度。当浮在锡液面上的玻璃液不受到任何外力作用时所显示的厚度称自由厚度。它决定于下列各力之间的平衡:玻璃液的表面张力σg 、锡液的表面张力σ t 、玻璃液与锡液界面上的表面张力σ gt 以及玻璃液与锡液的密度 d g 、 d τ。其间的关系可用下式表示 :0 &&image.height>0){if(image.width>=700){this.width=700;this.height=image.height*700/image.width;}}">(2-3-3 )式中: g ——重力加速度。 应用上述公式可对浮法玻璃的自由厚度 H 作如下估算:当成型温度为 1000 ℃时,σ g =340 × 10 -3 N/m 、σ t =500 × 10 -3 N/m 、σ gt =550 × 10 -3 N/m、 d t = 6.7g /cm 3 、 d g = 2.5g /cm 3 ,把上述各值代入式 (2 — 3 — 2) 得 H=7mm ,它与实测相近。 (3)玻璃在锡液面上的抛光时间。玻璃液由流槽流入锡槽时,由于流槽面与锡液面存在落差以及流入时的速度不均将形成正弦状波纹,在进行横向扩展的同时向前漂移,此时正弦状波形纹将逐渐减弱( 如图 2 — 3 — 12 所示 )。处于高温状态下的玻璃液由于表面张力的作用,使其具有平整的表面,达到玻璃抛光的目的,其过程所需时间即为抛光时间。它对设计锡槽的长度与宽度是一重要的技术参数。0 &&image.height>0){if(image.width>=700){this.width=700;this.height=image.height*700/image.width;}}">可以把玻璃液由高液位( 流槽面 ) 落入低液位 ( 锡槽面 ) 所形成的冲击波的断面曲线近似地假定为正弦函数: 0 &&image.height>0){if(image.width>=700){this.width=700;this.height=image.height*700/image.width;}}">(2-3-4 ) 把 OC 段的玻璃液视为一个玻璃滴,因而其中任一点的 X 处所受到的压强 P是玻璃表面张力所形成的压强和流体的静压强之和,即: 0 &&image.height>0){if(image.width>=700){this.width=700;this.height=image.height*700/image.width;}}">(2-3-5 ) 式中:σ g ——玻璃液在成型温度 ( 1000 ℃ ) 时的表面张力, N/m ; R 1 、 R 2——分别为玻璃液在长度和宽度方向的曲率半径; dg ——玻璃液在成型温度时的密度; g ——重力加速度; 0 &&image.height>0){if(image.width>=700){this.width=700;this.height=image.height*700/image.width;}}">——表面张力形成的附加压强,又称拉普拉斯公式。经运算可得下式: 0 &&image.height>0){if(image.width>=700){this.width=700;this.height=image.height*700/image.width;}}">(2-3-6 ) 玻璃板的抛光作用主要是表面张力,因而表面张力的临界值应不低于静压力值。此时: 0 &&image.height>0){if(image.width>=700){this.width=700;this.height=image.height*700/image.width;}}">(2-3-7 ) 由上可求得λ的临界值λ 0 。 在表面张力作用下,波峰与波谷趋向于平整的速度 V ,可以应用粘滞流体运动的管流公式:0 &&image.height>0){if(image.width>=700){this.width=700;this.height=image.height*700/image.width;}}">(2-3-8 ) 式中:η——玻璃粘度。 应用上述各式可以估算浮法玻璃的抛光时间。 例:设浮法玻璃的成型温度为 1000 ℃,其相应参数分别为:η =10 3 Pa.s 、σ g=350 × 10 -3 N/m 、 dg= 2.4g /cm 3 、 g=1000cm /s 2 。把上述各值代入式 ( 2-3-7 ) 及式 (2-3-8) 可得λ 0 = 2.4cm 、 V=3.5 ×10 -2 cm /s 。因 t= λ /V ,得 t=68.5s 。生产实践表明,若流入锡槽的是均质玻璃液,则它在抛光区内停留时间为 1min左右,就可以获得光亮平整的抛光面,所以上述估算与生产实践相符。 (4)玻璃的拉薄。浮法玻璃的拉薄在工艺上有两种方法,即高温拉薄法与低温拉薄法,如图 2 — 3 — 13 所示。 在高温拉薄时 (1050 ℃ ) 时,其宽度与厚度变化如图 2 — 3 — 13 中 POQ 所示;在低温拉薄 ( 850 ℃ ) 时,其曲线为PBF 。 从图上可以看出,两种不同的拉薄法其效果并不相同。例如,设原板在拉薄前的状态为 P 点,即原板宽度为 5m ,厚为 7mm。若分别用高温拉制法和低温拉制法进行拉薄,若使两者的宽度均为 2.5m ,则相应得 F 点和 0 点,其厚度却分别为 3mm (低温法 ) 和 6mm ( 高温法 ) 。可见用低温法可以拉制更薄的玻璃。若拉制厚度为 4mm 的玻璃,则相应得 B 点和 Q点,其板宽分别为 3m ( 低温法 ) 和 0.75m ( 高温法 ) 。由上可知,采用低温拉薄比高温拉薄更为有利。实际上低温拉薄还可以分为两种,即低温急冷法和低温徐冷法。两者拉薄过程如图 2-3-14所示。 0 &&image.height>0){if(image.width>=700){this.width=700;this.height=image.height*700/image.width;}}">0 &&image.height>0){if(image.width>=700){this.width=700;this.height=image.height*700/image.width;}}">低温急冷法。玻璃在离开抛光区后,进入强制冷却区,使其温度降到 700 ℃ ,粘度为 10 7Pa · s;而后玻璃进入重新加热区,其温度回升到 850 ℃ ,粘度为 10 5 Pa · s ,在使用拉边器情况下进行拉薄,其收缩率达 30%左右。 低温徐冷法。玻璃在离开抛光区后,进入徐冷区,使其温度达 850 ℃ ,再配合拉边器进行高速拉制。这种方法的收缩率可降到28 %以下。 在进行拉薄时必须添加拉边器,其配用台数与拉制的厚度有关,如表 2-3-13 所示。 表 2-3-13 拉边器配用台数玻璃厚度 (mm) 5 4 3 2 1.6 拉边器配用台数 ( 台 ) 1 2-3 3-4 4-5 7 2 .锡液的物理性质 浮抛液在玻璃成型过程中的主要作用是托浮和抛光玻璃,在选用的各种金属及合金中,尤以金属锡液最符合浮法工艺的成型条件,从表 2-3-14~表 2-3-18 中显示了它的综合优点。 表 2-3-14 锡的标准 (GB728-729-65) 牌号 Sn 含量大于 ( % )杂质含量小于 ( % ) As Fe Cu Pb Bi Sb S 01 1 2 3 4 99.95 99.90 99.75 99.5699.00 0.003 0.015 0.02 0.02 0.1 0.004 0.007 0.01 0.02 0.05 0.0040.01 0.03 0.03 0.05 0.003 0.005 0.008 0.3 0.6 0.003 0.015 0.05 0.050.06 0.005 0.015 0.05 0.05 0.15 0.001 0.001 0.01 0.01 0.02 由表2-3-14可知,锡中所含各种杂质都是组成玻璃的元素,它们可以在玻璃成型过程中夺取玻璃中的游离氧成为氧化物,这种不均质的氧化物成为玻璃表面的膜层;当金属锡中的含铁量达0.2 %时会在锡液表面形成铁锡合金 FeSn 2 ,它增加锡液的“硬度”; Al 2 0 3 含量过多会在锡液表面生成 Al 2 O3 薄膜使锡液表面呈现不光滑;杂质 S 能生成 SnS,是形成浮法玻璃缺陷的原因之一。以上都会影响玻璃的抛光度,因此,对于浮抛玻璃用锡液其纯度要求在 99.90 %以上,为此常选用特级锡。 由表 2-3-15 、表 2-3-16 可知,锡的密度大大高于玻璃的密度 ( 2.7g /cm 3 ),有利于对玻璃托浮;锡的熔点 ( 231.96 ℃ ) 远低于玻璃出锡槽口的温度 (650 ~ 700 ℃ ),有利于保持玻璃的抛光面;锡的导热率为玻璃的 60 ~ 70 倍有利于玻璃板面温度的均匀等;锡液的表面张力 [(462 ~ 502)× 10 -3 N/m] 高于玻璃的表面张力 [(220 ~ 380) × 10 -3 N/m] ,有利于玻璃的拉薄。 表2-3-15 锡的物理性质 性 质 单 位 数值 性 质 单 位 数值 密度熔点 沸点 导热率 ( 200C ) g/cm 3 ℃ ℃W/(m · K) 7.298 231.96 2270 65.73 熔化潜热 蒸发潜热 固 - 液相体积变化 表面张力( 232 ℃) J/g J/g % N/m 60.3 3018 2.7 531 × 10 -3 波长 μ m 1 2 4 7 10 12 反光能力% 54 61 72 81 84 85 表 2-3-16 锡液密度、表面张力与温度的关系 温度(℃) 600 700 800 9001000 1050 1100 密度( g/cm 3 ) 60.711 6.643 6.574 6.505 6.437 6.4036.368 表面张力(× 10 -3N/m ) 502 494 486 478 470 466 462 由表 2 — 3 — 17可知,锡液有极低的粘度,这表明有良好的热对流的运动性能,这对均匀浮法表面温度有较大的影响。 表 2-3-17 锡液粘度与温度间关系温度 ( ℃ ) 301 320 351 450 604 750 粘度 (Pa · s) 1.68 × 10 -3 1.593 ×10 -3 1.52 × 10 -3 1.27 × 10 -3 1.045 × 10 -3 0.905 × 10 -3 表2-3-17 锡液粘度与温度间关系 温度 ( ℃ ) 730 880 940 1010 1130 1270 1440 蒸气压 (Pa)1.94 × 10 -4 2.3 × 10 -2 4.13 × 10 -2 0.133 1.33 13.3 133 由表 2 — 3— 18 可知,在浮法玻璃成型温度范围内蒸气压变化在 1.94 × 10 -4 ~ O.133Pa 之间,所以锡液的挥发量极小。使用锡液作浮抛介质的主要缺点是 Sn 极易氧化成 Sn0 及 SnO 2,它不利于玻璃的抛光,同时又是产生虹彩、沾锡、光畸变等玻璃缺陷的主要原因,为此须采用保护气体。 3 .保护气体 在锡槽中引入保护气体的目的在于防止锡的氧化以保持玻璃的抛光度,减少产生虹彩、沾锡、光畸变等缺陷,减少锡的损失等。一般,保护气体由 N2 +H 2 组成,两者可采用如下比例: 表 2-3-19 N 2 与 H 2 的比例 H 2 ( % ) 4 ~ 6 6 ~ 7 8~ 9 N 2 ( % ) 96 ~ 94 94 ~ 93 92 ~ 91 实际上在锡槽各部的 N 2 与 H 2的比例并不相同,在锡槽的进出口处的 H 2 的比例要稍大些。 二、垂直引上法成型 可分为有槽垂直引上法、无槽垂直引上法两种。 0&&image.height>0){if(image.width>=700){this.width=700;this.height=image.height*700/image.width;}}">( 一 ) 有槽垂直引上法 是玻璃液通过槽子砖缝隙成型平板玻璃的方法。其成型过程如图 2 — 3 — 15 所示,玻璃液由通路 1经大梁 3 的下部进入引上室,小眼 2 是供观察、清除杂物和安装加热器用的。进入引上室的玻璃液在静压作用下,通过槽子砖 4的长形缝隙上升到槽口,此处玻璃液的温度约为 920 ~ 960 ℃ 左右,在表面张力的作用下,槽口的玻璃液形成葱头状板根 7,板根处的玻璃液在引上机 9 的石棉辊 8 拉引下不断上升与拉薄形成原板 10 。玻璃原板在引上后受到主水包 5 、辅助水包 6的冷却而硬化。槽子砖是主要的成型设备,其结构如图 2-3-16 所示。 用有槽法生产窗玻璃的过程是玻璃液经槽口成型、水包冷却、机膛退火而成原板,原板经采板而成原片。其中,玻璃性质、板根的成型、边子的成型、原板的拉伸力是玻璃成型机理的四个关键部分。玻璃性质已如前述,以下叙述后三个部分。0 &&image.height>0){if(image.width>=700){this.width=700;this.height=image.height*700/image.width;}}">1.板根的成型 在生产情况下,板根的大小、形状与位置决定于以下四个因素: (1)槽子砖沉入玻璃液深度的影响。槽子砖沉入越深,则槽口的玻璃液就越多,玻璃液在槽口的停留时间增长、冷却增强,所以引上量可增大,反之,则引上量减少。(2)玻璃液温度的影响。若玻璃液的温度升高,导致玻璃液的粘度下降,玻璃液在流动时的内阻减少,使槽口流出的玻璃液量增加,此时,板根上升。反之,则下降。(3) 窑压的影响。当熔化部窑压增加时,熔化部的高温废气压向冷却通路,使玻璃液温度升高,与上述同理使板根上升。反之,则下降。 (4)熔窑玻璃液面波动的影响。玻璃液面的升降将直接影响板根的位置。 2 .边子的成型 在原板的成型过程中,原板的宽度与厚度将同时产生两类收缩。第一类是自然收缩,由热塑状玻璃的表面张力和流动度 ( 粘度 )的共同作用所形成;第二类是强制收缩,热塑状玻璃与其他材料一样,当受到外力作用时,只要有力的传递,就会在纵向受拉时产生横向收缩,其收缩率决定于纵向的拉力大小、材料性质与材料所处温度。由于原板存在纵向拉力,所以在原板的厚度与宽度方向上都将产生强制收缩。所以要得到与槽口长度相等的原板是不可能的。3 .原板的拉伸力 原板在恒速上升时要克服三类矢力:一是原板的自身重力;二是在槽口的玻璃液不断拉伸时形成新的表面,引上后的原板在其固化前厚度不断地变薄而形成二次表面,要克服的第二类矢力是形成新表面所需的表面力;三是沿槽口长度方向上的板根的体积是不相同的,而引上的原板是等厚的,则在引上过程中塑状玻璃内部的质点间存在着速度梯度,这种速度梯度不仅存在于原板的宽度上,也存在于原板的厚度上,这就形成了玻璃液的粘滞力。 提高引上速度就相应地提高了原板的拉伸力,它伴随纵向拉力的增加产生横向的收缩也增加,在此时有两种情况:其一,当边子的自由度较大时,边子向内收缩,维持原有的厚度引上,即提高引上速度并不能使原板变薄;其二,当边子两边添置拉边器时,边子的自由度极小,即纵向受拉时横向收缩较小,因而由于提高引上速度而增加的拉伸力必然导致玻璃液质点间的相对位移增加,这使原板变薄。反之,则变厚。0 &&image.height>0){if(image.width>=700){this.width=700;this.height=image.height*700/image.width;}}">(二 ) 无槽垂直引上法 图 2 — 3 — 17为无槽引上室的结构示意图。可以看出,有槽与无槽引上室设备的主要区别是:有槽法采用槽子砖成型,而无槽法采用沉入玻璃液内的引砖并在玻璃液表面的自由液面上成型。 由于无槽引上法采用自由液面成型,所以由槽口不平整 ( 如槽口玻璃液析晶、槽唇侵蚀等 )引起的波筋就不再产生,其质量优于有槽法,但无槽引上法的技术操作难度大于有槽引上法。 ( 三 ) 平拉法成型 平拉法与无槽垂直引上法都是在玻璃液的自由液面上垂直拉出玻璃板。但平拉法垂直拉出的玻璃板在 500 ~ 700m没高度处,经转向辊转向水平方向,由平拉辊牵引,当玻璃板温度冷却到退火上限温度后,进入水平辊道退火窑退火。玻璃板在转向辊处的温度约620 ~ 690 ℃ 。图 2 — 3 — 18 为平拉法成型示意图。 ( 四 ) 压延法成型 用压延法生产的玻璃品种有:压花玻璃 (2 ~ 12mm 厚的各种单面花纹玻璃 ) 、夹丝网玻璃 ( 制品厚度为 6 ~ 8mm )、波形玻璃(有大波、小波之分,其厚度为 mm 左右 ) 、槽形玻璃 ( 分无丝和夹丝两种,其厚度为 7mm ) 、熔融法制的玻璃马赛克( 生产 2Omm × 20mm 、 25mm × 25mm 的彩色玻璃马赛克 )、熔融法制的微晶玻璃花岗岩板材(晶化后的板材再经研磨抛光而成制品,板材厚度为 10 ~ 0 &&image.height>0){if(image.width>=700){this.width=700;this.height=image.height*700/image.width;}}">15mm) 。目前,压延法已不用来生产光面的窗用玻璃和制镜用的平板玻璃。压延法有单辊压延法和对辊压延法之分。 单辊压延法是一种古老的成型方法。它是把玻璃液倒在浇铸平台的金属板上,然后用金属压辊滚压而成平板 [ (如图 2 — 3 —19(a)] ,再送入退火炉退火。这种成型方法无论在产量、质量上或成本上都不具有优势,是属淘汰的成型方法。 连续压延法是玻璃液由池窑工作池沿流槽流出,进入成对的用水冷却的中空压辊,经滚压而成平板,再送入退火炉退火。采用对辊压制的玻璃板两面的冷却强度大致相近。由于玻璃液与压辊成型面的接触时间短,即成型时间短,故采用温度较低的玻璃液。连续压延法的产量、质量、成本都优于单辊压延法。各种压延法示于图2 — 3 — 19 中。 0 &&image.height>0){if(image.width>=700){this.width=700;this.height=image.height*700/image.width;}}">图 2-3-19 压延法 对压延玻璃的成分有如下要求:在压延前玻璃液应有较低的粘度以保持良好的可塑性,在压延后,玻璃的粘度应迅速增加,以保证固型,保持花纹的稳定与花纹清晰度,制品应有一定的强度并易于退火。对夹丝网玻璃所用丝网有以下要求: (1) 丝网的热膨胀系数应与玻璃匹配; (2)丝网与玻璃不起化学反应,防止碳素钢中的碳素与玻璃中游离氧生成 CO 2 , (3)丝网应有一定的强度和熔点,防止在夹入过程中发生拉断与熔断; (4) 丝网应具有磁性,以便在处理碎玻璃时容易除去; (5)在掰断夹丝网玻璃时丝网应比较容易掰断; (6) 价格便宜易于采购。 通常采用的丝网直径为 O.46 ~ O.53 没 m 的含18Cr 的低碳钢。 第七节 玻璃的缺陷 玻璃缺陷的形成与各工艺环节是否正常进行有密切关系,如配合料的质量、熔制过程、成型以及退火等都能产生各种玻璃缺陷。通常的所谓玻璃缺陷主要是指制品中的气泡、线道、节瘤及结石,这些缺陷的存在不仅影响玻璃的外观质量,而且也影响使用性能。有上述缺陷的制品,在使用过程中极易炸裂。玻璃退火不良存在永久应力也属玻璃缺陷,见第七节玻璃的退火。各种玻璃制品还有其特有的缺陷,如浮法玻璃中的光畸变,玻璃瓶壁的厚薄差、颜色玻璃中的色差、光学玻璃中的浇铸条纹等都是玻璃缺陷。 不同的玻璃品种对缺陷程度有各种不同的要求。例如,对光学玻璃,即使肉眼看来不明显的条纹也是不允许存在的;在厚壁瓶罐玻璃中一般可容许一些条纹或尺寸小的气泡,但在器皿玻璃中同样的条纹与气泡就要作为疵病来对待}对玻璃缺陷要求不严格的制品是熔融法制造的玻璃马赛克,它容许同时存在气泡、条纹、砂粒等而不视为废品或等外品,这是由于玻璃马赛克制品本身的特点所决定,因其面积小、乳浊而不透明、彩色,并要求有未熔化的砂粒。 通常,生产中应尽量减少气泡、条纹、结石等缺陷。因此,研究玻璃缺陷形成的原因并提出相应的措施对提高玻璃制品的产质量有着重要作用。 ?气泡的类型与形成的原因 玻璃制品常以气泡的直径及单位体积内的气泡个数来划分等级。制品中气泡的形状可呈球形、椭圆形、细长形,它的变形与成型过程有关。大部分气泡为无色透明的,也可呈有色的,如白色芒硝泡。气泡直径过小的称灰泡或尘泡。气泡中的气体有:0 2 、 N 2 、 H 2 O 、 CO 2 、 CO 、 H 2 、 SO 2 、 H 2 S 、 NO 2等。有时气泡为真空泡或空气泡。 通常气泡的形成有以下几种原因: 1 .残留气泡的形成 在玻璃熔制过程中,粉料中的各种盐类等都将在高温下分解,放出的大量气体不断地从熔体中排除。熔体进入澄清阶段还继续排除气泡。为加速排除气泡,一般采用高温熔制以降低玻璃液的粘度,或加入降低表面张力的物质,或使窑内压力降低以使气泡逸出。但尽管如此,有些气泡仍然会残留在玻璃液内,或者由于玻璃液与炉气相互作用后又产生气泡而又未能及时排除,这就形成了残留气泡。 要防止这种缺陷,必须严格遵守配料与熔制制度,或调整熔制温度、改变澄清剂种类和用量,或适当改变玻璃成分,使熔体的粘度和表面张力降低等。以上都是有利于排除玻璃液中气泡的措施。2 .二次气泡的形成 二次气泡的形成可以有两种原因,即物理的和化学的。 玻璃液澄清结束后,玻璃液处于气液两相平衡状态,若降温后的玻璃液又一次升温超过一定限度,原溶解于玻璃液中的气体由于温度增高而引起溶解度的下降,所以析出了极细小的、分布均匀的、数量极多的气泡,这就是二次气泡。这种情况属于物理上的原因。 由于化学上原因产生二次气泡的成因可以有多种多样。在使用芒硝的玻璃液中,未分解完全的芒硝在冷却阶段继续分解而形成二次气泡;含钡玻璃由于过氧化钡在低温时的分解形成次气泡;以硫化物着色的玻璃与含硫酸盐的玻璃接触也产生二次气泡等。 由于二次气泡产生于玻璃液的低温状态下,其粘度很大,因而微小的气泡极难排除,且由于玻璃液是高粘滞液体,要建立新的平衡是比较缓慢的。由于二次气泡的成因不同,为防止二次气泡应有相应的措施。3 .耐火材料气泡的形成 玻璃液与耐火材料相互进行物理化学作用而产生气泡。 耐火材料本身有一定的气孔率,当与玻璃液接触后,因毛细管作用,玻璃液进入缝隙而将气体挤出而成气泡,耐火材料的气孔率比较大,因而放出的气体量是相当可观的。 耐火材料所含铁的氧化物对玻璃液中残留的盐类的分解起着催化作用,这使玻璃液产生气泡。 由还原焰烧成的耐火材料,在其表面上或缝隙中会留有碳素,这些碳索与玻璃液中的变价氧化物作用而生成气泡。 为防止这类气泡的产生,必须提高耐火材料的质量降低气孔率,并在熔制工艺操作上严格遵守作业制度减少温度的波动。 4 .铁器引起的气泡 在冷修或热修玻璃熔窑时,可能会在窑中落入铁器,在很长时间内铁器将逐步氧化并溶解于玻璃液中,使玻璃着成褐色,而铁中的碳也将氧化成 CO及 CO 2 而形成气泡。由此可见由铁器引起的气泡在其周界上往往伴随有褐色的玻璃膜。 5 .其他气泡形成的原因 由于粉料颗粒间的空气在高温熔化时未能及时排除,或由成型时因挑料而带入的空气,或搅拌叶带入的空气等都可以形成空气泡。当玻璃表面遭受急冷而使外层结硬,而内层还将继续收缩,这时只要内层中有极小的气泡就造成了真空条件,使极小的气泡迅速长大而形成了真空泡。在玻璃电熔过程中,如果电流密度过大,在电极附近就会产生氧气泡。二、玻璃状夹杂物及其形成原因 在主体玻璃内存在异类玻璃夹杂物称玻璃状夹杂物(通常是指条纹、线道和节瘤 )。它是属于一种比较普遍的玻璃缺陷。由于两者成分和性质不同,其结果不仅影响外观,也可使界面上的力学强度、耐热性、密度、粘度、折射率、表面张力、色泽上与主体玻璃不同,这使制品的使用性能降低。 线道多是由于玻璃液中存在着尚未均化的、粘度高、表面张力大的玻璃在拉制成型过程中形成的;结节由结石与周围玻璃液中的组分在长期高温下作用而成,或由碹滴转化而成玻璃状团块;条纹是早期形成的不均匀玻璃液在液流作用下和在搅拌过程中被分散而尚未扩散均化而成的细小条带。这三种玻璃状夹杂物中前两种的缺陷对制品质量的影响最大。虽然条纹也影响质量,但对有些制品,如包装用瓶罐及低档的器皿等,在一定程度上还容许存在,但对光学玻璃却是绝对不容许的。玻璃状夹杂物按它们的化学成分来分,主要有硅质与铝硅质两大类,现分述如下: 1 .硅质玻璃状夹杂物由富硅质玻璃产生的线道、结节和条纹,主要是因原料配制及熔制不当及耐火材料的侵蚀而引起的。当粉料混和极不均匀时,常形成砂蛋,即形成富硅质的料团,在长期高温作用下料团虽熔化成玻璃体,但未能及时扩散而成为结节;因分层使 SiO2 在粉料中各处含量不均,它在熔制后形成了富硅质条纹。另外,石英颗粒的颗粒组成不当,粗颗粒极易形成条纹。在熔制时,若配合料采用大料堆的加料方法,料堆表面的易熔组分很容易由高处往低处流,造成了料堆上层难熔的 SiO 2增多,即发生了熔化分层。由硅质耐火材料侵蚀下来的物质也形成硅质线道与结节。池窑中的胸墙及碹顶大多采用硅砖来砌筑,在使用过程中这些砖的表面都会发生侵蚀,若炉龄过长或炉温过高对其侵蚀加剧,侵蚀后的形成物,或以熔溜物沿砖表面淌下,或以碹滴掉下,有时虽呈晶态物质,但经长期高温熔化一般均可玻璃化,由于来不及扩散而呈玻璃状夹杂物。由于富硅质玻璃状夹杂物的密度和折射率均小于主体玻璃,这可作为鉴别的依据。 2 .铝硅质玻璃状夹杂物它大部分来自电熔砖、粘土砖、高铝砖等耐火材料的侵蚀,或玻璃配合料中混入高铝质的粘土所致。铝硅质耐火材料的侵蚀程度往往与耐火材料的质量密切相关,结构不致密的耐火砖因存在缝隙,玻璃液很容易从毛细孔或微细裂纹处渗进,随着组分间的扩散交代作用而进一步深入耐火砖,并形成富铝质的玻璃。若这种玻璃附着于砖体表面,由于其粘度和表面张力都很大,可以在砖表面形成一层保护层,使砖体的侵蚀变得缓慢。但当熔制温度发生波动,或液面波动过于频繁,液流即被扰乱,在窑体结构的相应部位侵蚀下来的高粘度高表面张力的玻璃便进入主体玻璃中形成了线道或条纹。当耐火砖表面受到侵蚀后,砖体碎屑可能剥落下来,经长期高温作用也可由晶相转为玻璃相,若不能充分均化就形成铝硅质结节。电熔耐火材料的显微结构不适当,则在砖体内部易造成粗晶和空洞,并因此而产生裂纹,这将导致侵蚀加速,尤其是炉温过高或炉温波动频繁则更甚。三、结石的类型与形成的原因结石是出现在玻璃中的结晶夹杂物。结石是玻璃制品中最严重的缺陷,它破坏了玻璃制品的外观和光学均匀性,另外,由于结石与主体玻璃的热膨胀系数不同,因而在制品加热或冷却过程中造成界面应力,它是制品出现裂纹和炸裂的主要原因。根据结石的成因,它可以分为以下几类: 1 .配合料结石配合料结石是配合料中未熔化的颗粒,在大多数情况下是石英颗粒,色泽呈白色,其边缘由于逐渐溶解而变圆,其表面常有沟槽,在石英颗粒周围有一层SiO2含量较高的无色圈,它粘度高不易扩散,常导致形成粗筋。石英颗粒的边缘往往会出现方石英和鳞石英的晶体。配合料结石的产生不仅与配合料的制备质量有关,也与熔制的加料方式、熔制温度的高低与波动等有关。常见的结石有方石英及鳞石英。2 .耐火材料结石当耐火材料受到侵蚀剥落,或在高温下玻璃液与耐火材料相互作用后有些碎屑就可能夹杂到玻璃制品中而形成耐火材料结石。窑碹、胸墙常用硅砖砌成,在高温下或者在碱性飞料的影响下会产生蚀变,有时形成熔溜物淌下,或以碹滴落入玻璃液中,这是耐火材料结石的另一种来源。因此,要减少耐火材料结石,必须选用优质耐火材料。一般而言,耐火材料的气孔率、结构致密度、显微结构的均匀度、砌筑质量、熔化温度、玻璃液本身的碱性程度、熔化分层、所用原料种类等都与其有密切关系。常见的耐火材料结石为铝硅质结石如莫来石、霞石、白榴石等。 3 .析晶结石 均质的玻璃液在一定温度下又析出晶体即为析晶结石。玻璃中的析晶结石往往使玻璃产生迷漠的白点,或呈现具有明显结晶态的产物。析晶结石特别容易发生在两相界面上。例如,在玻璃液的表面上、气泡上、与耐火材料接触的界面上。玻璃成分对产生析晶结石有明显的影响,因为成分不同其晶核生成速度及晶体成长速度都不同,在成分上应选择析晶倾向小的氧化物,降低易析晶氧化物的含量。另外,对产生析晶有较大影响的是窑炉的温度制度与窑的结构,前者应使玻璃液尽量少在析晶温度范围内停留,而后者应尽量使玻璃液滞留的死角减少。析晶结石通常有鳞石英与方石英 (SiO 2 ) 、硅灰石 (CaO · SiO 2 ) 、失透石 (Na 2 O · 3CaO ·6Si0 2 ) 、透辉石 (CaO · MgO · 2Si0 2 ) 及二硅酸钡 (BaO · 2Si0 2 ) 等。 4.硫酸盐夹杂物 玻璃熔体中所含硫酸盐若超过所能溶解的量,它就会以硫酸盐的形式成为浮渣析出,在冷却后硬化而成结晶体。 5 .黑色夹杂物在玻璃中也常见黑色夹杂物,它们直接或间接由配合料而来,常见的有氧化铬晶体、氧化镍晶体、铬铁晶体等。 第八节 玻璃的退火在生产过程中,玻璃制品经受激烈的、不均匀的温度变化,会产生热应力。这种热应力能降低玻璃制品的强度和热稳定性。热成型的制品若不经退火令其自然冷却,则在冷却、存放、使用、加工过程中会产生炸裂。退火就是消除或减少玻璃制品中的热应力至允许值的热处理过程,不同玻璃制品有不同的要求,如表 2 — 3 — 20 所示。薄壁制品 (如灯泡等 )和玻璃纤维在成型后由于热应力很小,除适当地控制冷却速度外,一般都不再进行退火。若玻璃表面层具有有规律的、均匀分布的压应力就能提高玻璃的强度和热稳定性。玻璃的淬火增强就是应用这一原理。表 2-3-20 各种玻璃的容许应力(以光程差表示 ) 玻璃种类 nm/cm 玻璃种类 nm/cm 光学玻璃精密退火 光学玻璃粗退火望远镜、反光镜 平板玻璃 2 ~ 5 10 ~ 30 20 20 ~ 95 镜玻璃 空心玻璃 玻璃管 瓶罐玻璃 30 ~ 40 60120 50 ~ 400 ? 玻璃的应力 玻璃中的应力一般可分为三类:热应力、结构应力及机械应力。玻璃中的热应力是由于玻璃中存在温差而产生的应力,按其产生的特点可分为暂时应力和永久应力两类。 1 .暂时应力在温度低于应变点时,处于弹性变形温度范围内 ( 即脆性状态 )的玻璃在经受不均匀的温度变化时所产生的热应力,随温度梯度的存在而存在,随温度梯度的消失而消失,这种应力称为暂时应力。把温度低于应变点以下的、无应力的玻璃板进行双面均匀自然冷却,则玻璃表面层的温度急剧下降,由于玻璃的导热系数低,故内层冷却缓慢,由此在玻璃内部产生了温度梯度,沿厚度方向的温度场分布呈抛物线形,如图2 — 3 — 20 实线所示。玻璃在冷却过程中处于较低温度的外层收缩量应大于内层,但由于受到内层的阻碍而不能收缩到正常收缩量,所以外层产生了张应力,内层处于压缩状态而产生了压应力。这时玻璃厚度方向的应力分布是外层为张应力,内层为压应力,其应力分布呈抛物线形,如图2 — 3 — 20 虚线所示。在玻璃中间的某层,压应力和张应力大小相等,应力方向相反,相互抵消,该层应力为零,称中性层。玻璃继续冷却,当表面层冷却到室温后,表面温度不再下降,其体积也不再收缩,但内层温度高于外层,它将继续降温收缩,这样外层开始受到内层的拉引而产生压应力,此部分应力将部分抵消冷却开始时所受到的张应力,而内层收缩时受到外层的拉伸呈张应力,将部0 &&image.height>0){if(image.width>=700){this.width=700;this.height=image.height*700/image.width;}}">分图 2-3-20 玻璃暂时应力产生的示意图抵消冷却开始时的压应力。随着内层温度不断下降,外层的张应力和内层的压应力不断相互抵消,当内外层温度一致时,玻璃中不再存在应力.反之,若玻璃板由室温开始加热,直到应变点以下某温度保温时,其温度变化曲线与应力变化曲线恰与上述相反。暂时应力虽然随温度梯度的消失而消失,但其应力值应严加控制,若超过了玻璃的抗张强度的极限,玻璃会发生炸裂。通常应用这一现象以骤冷的方法来切割玻璃制品及玻璃管、玻璃棒等。2 .永久应力 当玻璃内外温度相等时所残留的热应力称永久应力。将一块玻璃板加热到高于玻璃应变点以上的某一温度,待均热后板两面均匀自然冷却,经一定时间后玻璃中温度场呈抛物线分布,如图 2-3 —21所示。玻璃外层为张应力而内层为压应力,由于应变点以上的玻璃具有粘弹性,即此时的玻璃为可塑状态,在受力后可以产生位移和变形,使由温度梯度所产生的内应力消除。这个过程称为应力松弛过程,这时的玻璃内外层虽存在着温度梯度但不存在应力。当玻璃冷却到应变点以下,玻璃已成为弹性体,以后的降温与应力变化与前述的产生暂时应力的情况相同,待冷却到室温时虽然消除了应变点以下产生的应力,但不能消除应变点以上所产生的应力,此时,应力方向恰相反,即表面为压应力,内部为张应力,这种应力为永久应力,如图2 — 3 — 21 所示。 0 &&image.height>0){if(image.width>=700){this.width=700;this.height=image.height*700/image.width;}}">图2-3-21 玻璃永久应力产生的示惹图 3 .玻璃中的结构应力玻璃因化学组成不均导致结构上的不均而产生的应力称结构应力。它是属于永久应力,玻璃即使经退火也不能消除这种应力。玻璃中的成分不均体,其热膨胀系数与主体玻璃不相同,因而主体玻璃与不均体的收缩、膨胀量也不相同,在其界面上产生了应力,所以,退火也不能消除这类应力。例如,当玻璃中存在结石、条纹和节瘤时,就会在这些缺陷的界面上引起应力。4 .机械应力 由外力作用在玻璃上弓 I起的应力,当外力除去时该应力随之消失,此应力称机械应力。在生产过程中,若对玻璃制品施加过大的机械力也会使玻璃制品破裂。二、玻璃的退火工艺 为了消除玻璃中的永久应力,必须把玻璃加热到低于玻璃转变温度 Tg附近某一温度进行保温均热,以消除玻璃各部分的温度梯度,使应力松弛,这个选定的保温均热温度称玻璃的退火温度。玻璃在退火温度下,由于粘度很大还不会发生可测得的变形。玻璃的最高退火温度是指在此温度下经过3min 能消除 95 %的应力,此温度亦称退火上限温度;最低退火温度是指在此温度下经 3min 只能消除 5%的应力,此温度亦称退火下限温度。最高退火温度和最低退火温度之间为退火温度范围。 大部分器皿玻璃的最高退火温度为 550 ± 20 ℃,平板玻璃为 550 ~ 570 ℃ 、瓶罐玻璃为 550 ~ 600 ℃ 。实际上,一般采用的退火温度都比最高退火温度低 20 ~30 ℃ ,低于最高退火温度 50 ~ 150 ℃ 的为最低退火温度。玻璃的退火温度与其化学组成有关。凡能降低玻璃粘度的组成也能降低退火温度,如碱金属氧化物 Na 2 0 、 K 2 O 等。 SiO 2、 Al 2 O 3 、 CaO 等都增加玻璃粘度,所以随着它们含量的增加其退火温度都提高。玻璃的退火制度与制品的种类、形状、大小、容许的应力值、退火炉内温度分布等情况有关。目前采用的退火制度有多种形式。根据退火原理,退火工艺可分为四个阶段:加热阶段、均热阶段、慢冷阶段和快冷阶段。按上述四个阶段可作出温度-时间曲线,此曲线称退火曲线,示于图2 — 3 — 22 。 0 &&image.height>0){if(image.width>=700){this.width=700;this.height=image.height*700/image.width;}}">1 .加热阶段不同品种的玻璃有不同的退火工艺。有的玻璃在成型后直接进入退火炉进行退火,称为一次退火;有的制品在成型冷却后再经加热退火,称为二次退火。所以加热阶段对有些制品并不是必要的。在加热过程中,玻璃表面产生压应力,所以加热速率可相应高些,例如20 ℃ 的平板玻璃可直接进入 700 ℃ 的退火炉,其加热速率可高达 300 ℃ / rain。考虑到制品大小、形状、炉内温度分布的不均性等因时间素,在生产中一般采用的加热速率为 20/a 2 ~ 30/a 2 ( ℃/min) ,对光学玻璃制品的要求更高,一般为 <5/a 2 ,式中 a 为制品的厚度之半,其单位为 cm 。 2 .均热阶段把制品加热到退火温度进行保温、均热以消除应力。在本阶段中首先要确定退火温度,其次是保温时间。一般把比退火上限温度低 20 ~ 30 ℃作为退火温度。退火温度除直接测定外,也可根据玻璃成分计算粘度为 10 12 Pa · s 时的温度。当退火温度确定后,保温时间可按70a 2 ~ 120a 2 进行计算,或者按应力容许值进行计算: 0 &&image.height>0){if(image.width>=700){this.width=700;this.height=image.height*700/image.width;}}">(2-3-9 ) 式中:△ n ——玻璃退火后容许存在的内应力, nm / cm 。 3 .慢冷阶段为了使玻璃制品在冷却后不产生永久应力,或减小到制品所要求的应力范围内,在均热后进行慢冷是必要的,以防止过大的温差。按下式计算冷却速度:0 &&image.height>0){if(image.width>=700){this.width=700;this.height=image.height*700/image.width;}}">(2-3-10 ) 对一般工业玻璃 : 0 &&image.height>0){if(image.width>=700){this.width=700;this.height=image.height*700/image.width;}}">(2-3-11 ) 0 &&image.height>0){if(image.width>=700){this.width=700;this.height=image.height*700/image.width;}}">MPa=1.3 0 &&image.height>0){if(image.width>=700){this.width=700;this.height=image.height*700/image.width;}}">nm/ cm 此阶段冷却速度的极限值为: 10 / a 2 ( ℃/ rain) ,每隔 10 ℃ 冷却速度增加 0 . 2 ℃ /min ,所以也可按下式计算: 0 &&image.height>0){if(image.width>=700){this.width=700;this.height=image.height*700/image.width;}}">℃/min ( 2-3-12 ) 式中: h 0 ——开始时的冷却速度; h t ——在 t ℃时的冷却速度。4 .快冷阶段玻璃在应变点以下冷却时,如前述只产生暂时应力,只要它不超过玻璃的极限强度,就可以加快冷却速度以缩短整个退火过程、降低燃料消耗、提高生产率。此阶段的最大冷却速度可按下式计算:h c =65 / a 2 ( 2-3-13 )在生产上,一般都采用较低的冷却速度,这是由于制品或多或少存在某些缺陷,以免在缺陷与主体玻璃间的界面上产生张应力。对一般技术玻璃采用此值的15 %~ 20 %,甚至采用: 0 &&image.height>0){if(image.width>=700){this.width=700;this.height=image.height*700/image.width;}}">(2-3-14 ) 上述参数确定后,通常还应在生产实践中加以调整。 第九节 平板玻璃的性能 表 2-3-21 ~表 2-3-23列出了平板玻璃的主要使用性能。表 2-3-21 平板玻璃的光学性能 入射光角度 ( 度 ) 光透过率 ( % ) 0 20 45 6075 92 90 88 83 60 波长 (nm) 透过率 ( % ) 400 450 500 550 600 650 700 4355 67 64 52 37 31 玻璃每面反射率 ( % ) 玻璃光吸收率 ( % ) 玻璃色调 3.5 ~4 1~3浅蓝绿色、浅黄绿色 紫外线透过率( % ) 红外线透过率( % ) 玻璃折射率 不大 10 ~ 25 约 1.5 表 2-3-22平板玻璃的热学性能 软化温度范围 ( ℃ ) 530 ~ 570 在 20 ~ 300 ℃ 间热膨胀系数 ( ℃ -1 ) (80 ~95) × 10 -7 导热系数 KJ/(www.cnshaifen.com) 20 ℃ 3.351200 ℃ 9.62 比热 KJ/( Kg.K ) 20 ℃ 0.841200 ℃ 1.26 玻璃厚度 (mm) 2 3 4 5 6 玻璃的热稳定性 ( ℃ )试样破损为 0 时的温度差试样破损为 50 %时的温度差试样破损为 100 %时的温度差 100 75 65 62 60138 11698 85 78180 140 120 110 100 表 2-3-23 平板玻璃的力学性能与声学性能 ┃ 莫氏硬度抗压强度(MPa)抗拉强度 (MPa)抗弯强度 (MPa)弹性模数 (MPa) 6 ~ 7860 ~ 91029 ~ 88平均 4469 ~74 声音在玻璃中速度 (m/s)玻璃厚度 (mm)吸音能力 (dB)密度 (g / cm 3 ) 约 5400? 5约 22 约302.5