摘要:本文从环氧树脂的特性出发,分析了以环氧树为基体的复合材料的常用生产技术,典型产品,并介绍了国内外的有关情况。
一、前言
相比传统材料,复合材料具有一系列不可替代的特性,自二次大战以来发展很快。尽管产量小(据法国Vetrotex公司统计,全球复合材料达700万吨),但复合材料的水平已是衡量一个国家或地区科技、经济水平的标志之一。美、日、西欧水平较高。北美、欧洲的产量分别占全球产量的33%与32%,以中国(含台湾省)、日本为主的亚洲占30%。中国大陆2003年玻璃纤维增强塑料(玻璃纤维与树脂复合的复合材料、俗称“玻璃钢”)逾100万吨,已居世界第二位(美国2003年为169万吨,日本不足70万吨)。
复合材料主要由增强材料与基体材料两大部分组成:
增强材料:在复合材料中不构成连续相,赋于复合材料的主要力学性能,如玻璃钢中的玻璃纤维,CFRP(碳纤维增强塑料)中的碳纤维就是增强材料。
基体:构成复合材料连续相的单一材料,如玻璃钢(GRP)中的树脂(本文谈到的环氧树脂)就是基体。
按基体材料不同,复合材料可分为三大类:
树脂基复合材料
金属基复合材料
无机非金属基复合材料,如陶瓷基复合材料、水泥基复合材料、碳基复合材料等。
本文讨论环氧树脂基复合材料。
1、为什么采用环氧树脂做基体?
·固化收缩率低,仅1%-3%,而不饱和聚酯树脂却高达7%-8%;
·粘结力强;
·有B阶段,有利于生产工艺;
·可低压固化,挥发份甚低;
·固化后力学性能、耐化学性佳,电绝缘性能良好。
值得指出的是环氧树脂耐有机溶剂、耐碱性能较常用的酚醛与不饱和聚酯树脂为佳,然耐水性、耐酸性差;固化后一般较脆,韧性较差。
2、环氧玻璃钢性能(按ASTM)
以FW(纤维缠绕)法制造的玻纤增强环氧树脂的产品为例,将其与钢比较。
表1 GF/EPR与钢的性能比较
GF/EPR(玻纤含量80wt%)
AISI1008 冷轧钢
相对密度
2.08
7.86
拉伸强度
551.6Mpa
331.0MPa
拉伸模量
27.58GPa
206.7GPa
伸长率
1.6%
37.0%
弯曲强度
689.5MPa
弯曲模量
34.48GPa
压缩强度
310.3MPa
331.0MPa
悬臂梁冲击强度
2385J/m
燃烧性(UL-94)
V-O
比热容
535J/kg·k
233J/kg·k
膨胀系数
4.0×10-6k-1
6.7×10-6k-1
热变形温度
204oC(1.82MPa)
热导率
1.85W/m·k
33.7W/m·k
介电强度
11.8×106V/m
吸水率
0.5%(24h)
表2 几种常用材料与复合材料的比强度和比模量
材料名称
密度g/cm3
拉伸强度×104MPa
弹性模量×106MPa
比强度×106cm
比模量×109cm
钢
7.8
10.10
20.59
0.13
0.27
铝
2.8
4.61
7.35
0.17
0.26
钛
4.5
9.41
11.18
0.21
0.25
玻璃钢
2.0
10.40
3.92
0.53
0.21
碳纤维/环氧树脂
1.45
14.71
13.73
0.21
碳纤维/环氧树脂
1.6
1049
23.54
1.5
芳纶纤维/环氧树脂
1.4
13.73
7.85
0.57
硼纤维/环氧树脂
2.1
13.53
20.59
1.0
硼纤维/铝
2.65
9.81
19.61
0.75
玻璃纤维含量%
Kevlar/环氧(60)
S-玻璃/环氧(60)
高强度型碳/环氧(60)
硼/环氧(50)
高刚性型碳/环氧(60)
硼/铝(50)
积层
钛
钢
铝
图1 复合材料的比强度与比刚性
二、纤维增强环氧树脂复合材料成型工艺简介
1、手糊成型 (hand lay up)
图2 手糊成型示意图
(1)概要 依次在模具表面上施加
脱模剂
胶衣
一层粘度为0.3-0.4PaS的中等活性液体热固性树脂(须待胶衣凝结后)
一层纤维增强材料(玻纤、芳纶、碳纤维......),纤维增强材料有表面毡、无捻粗纱布(方格布)等几种。以手持辊子或刷子使树脂浸渍纤维增强材料,并驱除气泡,压实积层。铺层操作反复多次,直到达到制品的设计厚度。
树脂因聚合反应,常温固化。可加热加速固化。
(2)原材料
树脂环氧树脂
纤维 玻纤、碳纤、芳纶等。虽然厚的芳纶织物难于手工将树脂浸透,亦可用。
芯材 任意。
(3)优点
1)适合少量生产;
2)可室温成型,设备投资少,模具折旧费低;
3)可制造大型制品和型状复杂产品;
4)树脂和增强材料可自由组合,易进行材料设计;
5)可采用加强筋局部增强,可嵌入金属件;
6)可用胶衣层获得具有自由色彩和光泽的表面(如开模成型则一面不平滑);
7)玻纤含量较喷射成型高。
无捻粗纱布 50%左右
织物 35%-45%
短切原丝毡 30%-40%
(4)缺点
1)属于劳动密集型生产,产品质量由工人训练程度决定;
2)玻纤含量不可能太高;树脂需要粘度较低才易手工操作,溶剂量高,力学与热性能受限制;
3)手糊用树脂分子量低;通常可能较分子量高的树脂有害于人的健康和安全。
(5)典型产品
舰艇、风力发电机叶片、游乐设备、冷却塔壳体、建筑模型。
2、树脂传递成型(RTM)
图3 树脂传递成型示意图
(1) 概要
RTM是一种闭模低压成型的方法。
将纤维增强材料置于上下模之间;合模并将模具夹紧;在压力下注射树脂;树脂固化后打开模具,取下产品。
树脂胶凝过程开始前,必须让树脂充满模腔,压力促使树脂快速传递到模个内,浸渍纤维材料。
RTM是一低压系统,树脂注射压力范围0.4-0.5MPa,当制造高纤维含量(体积比超过50%)的制品,如航空航天用零部件时,压力甚至达0.7MPa。
纤维增强材料有时可预先在一个模具内预成型大致形状(带粘结剂),再在第二个模具内注射成型。
为了提高树脂浸透纤维能力,可选择真空辅助树脂传递成型(VARTM-vacuum assisted resin transfer molding)。
注意树脂一经将纤维材料浸透,树脂注口要封闭,以便树脂固化。注射与固化可在室温或加热条件下进行。模具可以复合材料与钢材料 制作。若采用加热工艺,宜用钢模。
(2)原材料
树脂:一般多用环氧、不饱和聚酯、乙烯基脂及酚醛;当加温时,高温树脂如双马来酰亚胺树脂亦可用。
法国 Vetrotex公司开发了热塑性树脂RTM。
纤维:任意。常用玻纤连续毡、缝编材料(其纤维间的缝隙利于树脂传递)、无捻粗纱布;玻纤与热塑性塑料的复合纱及其织物与片材(法国Vetrotex商品名TWINTEX)。
芯材:不用蜂窝,因蜂窝空格全被树脂填满,压力会导致其破坏。可用耐溶剂发泡材料PU、PP、CLVC等。
(3)优点
1)制品纤维含量可较高,未被树脂浸得部分非常少;
2)闭模成型,生产环境好;
3)劳动强度低,对工人技术熟练程度的要求也比手糊与喷射成型低;
4)制品两面光,可作有表面胶衣的制品,精度也比较高;
5)成型周期较短;
6)产品可大型化;
7)强度可按设计要求具有方向性;
8)可与芯材、嵌件一体成型;
9)相对注射设备与模具成本较低。
(4)缺点
1)不易制作较小产品;
2)因要承压,故模具较手糊与喷射工艺用模具要重和复杂,价位也高一些;
3)能有未被浸渍的材料,导致边角料浪费。
(5)典型产品
小型飞机与汽车零部件、客车座椅、仪表壳
3、纤维缠绕(FW)
图4 纤维缠绕示意图
(1)概要
通常采用直接无捻粗纱作为增强材料。粗纱排列在纱架上。粗纱自纱架上退绕,通过张力系统、树脂槽、绕丝嘴,由小车带动其往复移动并缠绕在回转的芯轴(模)上。纤维缠绕角度与纤维排列密度根据强度设计,并由芯轴(模)转速与小车往复速度之比,精确地控制。固化后将缠绕的复合材料制品脱模。
对某些两端密闭的产品不用脱模,芯模即包在复合材料产品内,作为内衬。
(2)原材料
树脂:任意。多用环氧、不饱和聚酯、乙烯基脂及酚醛树脂。
纤维:任意。无捻粗纱、缝编和无纺织物。生产管罐时,常用表面毡、短切原丝作为内衬材料。
芯材:可用。虽然复合材料制品通常是单一壳体,一般不用。
(3)优点
1)因为纤维迳直以合理的线型铺设,承担负荷,故复合材料制品的结构特性可非常高;
2)由于同内衬层组合,可制得耐腐蚀、耐压、耐热的制品;
3)可制造两端封闭的制品;
4)铺放材料快、经济、用无捻粗纱,材料费用低;
5)可采用树脂计量,然浸胶后的纤维通过挤胶或口模,控制树脂含量;
6)可大量生产和自动化;
7)机械成型,复合材料材质及方向性均匀,质量稳定。
(4)缺点
1)制品形状限于圆柱形或其它回转体;
2)纤维不易沿制品长度方向精确排列;
3)对于大型制品,芯模成本高;
4)成品外表不是“模制”的,不尽如人意;
5)对于承受压力的制品,如选择树脂不合适或无内衬,就易发生渗漏。
(5)典型产品
管道、贮罐、气瓶(消防呼吸气瓶、压缩天然气瓶等)、固体火箭发动机壳体。
4、RIM(Reaction Injection Molding一反应注射成型)
图5 RIM示意图
(1)概要
将两种或两种以上的组分在混合区低压(0.5MPa)混合后,即在低压(0.5-1.5MPa)下注射到闭模中反应成型,此即为工艺过程。若组分一为多元醇,一为异氰酸酯,则反应生成聚氨酯 。为增加强度,可直接在一种组分内行加入磨碎玻纤原丝和(或)填料。弈可采用长纤维(如连续纤维毡、织物、复合毡、短切原丝等的预成型物等)增强,在注射前,将长纤维增强材料预先置模具内。用此法可得到高力学性能的制品。这种工艺称为SRIM(Structural Reaction Injection Molding-结构反应注射成型)。
(2)原材料
树脂:常用聚氨酯体系或聚氨酯/脲混合体系;亦可采用环氧、尼龙、聚酯等基本;
纤维:常用长0.2-0.4mm的磨碎玻璃纤维;
芯材:不用。
(3)优点
1)制造成本比热塑性塑料注射工艺低;
2)可制造大尺寸、形状复杂的产品;
3)固化快,适于快速生产。
(4)缺点
采用磨碎玻璃纤维增强原料费用高,荐用矿物复合填料取代之。
(5)主要产品
汽车仪表盘、保险杠、建筑门、窗、桌、沙发、电绝缘件。
5、拉挤成型 (Pultrusion)
(1)概要
主要采用玻璃纤维无捻粗纱(使用前预先放置在纱架上),它提供纵向(沿生产线方向)增强。
其它类型的增强材料有连续原丝毡、织物等。它们补充横向增强,表面毡则用于提高成品表面质量。树脂中可加入填料,改进型材性能(如阻燃),并可降低成本。
拉挤成型的程序是
1)使玻璃纤维增强材料浸渍树脂;
2)玻璃纤维预成型后进入加热模具内,进一步浸渍(挤胶)、基体树脂固化、复合材料定型;
3)将型材按要求长度切断。
现在已有变截面的、长度方向呈弧型的拉挤制品成型技术。
拉挤成型将增强材料浸渍树脂有两种方式:
胶槽浸渍法(图6):通常采用此法,即将增强材料通过树脂槽浸胶,然后进入模具。此法设备便宜作业性好,适于不饱和聚酯树脂,乙烯基酯树脂。
注入浸渍法(图7):玻纤增强材料进入模具后,被注入模具内的树脂所浸渍。此法适于凝胶时间短、粘度高、生产附产物的树脂基体,如酚醛、环氧、双马来酰亚胺树脂。
图6 胶槽浸渍法
图7 注入浸渍法
(2)原材料
树脂:常用不饱和聚酯树脂、环氧树脂、乙烯基酯树脂、酚醛树脂;
纤维:拉挤用玻璃纤维无捻粗纱、连续原丝毡、缝编毡、缝编复合毡、织物、玻纤表面毡、聚酯纤维表面毡等;
芯材:一般不用,现有以现场PU发泡材料为芯材,外为连续拉挤框型型材,作为保温墙板的。
(3)优点
1)典型拉挤速度0.5-2m/min,效率较高,适于大批量生产,制造长尺寸制品;
2)树脂含量可精确控制;
3)由于纤维呈纵向,且体积比可较高(40%-80%),因而型材轴向结构特性可非常好;
4)主要用无捻粗纱增强,原材料成本低,多种增强材料组合使用,可调节制品力学性能;
5)制品质量稳定,外观平滑。
(4)缺点
1)模具费用较高;
2)一般限于生产恒定横截面的制品。
(5)典型产品
建筑屋顶横梁、椽子、门窗框架型材、墙板、石油开采抽油杆、钢筋、锚杆、帐篷竿、梯子、桥梁、工具把、手机微波站罩壳、汽车板簧、传动轴、电缆管、光纤光缆芯、钓鱼竿、隔栅、汽车空调器罩、地铁第三轨保护罩。
6、真空袋法法成型(Vacuum bag process)
图8 真空袋法成示意图
(1)概要
此法是手糊法与喷射法的延伸。将手糊或喷射好的积层在树脂的A阶段与模具在一 起,在积层上覆以橡胶袋,周边密封,在后用真空泵抽真空,使积层受到不大于1个气压的压力,而被压实、固化、成型。
(2)原材料
树脂:主要采用环氧树脂、酚醛树脂。不饱和聚酯树脂与乙烯基酯树脂则因真空泵将树脂中的苯乙烯(交联剂)过度抽出,可能会造成问题,故一般不用;
纤维:同手糊法;
芯材:任意。
(3)优点
1)采用普通的湿法铺层技术,通常可获得高纤维含量的制品;
2)可制造大尺寸产品;
3)产品两面光;
4)较湿法铺层浸胶孔隙率低;
5)由于压力,树脂流经结构纤维,纤维得以较好地浸渍树脂;
6)有利于操作人员健康和安全;真空袋减少了固化时逸出的挥发性物质。
(4)缺点
1)额外的工艺过程增加了劳动力和袋材成本;
2)要求操作人员有较高的技术熟练水平;
3)树脂混合和含量控制基本上仍然取决于操作人员的技术;
4)生产效率不高。
(5)典型产品
艇、赛车、芯材粘结、飞机鼻锥雷达罩、机翼、方向舵。
7、树脂膜熔浸成型(RFI-Resin Film Infusion)
图9 树脂膜熔浸成型示意图
(1)概 要
将干织物与树脂片(树脂片系放在一层脱模纸上提供)交替铺放在模具内。铺层被真空袋包覆,藉真空泵抽真空,将干织物内空气抽出。然后加热,令树脂熔化并流浸已抽出空气的织物,然后经过一事实上时间即固化。
(2)原材料
树脂:一般仅用环氧树脂;
纤维:任意;
芯材:许多种芯材都可以使用,由于工艺过程中温度高,对PVC泡沫需要专门处理,以免泡沫损坏。
(3)优点
1)空隙率低,可精确获得高的纤维含量;
2)铺层清洁,有利于健康和安全(似预浸);
3)可较预浸法成本低,此为主要的优点;
4)由于树脂仅能过织物厚度方向传递,故树脂未浸到白斑区可较SCRIMP(西曼复合材料公司树脂参入成型法—Seeman Composite Resin Infusion Molding Process)少。
(4)缺点
1)目前仅用于宇航工业,还未推广;
2)虽然宇航工业用高压釜系统产非总是需要,但加热室和真空袋系统对于复合材料固化,总是不可少的;
3)模具要求能经受树脂膜片的工艺温度(低温固化即需60-100oC);
4)要求所用芯材能经受工艺温度和压力;
(5)典型产品
飞机雷达罩、舰艇声纳整流罩。
8、预浸料(高压釜)成型
图10 预浸料高压釜法示意图
(1)概要
预先在加热、加压或使用溶剂的条件下,将织物和(或)纤维预先用预催化树脂预浸渍。固化剂大多能在环境温度下,让预浸材料贮存几周或几个月,仍能保质使用。当要延长保持期,材料须在冷冻条件下贮存。树脂通常在环境温度下呈临界固态。故触摸预浸材料时有轻微的黏附感,象胶带似的。制作单向预浸渍材料的纤维直接由纱架下来,与树脂结合。预浸渍材料用手或机械铺于模具表面,通过真空袋抽真空,并通常加热到120-180oC。使树脂重新流动,并最终固化。盛开附加压力通常藉助高压釜(实际上是一座压力加热罐)提供,它能对铺层施加达5个大气压的压力。
(2)原材料
树脂:通常用环氧树脂,不饱和聚酯树脂、酚醛树脂及高温树脂,如聚酰亚胺、氰酸酯、双马来酰亚胺树脂等;
纤维:任意。虽然由于在工艺过程中,高温分对芯材有些影响,需要采用某些专门的泡沫芯材。
(3)优点
1)预浸材料制造人员可精确地调整树脂/固化剂水平和树脂在纤维中的含量;可以可靠地得到高纤维含量。
2)材料于操作人员十分安全,无碍健康,操作清洁;
3)单向带纤维成本最低,因为毋须将纤维预先转为织物的二次加工过程;
4)由于制造过程采用可渗透的高粘度树脂,树脂化学性能力学和热性能可以是最适宜的;
5)材料有效时间长(室温下可保质数月),这意味着可优化结构、复合材料易铺层;
6)可能实现自动化和节省劳动力。
(4)缺点
1)对于预浸织物,材料成本高;
2)通常要对高压釜固化复合材料制品,耗费大、作业慢、制品尺寸受限制;
3)模具需能承受作业温度;
4)芯材需要承受作业温度和压力。
(5)典型产品
飞机结构复合材料(如机翼和尾翼)、卫星与运载火箭结构件(太阳能电池基板、夹层结构板、卫星接口支架、火箭整流罩等)、赛车、运动器材(如网球拍、滑雪板等)。
9、低温 固化预浸料成型
图11 低温固化预浸料成型示意图
(2)原材料
树脂:通常用环氧树脂,不饱和聚酯树脂、酚醛树脂及高温树脂,如聚酰亚胺、氰酸酯、双马来酰亚胺树脂等;
纤维:任意。虽然由于在工艺过程中,高温分对芯材有些影响,需要采用某些专门的泡沫芯材。
(3)优点
1)预浸材料制造人员可精确地调整树脂/固化剂水平和树脂在纤维中的含量;可以可靠地得到高纤维含量。
2)材料于操作人员十分安全,无碍健康,操作清洁;
3)单向带纤维成本最低,因为毋须将纤维预先转为织物的二次加工过程;
4)由于制造过程采用可渗透的高粘度树脂,树脂化学性能力学和热性能可以是最适宜的;
5)材料有效时间长(室温下可保质数月),这意味着可优化结构、复合材料易铺层;
6)可能实现自动化和节省劳动力。
(4)缺点
1)对于预浸织物,材料成本高;
2)通常要对高压釜固化复合材料制品,耗费大、作业慢、制品尺寸受限制;
3)模具需能承受作业温度;
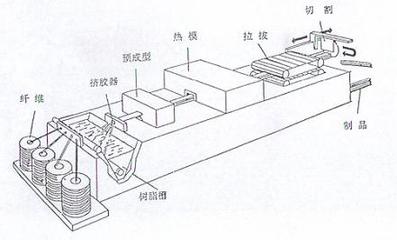
4)芯材需要承受作业温度和压力。
(5)典型产品
飞机结构复合材料(如机翼和尾翼)、卫星与运载火箭结构件(太阳能电池基板、夹层结构板、卫星接口支架、火箭整流罩等)、赛车、运动器材(如网球拍、滑雪板等)。
9、低温 固化预浸料成型
图11 低温固化预浸料成型示意图
(1)概要
低温固化预浸料完全按通常的预浸料方法制备,但树脂的化学性质使其得以在60-100oC温度下固化。在60oC时,材料可操作保持期可小到限于1个星期,但亦可延长到几个月。树脂系统的流动截面适于采用真空袋压力,避免采用高压釜。
(2)材料
树脂:一般仅采用环氧树脂;
纤维:任意,同通常的预浸料;
芯材:任意,虽然一般 的PVC泡沫需要特别注意。
(3)优点
1)具有传统预浸料法所具备的的一些条优点;
2)模具材料较便宜,如木材亦可用,因其固化温度较低故;
3)可容易地制造大型结构。因为仅需真空袋压力;固化温度低,可采用简单的热空气循环加热室(经常就地建造大于制品的加热室 )
;
4)可采用普通的PVC泡沫芯材,略作处理即可;
5)能耗低。
(4)缺点
1)材料成本仍高于预浸织物;
2)需加热室和真空袋系统,以固化制品;
3)模具需能经受高于环境温度的温度(常用60-100oC);
4)仍有能耗,因需高于环境温度固化。
(5)典型产品
高性能风力发电机叶片、赛艇、救生艇、火车用零部件。
10、SCRIMP,RIFT,VARTM
图12 SCRIMP,RIFT,VARTM示意图
(1)概要
SCRIMP(Seeman Composite Infusion Molding Process—西曼复合材料公司树脂渗透成型法),RIFT(Resin Infusion umder Flexibe Tooling—柔性模具树脂渗透法) ,VARTM(Vscuum Assisted Transfer Molding—真空辅助树脂传递成型)这三种工艺原理相似。
将织物作为干铺层材料入模内,如同RTM。然后覆以剥离保护层和缝编非结构织物。整个铺层用真空袋覆罩好。袋无渗漏后,让树脂流到积层。树脂很容易流经非结构织物而在整个铺层分布。SCRIMP法在真空袋与铺层之间可置加压模块,利于提高制作表观与结构密实度。
(2)材料
树脂:常用环氧树脂、不饱和聚酯和乙烯基酯树脂;
纤维:任意种类普通织物。这些工艺方法缝编材料很好用,因其间隙使得树脂快速流动;
芯材:除蜂窝外,各种芯材均可用。
(3)优点
1)同RTM,但制品仅一面光,不似RTM两面光;
2)由于模具一半是真空袋,主模具仅需较低强度,故模具成本甚低;
3)可制造大尺寸产品;
4)通常的湿法铺层工具可改进以用于这些成型法;
5)一次作业即可生产芯材结构。
(4)缺点
1)要完成好相对复杂的操作过程;
2)树脂粘度必须非常低,限制了制品的力学性能;
3)存在铺层未浸到树脂,而造成的废品浪费的可能性;
4) SCRIMP的一些工艺要素已被专利所限。
(5)典型产品
小艇半成品、列车和卡车车身面板。
三、环氧树脂复合材料的应用
环氧树脂是先进复合材料中应用最广泛的树脂体系,它可适用于多种成型工艺,可配制成不同配方,可调节粘度范围大;以便适应于不同的生产工艺。它的贮存寿命长,固化时不释出挥发物,固化收缩率低,固化后的制品具有极佳的尺寸稳定性、良好的耐热、耐湿性能和高的绝缘性,因此,目前环氧树脂“统治”着高性能复合材料的市场。
(一)环氧树脂复合材料在航空工业中应用
40年代初,电子工业的需要,寻找一种适宜的材料,做防护军用飞行器的雷达天线,特别是防护战斗机及轰炸机上的雷达天线。采用雷达罩是用来防护气候对精密电子仪器的影响。玻璃钢具有优良的透雷达波性能,足够的机械强度和简便的成型工艺,使它成为理想的雷达罩材料。这是历史上第一次采用玻璃钢制造雷达罩,同时又大大地促进了玻璃钢材料的研究。
60年代玻璃钢技术在直升机领域的应用有所突破,如西德M.B.B.公司研制玻璃钢旋翼桨叶,逐步取代金属铝蒙皮/铝蜂窝夹层结构的金属桨叶。但由于玻璃钢的模量低,不能制造高强度的飞机结构件。
70年代初,随着硼纤维、碳纤维、芳纶纤维等相继出现,这些高级增强纤维的比刚度、比强度、耐疲劳性能等优于金属材料,由它们来增强环氧树脂组成的复合材料,已在飞机的主结构件(主受力件)上得到应用。
近10多年来,考虑到这些高级增强纤维的价格都比较高,为了更合理的用材,大力开发混杂复合材料(Hybrid Composites)的研究。
以复合材料在飞机发动机中的应用为代表。美国两家喷气发动机制造厂:通用电器—飞机发动机事业集团公司(GE—AEBG)和普惠公司,以及其它一些二次承包公司,都在用高性能复合材料取代金属制造飞机发动机零部件。如发动机舱系统的许多部紧推力反向器、风扇罩、风扇出风道导流片等都用复合材料制造。如发动机进口气罩的外壳是由美国聚合物公司的碳纤维环氧树脂预混料(E707A)叠铺而成,它具有耐177℃高温的热氧化稳定性科壳表面光滑如镜面,有利于形成层流。又如FW 4 0O0型发动机有8 0个149℃的高温空气喷口导流片也是用碳纤维环氧预浸料制造的。
在316℃这一极限温度以下的环境中,复合材料不仅性能优于金属,而且经济效益高。据波音公司估算,喷气客机重量每减轻一磅,是飞机在整个使用期限内可节省 100 0美元。据法布莱特公司估算,美国第年约有100万磅复合材料用于制造喷气飞机发动机零件,销售额高达5000万美元。
目前环氧树脂的连续使用温度最高约在280℃以下,近来DOW化学公司的一种多功能团环氧树脂Tactlx742,用二氨基二苯砜固化剂;制成的制品玻璃化温度Tg>310℃,可用于制造喷气发动机零件。用二氨基二苯砜固化剂;制成的制品玻璃化温度Tg>310℃,可用于制造喷气发动机零件。
(二)环氧树脂复合材料在航天工业中的应用
宇航技术对结构材料高比模量、高比强度的要求,特别严格,使先进复合材料成为宇航技术必需的材料。作为结构材料的基作树脂基本上都采用环氧树脂。其主要的应用范围如下:
1、固体火箭发动机壳体
在50年代末,采用纤维缠绕成型的玻璃钢壳体取代钢壳,使结构减轻50%一60%。后来,“三叉戟1”、 M X的三级发动机壳体全部采用芳纶/环氧树脂体系,重量又比玻璃钢的同尺寸壳体减轻50%。
阿里亚娜运载火箭许多结构件均用碳纤维/环氧树脂制造。
2.战略导弹上的应用
美国早已采用纤维增强环氧复合材料作弹头结构壳体、仪器舱、级间段等50多个分系统部件。据 洛克希德导弹与宇航公司称用碳纤维/环氧树脂制造的机构取代铝结构,可使结构减轻40%。
3、卫星和宇航器上的结构应用
卫星结构的轻型化对卫星功能及运载火箭的要求至关重要,所以对卫星结构的重量要求很严。国际通讯卫星VA中心推力筒用碳纤维复合材料取代铝后减重23kg(约占3O%),可使有效载荷舱增加 450条电话线路,仅此一项盈利就接近卫星的发射费用。美、欧卫星结构重量不到总重的10%,其原因就是广泛使用了先进复合材料。。
4.航天飞机上的应用
美国航天飞机上使用的结构复合材料总重约2吨,采用先进复合材料后减重410kg,而且明显减少了飞行过程中因复杂的温度环境引起的变形。航天飞机进入轨道后,用机械手投放和回收卫星,机械手上臂、前臂是用超高模量石墨纤维 GY— 7 0增强环氧制成的。
总之,复合材料已成为宇航工业中不可缺少的关键材料。
(三)环氧复合材料在民用工业中的应用
凡是对机械强度要求高的增强塑料制品基本上采用环氧树脂作为基体。
1、玻璃钢的压力容 器和管道
我国北京、西安、重庆、自贡已生产汽车用压缩天然气(CNG)瓶,北京已成为现在世界上使用CNG公交车最多的城市。
国内已经有4家企业生产纤维缠绕环氧玻璃钢高压管。对直径100mm以下的管道工作压力达25Mpa。值得注意的是这种管无须内衬层!
60年代国内钢瓶十分紧张,采用纤维缠绕成型制造玻璃钢气瓶相当活跃,曾制定过部颁标准FC194-74,90R年修改后制定ZBQ23004一90。 玻璃纤维增强塑料压力容器,以634环氧树脂和616酚醛树脂体系为基体,使用环氧树脂一二甲基咪唑体系,其性能不亚于环氧一酚醛树脂体系,用此配方制成水研用的压力容器。迄今北京251环氧树脂一二甲基咪唑体系,其性能不亚于环氧一酚醛树脂体系,用此配方制成水研用的压力容器。迄今北京251厂已生产各种气瓶10万只,北京天海公司2004年生产CNG气瓶2.6万只,月产曾达3000只。
2、玻璃钢电机护环、套环等
护环套装于发电机转子两端,保护转子线圈的端部,防止在高速旋转时,受离心力作用。它是发电机受力最大的部件之一,对强度和模量要求比较高,采用轻质高强的复合材料可以取代无镍反磁合金钢。早在上世纪60年代末国内先后生产1.25W千瓦和2.5万千瓦两种发电机护环。后者由北京重型电机厂、杭州玻璃钢化工设备厂和上海材料研究所等单位合作,选用高强度(S)玻璃纤维和高模量(M)玻璃纤维进行缠绕,用62O7(脂环族)环氧树脂一酸酐体系树脂配方和 AFG— 9 0环氧树脂(缩水甘油胺型)—— HK—0 21酸酐体系作为基体,使用多年情况良好。
玻璃钢套环 3 0 00千瓦以下的在杭州玻璃钢化工设备厂生产,已在北京重型电机厂安装出厂30年,属于定型产品。
此外,发电机定子线圈端部支撑环,装在定子线圈的鼻端,承受最大载荷是发电机发生短路的瞬间,亦采用玻璃钢制造,称为玻璃钢绑环。这种绑环安装在10万千瓦的气轮发电机上,已使用30余年。在国内最大的60万千瓦发电机用的玻璃钢锥壳(其作用类似于支撑环)已用了20多年。
玻璃钢绝缘子,有待于进一步开发研究。绝缘子的作用是把带电线路或带电零部件之间隔开,既要求绝缘又要求高强度,电绝缘和耐腐(室外用),采用玻璃钢很适用。国外在露天的22万伏输电杆上的绝缘于已采用环氧树脂玻璃钢成批生产。
3、防腐蚀制品
通常不饱和聚酯树脂玻璃钢的力学性能在45℃以上强度就会明显下降,同时不饱和聚酯树脂耐碱性较差。如果在防腐蚀制品中要求强度高,耐温性好等则建议选用环氧玻璃钢。如上海市上钢二厂,在生产硫酸铁过程中,反应槽需要连续在120℃使用,选用环氧玻璃钢取得了很满意的效果。
4、玻璃钢模具
(1)玻璃钢铸造模具
用玻璃钢制成的铸造模具,比木模、铝模的效果好的多,使用寿命长,通常在万次以上,价格也比较便宜。
(2)玻璃钢制品模具
采用喷射成型、树脂传递模塑( RTM)成型所需的制品模具,通常都用不饱和聚酯玻璃钢模具。笔者建议采用环氧树脂玻璃钢模具更好,具有模具强度高、使用寿命长、尺寸稳定性好等优点。
5、风力发电机叶片 我国目前已做到长23m,国外已经超过50m。6、碳纤维补强建筑结构
6、运动器材
高尔夫球杆、网球拍、羽毛球拍、壁球拍、滑雪板、渔具、自行车架等。
四、我国环氧树脂市场分析
据统计,2003年中国大陆环氧树脂产量25万吨,比上年增长25%;进口19.88万吨,比上年增长23%;出口3.558万吨,比上年增长81%,表现消费量41.322万吨,比上年增长21%。
2004市场比例为:
涂料
45%
电子电器
36%
复合材料
5%
粘结剂
-7%
其它(交联剂等)
-7%
2003年我国大陆生产高压玻璃钢环氧管3000吨,约用环氧树脂1300吨。建筑结构采用CF(碳纤维)补强用环氧树脂5 00吨。
绝缘棒管生产2000吨,用环氧树脂1000吨。
2003年生产环氧玻璃钢2万吨,采用环氧树脂9000余吨。
2003年生产玻璃纤维基覆铜板14万吨,采用环氧树脂6.15万吨。2004年可增长3O%以上。所用环氧树脂将达8万吨。
2003年用于生产乙烯基酯树脂(VER)采用环氧树脂2900吨。
国产树脂的质量稳定性有待于进一步提高,因而国内一些复合材料厂家在生产要求性能较高的产品(如绝缘棒、绝缘管)时,常采用陶氏(DOW),壳牌(Shell)、巴克立特(Bakelite)等国外公司的产品。
继美国陶氏化学在江苏省张家港市建设一年产能4.1万吨环氧树脂生产厂后并拟建一年产能 4万吨的厂;韩国国都化学正在昆山建一年产 2万吨的环氧树脂厂,并拟再建一年产2万吨环氧树脂的生产线。
台塑子公司宏仁集团引进日本东都化成技术在广州兴建了年产能2.3万吨的环氧树脂厂。日本钢铁化学公司子公司Tohto Kasei公司转让技术给黑龙江省齐华化学公司建一年产能2万吨的环氧树脂厂。
值得补充的是,环氧树脂还可用于文物保护。在长江三峡的国家级重点文物重庆市云阳县张飞庙(张桓侯庙)整体搬迁过程中,大量残损砖石是以环氧树脂粘结修补或灌注成型定型 ,使这座始建于三国蜀汉末年(距今 1780年)的古建筑得以回复留存。