(一)车刀的组成部分车刀分为刀头和刀体两大部分。车刀的刀头是车刀的切削部分,它由以下几个要素组成:
1。前刀面:切屑流出时,刀头与切屑相接触的表面。又称前面。
2。主后刀面:刀头上与切削表面相对的表面。又称主后刀面。
3。副后刀面:刀头上与工件已加工表面相对的表面。又称副后刀面。
4主切削刃:前刀面与主后刃面的交线。它担负主要的切削工作。
5副切削刃:前面与副后刃面的交线。它也起切削作用。
6。刀尖:主切削刃与副切削刃的交点。
任何车刀都是由上述组成,而其数目不完全相同。如切断刀就有两个副切削刃的两个刀尖。另外,切削刃可以、
是直线的,也可以是曲线的。如样板车刀的切削刃就是曲线的。
(二)辅助基准平面
为了确定和测量车刀的几何角度,需要选择几个辅助平面作为基准面。
1切削平面:切削刃上任一点的切削平面,是通过这点与工件的切削表面相切的平面。
2基面:通过切削刃上一点并垂直于切削平面的平面。切削刃上的同一点的基面与切削平面一定是垂直的。
3主截面:主切削刃上任一点的主截面,是通过这一点而垂直于主切削刃在基面上的投影的截面。
当主切削刃与水平面平行时,切屑 流出的方向正接近于这一平面所处的位置,因此车刀上主要切削角度(如前角,后角)都在主截面上进行测量。
(三)车刀的切削角度过 车刀的切削角度共有10项,用于表示切削部分的几何形状,并可在上述三个辅助基准面内度量。
1。在主截面内测量的角度
(1)前角:前面与基面在主截面的夹角。前角影响切屑形成与流出的难易程度以及切削力的大小和刀具强度。
(2)后角:主后面与切削平面在主截面的夹角。后角影响后面与工件加工表面之间的磨擦和刀具强度。
(3)楔角:前面与主后面在主截面内的夹角。楔角的大小影响刀头的强度和刃口和锋利程度。
(4)切削角:切削平面与前面在主截面内的夹角。它是前角的余角。
2。在基面内测量的角度
1主偏角:主切削刃与进给方向在基面上投影的夹角。又称导角。它影响主刀刃参加工作的长度,并影响刀削力的大小。
2副偏角副切削刃与进给方向在基面上投影的夹角。又称离角。它影响已加工表面的粗糙度及副刀刃参加工作的长度。
3刀尖角:主、副切削刃在基面上投影的夹角。切尖角的大小影响刀尖的强度及传热性能。
4刀倾角:又称主切削刃斜角。是主切削刃与基面间的夹角。主要影响排屑 情况和刀尖承受冲击的能力。当刀尖主主切削刃最低点时,为正值。当刀尖是主切削刃最高点时,为负值。当刀刃与基面平行时,为零度。
3在副后刀面内测量的角度
1副后角:副后角与副切削平面在副截面内的夹角。其作用与后角相似。
2副前角:前面与基面在副截面内的夹角。
二。车刀几何角度的选择、
合理选择车刀的几何参数是保证加工质量(精度、粗糙度)的前提下,提高刀具的切削用量,减少车刀磨损,提高刀具耐用度。
(一)前角的选择、
1工件材料对前角的影响:车削塑性材时,切屑呈带状。切削力集中在离主切削刃较远的前面上,刀尖不易受损、。为减少变形,应采取较大的前角。加工
钢件的硬质合金刀具前角一般取12-30度。
车削脆性材料时,切屑呈碎粒状,加上工件表面硬度高,通常含有杂质及砂眼、缩孔等缺陷,使刀尖附近集中了很大的冲击力,
为保护刀尖,在一般情况下前角应取小些。加工铸铁类工件,硬质合金刀具前角一般取5-15度。
工件材料较软,可选取较大的前角;工件材料较硬,则应选取较小的前角。如使用硬质合金黄色刀加工一般碳
钢类工件,前角取12-30度,加工铝类工件,前角取25-35度,加工橡胶类工件,前角取40-50度。但在加工较硬材料工件时,因切削阻力大,应取较小的前角,
以保证车刀强固。如加工铬锰钢工件时,车刀前角通常磨成度。车削淬硬钢件时,也常将车刀前面磨成负值,以增加车刀耐用度。
2。刀具材料对前角的影响:高速钢、合金工具钢等刀具韧性较好,抗弯强度较高,可采用较大的前角。硬质合金及陶瓷等刀具材料性脆,怕冲击,抗
弯强度较差,故前角应取得小。
3。加工特点对前角的影响:粗车时,切削深度大、进给快、切削时冲击力大、工件表面硬度较高,所以在不影响车刀锋利前提下选取较小的前角。
精车时,因工件表面有精度要求,加大前角可以减小切削力,减小变形,改进工件表面粗糙度,应选取较大
前角。又由于切削深度浅,进给量小,相应地也具备了允许加大前角进行进行切削的有利条件。
(二)前面形状的选择 前面的形状是指主截面的形状。它直接与切屑接触,其形状和粗糙度对切屑的流出及切屑在前面上的摩擦有直接影响。对于高速钢车刀只有正前角的三种
:平面型、平面带倒棱型和带断屑槽型。对硬质合金车刀,除以上三种外,还有负前角双面型和负前角单面型两种。
精加工和成型刀具应采用正前角平面型。粗加工刀具一般采用平面带倒棱型。
(三)断屑槽的选择 为使切屑有规律地流出和折断,就要针对不同的工件材料、车刀切削角度、切削用量和切削要求,选取用不同的形状和尺寸 的断屑槽 。
1。断屑槽与工件材的关系: 车削较硬的塑性金黄色属材料时,由于切屑本身的强度较大,可把断屑槽磨成阶台型式,使切屑与阶台面碰后折断。车削硬度较低度的塑性材料时,由于
、把断屑槽磨成圆弧曲面型式,使切屑沿圆弧面变形,增加其内应力而自然折断。
2。断屑槽和切削用量的关系:粗车时,切削深度和进给量大,切屑的断面积大,断屑槽要磨得宽而浅。在精车时,切削深度和进给量小,切削速度较高,切屑的变形减小而切屑 的产生
速度 加快,为使切屑有规律地排出,宜将切屑槽取窄而深些。
3。断屑槽在刀具前面上所处的位置也影响断屑的效果。当断屑槽与主切削刃平行时,切屑通常在主切削刃前端的主后面上折断,或在断屑槽里盘旋成发条形排出。这种位置断屑槽刃磨较方便。
常以偏负值的刃倾角相配合,可取得良好断屑效果。
断屑槽与主切削刃不平行时,若在偏向主切削刃后端的主后面上折断,或成弹簧形排出,当达到一定长度时甩断,断屑效果较好。但断屑槽位置刃磨较难。
断屑槽位置与主切削刃不平行时,若在偏向主切削刃前端的主后面上折断,易与切削表面相擦碰,它的刃磨较易,适于粗车,别是强力切削。精车时
不宜采用。
(四)后角的选择 后角的作用主要是减少车刀的主后面与工件切削表面的之间的摩擦,影响刀具的磨损。后角与刀具强固有直接关系。后角大,磨擦可减小,车削较快,车刀磨损也慢。但后角过大,
车刀楔角减小,强度减弱。而且刀刃散热变差,磨损反而加剧。
后角的选取择原则、
1。粗加工取较小后角,一般取3-6度。精加工取较大的后角,一般取4-8度。
2。工件或车刀刚性较差时,应取较小后角,例如车细长轴、较长的梯形内螺纹时,采用减小后角的方法能有效的
减少振动。、
3。工件材质较硬,后角宜小。工件材质较软时后角值可取较大些。
4。高速切削时应选较小后角。副后角一般与后角数值相同。
(五)主偏角和副偏角的选择P65
主偏角大小直接影响切削力和切削刀具耐用度。在相同的走刀量和切削深度下进行切削时,减小主偏角,能使主切削刃参加切削的长度增大,切屑变薄
此时刀刃散热面积加大,改善散热情况。且刀尖角增大,提高了刀尖强度,对提高刀具耐用度有利。但主偏角大小又直接影响到切削力的分配。主偏听偏角的减小会使主切削力、和径向力增大而轴向力减小、
易使工件产生振动而造成弯曲变形。这对工件表面形状和精度影响大。所以选择主偏角,首先要孝虑工件外形要要求及工艺系统的刚性,其次才是刀具的耐用度。一般车刀的主偏角取45度、60度、75度、90度几种。
选择主偏角的几个原则:
1。工件、车刀、夹具和机床的刚性较差时,主偏角选大值。
2。工件材料越硬,主偏角相应取小些。
3。主偏角还有与工件形状有关,车削带直角台阶轴时,取90度;车削不通孔的内孔车刀大于90度,;车削细长轴
工件,取75-90度;车退刀槽或需从工件中间切入时,60-75度;有45度倒角的工件也可以取45度,其它情况,为提高也具的耐用度取30-60度。
副偏角的作用是减小车刀与已加工表面间的摩擦。副偏角减小,可显著减少车削后的残留表积,改进工件表面的粗糙度。但减小副偏角会增加刀削面积,引振动。因此,只有当工件、车刀和机床具有足够的刚性时,
才能取较小的副偏角。副偏角一般取2-8度。在采用宽刃车刀车削时,由于刀刃大于进给量,则副偏角为0度。
(六)刃倾角的选择 刃倾角是刀具上的一个重要角度,它与刀具的锋利和强固程度有着密切的关系。其值对车削过程的影响是:
1。影响实际前角。当值增加,实际前角就增大,使切屑易流出,变形减小,切削力下降,。
2。影响刀尖受冲击情况。当为正值时,可使刀尖不先受冲击。而为负值时,刀尖将先受到冲击。
3。影响排屑 方向。当为正值时,刀屑将流向已加工表面;当为负值时,切屑将会流向待加工表面;当为0值时,切屑在原地打卷或呈直条状射出,
选择刃倾角的原则:
1。对表面圆整、被切层均匀的工件粗车时,一般取2- -3度。精车时,为使切屑不致流向已婚加工表面而将其擦伤,应取负角,-3 - -8度。
2。强力切削,为加强刀刃可取正值0-10度;断续切削或有冲击,可增大正值,取10-35度。
3。取正值的刃倾角时,如果工件、车刀、夹具和机床的刚性较好,则可适当增大些。
(七)过渡刃的选择 过渡刃的作用主要提高刀尖强度和改善散热条件。车刀的刀尖部位是切削力和切削热最集中的区域,极易磨损。当刀尖处磨有过渡刃时,就能显著的改善刀尖处的切削性能,提高车刀耐用度。
过渡刃的形状有圆弧形和直线形两种,P68
1。圆弧过渡刃(刀尖圆弧半径r)r增大,可提高加工表面的光滑程度和刀具耐用度;但同时也会增加切削力,易产生振动。对高速切削钢车刀,0.5-5毫米;硬质合金车刀,0.5-2毫米。
、精车时r取小值,粗车时取大值.
一般普通车床,车刀本身不大,取值不超过2毫米.
2.直线过渡刃:当圆弧过度刃不易磨得准确或对称时,可采用直线过渡刃.当过渡刃的长度一般取0.5-2毫米,偏角通常取主偏角的一半左右.
(八)修光刃的选择.当进给量很大时, 为发减小车削后的残余面积,改进工件表面粗糙度,常在副偏角磨好后,再磨一个与进给方向相平行的修光刃.刀具增加修光刃,可适当增大进给量.以提高生产效率和刀具的耐用度.但修光刃过大,会使切削力增加而引起振动.一般取
修光刃长度(1.1-1.5)s (s 为走刀量,也叫进给量.).
(九)负倒棱的选择刀具的主切削刃担负着绝大部分的切削工作.为提高主切削刃的强度,改善它的受力和散热情况,常在车刀的主切削刃上磨出负倒棱(有时也在过渡刃上也可磨出负倒棱以提高它的强度).对于
采用较大前角的硬质合金刀,磨出负倒棱有利于克服刀片抗弯性差、性脆、不耐冲击等缺陷,可减少磨损。预防"崩刃".
负倒棱的倾角度一般取-5度左右.在强力切削、断续车削以及车削一些韧性较大的材料(如调质钢、不锈钢),负倒棱的倾斜角的负值可取大些。这既可进一步增强刀刃的强度,改善刀刃受力及散热情况,又可使负倒棱上形成较稳定的积屑瘤,增大车刀实际前角,减少车刀磨损,提高车刀耐用度。
负倒棱的宽度一般不应大于走刀量s值。
对于强度、硬度特别低的材料,则不宜采用负倒棱。
三、刀具切削角度的综合选择
一把车刀往往同时具有几个切削角度,这些切削角度彼此是相互依赖以相互制约的。选择车刀的切削角度时,必须根据工件材料、加工特点、切削用量。。。。。。等各方向因素选择合理的切削角度,设计出理想的车刀。
下面举几种常用的车刀说明切削角度的综合选择。
(一)粗加工用75度综合车刀 零件粗加工时,由于表面粗糙,加工余量大,几何形状不规则,会断续切削,冲击很大。因此,切削力和切实可行削热大,刀尖
易磨损。为了适应粗加工特点,在选择 刀具和切削角度时,要加大前角加负倒棱,取正值刃倾角,适当减小后角以减小切削变形,同时节增强刀尖强度。加工轴类零件时,要加大主偏角以减少径向力。刀具材料用YG8或YT15。
1。刀具的特点
(1)刀具材料为YT15硬质合金,刀杆为45号钢。
(2)前角15-18度,以减少机床负荷。后角4度,使刀头强度较高。
(3)主偏角75度。加工轴类工件可减少径向力,避免振动。采用45度直线过渡刃。副偏角6-8度,刀尖角大,散热快,可提高刀具寿命。
(4)采用正刃倾角4-6度,增加了刀刃强度。
(5)采用直线过渡刃,主刀刃与修光刃磨成R0.5毫米的圆弧.修光刃宽度f=s+0.3(s为进给量),可保证表面粗糙度在允许值范围.
(6)断屑槽浅,刀片磨耗小,断屑槽采用65度 斜角,使切屑有规律地向待加工表面方向排出。
(7)刀刃倒棱随进给量增加而适当增加,但不大于0.5S.这样加强了刀刃强度,并改善了切削状况.
2.使用条件:切削速度50米/分,进给量1-1.5毫米/转,切削深度5-10毫米,机床功率25千瓦.
3.应用范围:适用于强力切削,切削大型中碳钢铸件及锻件.
4.注意事项
(1)装刀要牢靠.车刀不宜伸出过长,一般伸出的长度约为刀杆厚度的1.5倍.但也不可过短,以免影响排屑.装刀垫要平整.
(2)对刀时刀尖要高于工件中心,约为工件直径的1/100,但不超过4毫米.
(3)机床车刀要大.切削前车床各部分的机构和间隙要调整好,不应松动.若发现主轴转速由于机床超负荷使用而减慢时,应退刀.退刀时,先停止进给以保护刀尖.若发现闷车时,应先关闭电机,防止车头倒转.卸车刀时,先松小刀架上靠后的压
紧螺钉,将刀具卸下.
(二)加工细长轴的车刀 凡加工零件长度与直径之比大于或等于20时称为细长轴.由于零件细长,刚性差,要求切削时径向力越小越好. 为了减少切削时的切削力,应在不影响刀具强度的情况下,尽量加大刀具的主偏角和前角,
主偏角取90度,前角取10-30度.
1.刀具的特点
(1)刀片材料为YT15,刀杆材料为45号钢.
(2)主偏角90度,减小了径向抗力.
(3)前面磨成4-5毫米宽的圆弧R3卷屑槽 ,使排屑卷屑好.因切削阻力和摩擦阻力小,散热性能好,使切屑成银白色.
(4)主刀刃磨出0.1-0.15毫米倒棱,提高了刀刃强度.刃倾角-3度,会产生线状蓝色副切屑,位于主切实可行屑中间,消除了刀瘤对已加工表面的粘附,排屑方便,切屑不损伤已加工表面.
(5)刀具结构简单,手工刃磨容易掌握.
2.使用条件:粗车时切削速度50-60米/分,进给量0.3-0.4毫米/转,切削深度1.5-2毫米;精车时切削速度100-200米/分,进给量0.08-0.12毫米/转,切削深度0.5-1毫米.采用乳化液作冷却润滑液.
3.适用范围:适用于加工光杠丝杠等细长轴外圆.
(三)加工铸铁材料的车 刀 铸铁材料的硬度低,抗拉强度小,塑性变形小,因此切削变形和切削抗力较小.但铸铁材料的表面层硬度高,局部有砂眼、气孔和缩孔等缺陷,切屑 呈崩碎的小块,使刀刃要承受一定的冲击力,刀尖区域散热性差。
加工铸铁的车刀应选取一定的前角,10-15度。中等的主偏角45-75度。并适当增大后角6-12度。刀片材料采用钨钴类硬质合金。
1。刀具的特点:
(1)刀具材料为YG6,刀杆材料为45号钢。
(2)前角15度,并具有(0.2-0.4)S 到(1-1.5)S的钭向负倒棱,增强车刀切削部分的强度.后角8度,在不影响强度的情况下减少与后刃面的摩擦.
(3)采用刃倾角0-3度,以增强刀刃的强度.
(4)主偏角75度,副偏角5度,刀尖角为100度,增大了散热面积,以提高刀具寿命.
(5)刀尖磨出R1.5毫米圆弧,用以保证加工工件的表面粗糙度值在允许范围内.
2.使用条件:切削速度30-50米/分,进给量0.75-1.5毫米/转,切削深度5-10毫米.加工时不允许用冷却润滑液.
加工铸铁时, 为了保护刀尖,不使刀尖与铸铁表面的硬皮接触,应选取用较大的切削深度的进给量.而切削速度应比加工钢件时选择低一些,以减少车刀的磨损和提高车刀的耐用度.
(四)加工铝合金的车刀 加工铝合金时,有利条件是材料的强度和硬度低,塑性变形小,切实可行削抗力小,导热性能好,好削温度不高.但铝合金熔点低,
在切削的过程中容易产生刀瘤,影响零件表面粗糙度.铝合金中含有硅,硅的化合物,所形成的硬质点,会加剧刀具的磨损.加工铝合金的车刀应选用较大的前角20-30度,较大的主偏角,60-90度.
并适当加大后角12度.刀头选用钨钴类硬质合金.
1.刀具的特点
(1)刀片材料为YG8,刀杆材料为45号钢.
(2)采用大前角30度,前面磨成圆弧形,无倒棱,刃倾角0度.前面粗糙度要求0.20,以减少切屑 的粘附.这种车刀切削阻力小,排屑流畅,切屑呈刨花式排出.
(3)主偏角60度,副偏角30度,刀尖圆弧R0.5-1,使刀头有一定的强度.
(4)后角12度,粗糙度0.20,以减少与零件之间的摩擦.
加工铝合金时,粗车使用乳化液.精车使用煤油为冷却润滑液.
2.使用条件: 切削速度150-200米/分,进给量0.15-0.5毫米/转,切削深度0.5-5毫米.
加工铝合金时切削速度 应比钢类材料高2-3倍.
(五)加工不锈钢的车刀不锈钢材料以Cr18Ni9Ti为例,基材粘且硬,车削时硬度高,塑性大,刀削变形大,切削力大,冷硬性强,导热性差,在高温下易于车刀的刀尖表面粘结在一起.而且切削时切屑温度度,刀尖易磨损.加工不锈 钢
的前角应选得大些15-20度.,并加负倒棱.后角不宜过大8-10度.主偏角75-90度.刃倾角3-5度.刀片材料可选用YG8、
YW1和YW2等。
1。刀具的特点:
(1)刀片材料为YW1、YW2,刀杆材料为45号钢。
(2)前角20度,并具有(0.5-0.8)S负倒棱,刃倾角3-5度,以增加刀具强度又利于切屑的变形。
(3)主偏角为75度,并以R50毫米大圆弧均匀转接,刀头强度较好,具有抗冲击性能。副偏角5度。、
(4)后角10度,在不影响刀具强度的情况下减少刀具后面与零件间的摩擦。
2.使用条件:粗车时切削速度60-80米/分,切削深度3-7毫米,进、给量0.3-0.6毫米/转;精车时切削速度100-150米/分,切削深度0.5-1毫米,进给量0.15-.-0.3毫米/转.
粗车时使用充分的冷却润滑液.
加工不锈钢时,切削用量应比加工碳素钢小些,特别是切削速度更不宜过高,以防止刀刃加速磨损和"粘刀".
(六)加工淬火钢的车刀淬火钢材料硬度高,脆性大,切削抗力和切削热大,刀具的磨损和崩刃现象严重。为了适用上述加工条件,车刀要采用负前角-5---20度,正刃倾角5-10度,并采用较小的主偏角20-60度和较大的刀尖圆弧。
1。刀具特点
(1)刀片材料为YG8、YW1、YW2,刀杆材料为45号钢。
(2)采用较大的负前角-20度,刃倾角10度,刀尖强度比一般刀具要大。
(3)主偏角40度,副偏角20度,刀尖圆弧角120度,刀尖圆弧R1.5毫米,刀尖强度好,散热快,提高了刀具耐用度,并且刃磨简单.
2.使用条件:工切削速度 25-30米/分,进给量0.1-0.3毫米/转,切削深度0.5-4毫米.
适用加工硬度为HRC50-54的碎火钢,或20号钢渗碳淬火以及合金钢、高锰钢等材料。
二车削用量和冷却润滑液的选择
一、车削用量的合理选择
切削用量是指切削深度(吃刀深度)、走刀量和切削速度。切削用量不仅对切削力、切削热
积屑瘤、工件精度和粗糙度有很大影响,还与提高生产率有着密切的关系。
(一)切削用量
1。吃刀深度:工件的侍加工表面和已加工表面之间的垂直距离,即车刀吃进工件的深度(单位:毫米)。
t=(D-d)/2毫米
式中D - 待加工面直径(毫米) d- 已加工表面直径(毫米).
2.走刀量:工件转一圈,车刀沿走刀方向移动的距离(单位:毫米/转).它有纵向走刀量和横向走刀量之分.
3.切削速度 :车刀在一分钟时间车削工件表面的展开直线长度(单位:米/分).它的计算公式:
v=*dn/1000米/分
式中:D -工件直径(毫米);n---主轴每分钟转数(转/分)
(二)切削用量的合理选择 一般来说加大切削用量对提高生产效率有利,但过分增加切实可行削用量会加剧刀具磨损,影响工件质量甚至撞坏刀具,产生"闷车"等严重后果.所以要在一定范围内合理地选择切削用量.
1.粗车或精车时选择切削用量的一般原则:
(1)粗车时,一般加工余量大,如要求车得快些,首先考虑切削深度吃得深些,以减少吃刀次数,其次是走刀量大些,然后再选择适当的切削用量.
(2)精车时,加工余量小,要提高生产效率只有适当增加切削速度.而此时被切层较薄,切削力小,也具备了适当提高切削速度的条件.
2.不同切削条件下选择切削用量的几点原则:
(1)粗车铸铁件比粗车钢类工件吃刀深度大,而走刀量小.精车铸铁件比精车钢件走刀量大而切削速度 低.
(2)断续车削的切削用量应比连续选得小.
(3)铸、锻工件粗车第一刀(称为荒刀)时,要加大吃刀深度,可适当减小走刀量和切削速度。
(4)车削内孔比车削外圆切削用量小。
(5)精车管料工件比精车轴类工件切削速度选得小些。
(6)用高速钢车刀切削比硬质合金车刀刀削选择切削速度要小。
(7)当工件、车刀、夹具和机床刚性强时,可选择切削用量较大些。
3。车削常用P
89
二、冷却润滑液的作用和选择
在车削的过程中,金属切削层发生变形。切屑与刀具间、刀具与加工表面间又有激烈的摩擦。变形的摩擦产生了很大切削力和大量的切削热。若在车削过程中有效地使用冷却润滑液,就能改善表面粗糙度,减少切削力15%-30%,降低度切削温度100-150度,
并能提高刀耐用度,从而提高了生产效率及产品质量。
一般情况下切削热的分布情况是:切屑占68%,车刀占25%左右,所以使用冷却润滑液主要浇在切屑上。
冷却润滑作液应具有以下性能:冷却性、润滑性,其次还应有洗涤性、防蚀性、经济性,对人体健康无害以及使用方便和稳定性。
冷却 润滑液可分两大类:水溶液--主要起冷却作用。油类--主要起润滑作用。
冷却润滑液种类很多,
冷却润滑液不能用得太少,太少了作用不大。更不能断续使用,否则会使硬质合金刀片碎裂。当然也不可滥用导致浪费。90
橡胶材料的车削、、
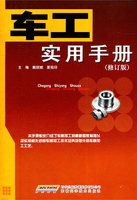
刀具及切削用量、
1。刀具材料:刀具材料常采用T8A、T10A、T12A、W9Cr4V2和W18Cr4V等工具钢和高速钢制成.
2.刀具种类及其应用
(1)套料车刀:套料车刀适用于在板材上加工密封垫圈、衬垫和皮碗等橡胶零件。在车削时,可先车内孔而后车削外圆。车工刀切削部分的圆弧半径值的大小应取零件圆弧公差的中间值勤。
(2玻璃钢材料的车削
1。刀具材料:一般采用YG6和YG8两种。
2。刀具角度:前角25-30度;后角10-12度;其余几何角度与通用车刀相同。
3。切削用量:进给量0.1-0.6毫米/转;切削速度 和切削深度可参照一般钢材选择.
三.有机玻璃材料的车削
刀具及切削用量
1.刀具材料:常用的刀具材料有YG6、YG8、和W18Cr4V等.
2.刀具角度:前角30-40度;后角10-12度;其余角度与通用车刀相同.
3.切削用量:进给量0.08-0.3毫米/转;切削速度,粗车时的切削速度比一般钢件略高.精车和车薄壁件时,其切削速度应比车削钢件略低,以便减少切削热产生的变形.切削深度可参照一般钢件选择.
四. 夹布胶木材料的车削.
刀具材料 常用的刀具材料有YG6、YG8和W18Cr4V等。
(二)刀具角度前角35-40度;后角12-14度;其余角度和切削深度可参照通用车刀选择。
(三)切削用量进给量0.1-0.4毫米/转;其切削速度 和切削深度与一般钢件相同.
高温合金的车削
刀具的选择 常用的刀具为硬质合金和高速钢两类.如YG8、YG6用于粗车;YG8、YW1、YW2等用于精车;YG8、W2Mo9Cr4VCo8、W18Cr4V等用于高温合金的精车型面,沟槽和螺纹等.
(二)角具几何角度前角,10-20度;后角8-15度.
在主切削的后刃面应磨出0.3-0.4毫米宽的切削刃带.刀具其它方面的几何角度根据具体情况选择。
(三)车刀的刃磨要点刃磨车削高温合金用的车刀时,其后刃面磨出切削刃带,前角不磨出角倒棱。车刀刃磨要锋利,刀刃不许有微小的锯齿形缺陷,各切削刃面的粗糙度达0.20以上.后刃面一般磨成圆弧形,以便减少由于磨擦产生的热粘结性,延长刀具的耐用度.刀具其余几何角度的刃磨方法与普通车刀相同.
三.切削用量
由于高温合金具有很高的热性,切屑 不易切离,因此切削用量比车削一般不锈 钢还要低.
(一)切削速度 实践证明,切削高温合金时由于刀具急剧磨损变钝,所以切削速度低,约为加工普通碳钢的切削速度 的1/10.断续切削时,其切削速度 还要小.
粗车时,切削速度40-60米/分(个别铸造合金,切削速度达7.5-9米/分).
精车时,切削速度 60-80米/分.
切削速度 要根据切具材料而定.刀具材好,切削速度 可以适当提高,如,YW1、YW2要比YG6、YG8提高10%-20%。
(二)切削深度
粗车时,切削深度3-7毫米,精车时,切削深度0.15-0.4毫米.
(三)进给量粗车时,进给量0.2-0.35毫米/转;精车时,进给量0.1-0.16毫米/转.
铝镁合金的车削
刀具和切削用量
切具材料常用的刀具材料为YG6、YG8。用于制造外圆内孔、切槽、螺纹、单片多刃刀及简单的样板车刀等。
T12A、W18Cr4V用于制造成型样板车刀.
(二)刀具角度
前角:20-25度.
后角:车削铝合金时,10-12度;车削镁合金时,12-15度.
副后角:10度
主偏角:60-90度.
其余角度与通用车刀相同.
(三)刃磨要点
刀具刃磨要锋利,粗糙度达0.40以上.不磨出负倒棱.特别是对于车削镁合金的车刀,要防止刀刃不锋利产生挤压磨擦,致使高温后产生燃烧事故.
(四)切削用量切削速度 150-500米/分.
切削深度和进给量与车削一般钢材时相同.但切削速度可以提高,以便获得较高的表面粗糙度.
三。典型梯形螺纹车削和所使用的车刀,
1.车削细长轴类工件上的螺纹如丝杠一类的工件时,要注意保证加工中的稳定和防止变曲变形。这时,常使用三个支爪的跟刀架,并在跟刀架爪与工件之间加用铜质套,可取得比较好的效果。
车梯形螺纹中使用的一种车刀,它采用了较大的刃倾角等于被加工梯形螺纹的螺旋角,这样,径向切削力分成三等分,受力均匀,减少了加工中的振动;车刀的后刀面中间和两侧都带弧形,以防止磨擦,增加强度;刀杆成弯形,增大底部接触面积,增加稳定性。车削中选用转速380-475r/min;背吃刀量0.3-0.5mm.粗车量用机油,精车时使用变压器油作为切削液.
另一种形式的普通钢材梯形螺纹 车刀,刀片材料为YT15硬质合金.切削中,选用车床主轴转速750-950r/min;粗车时背吃刀量0.75-1mm;精车时背吃刀量0.12mm;加工中不使用切削液.
该车刀的两面切削刃均具有1-1.5mm宽的度副倒棱;刀刃的后角较小,同时后角下部均磨成圆弧形,较一般刀具强度增高.由于具有以上特点,因此能吃大刀和进行高速切削.
要使用时要将车刀的前刀面用油石研磨至Ra小于0。8微米;并且,要将车床配合部分的间隙调整适宜。工件夹持也应牢固;同时,安装时刀尖应略高于工件中心,以免切削开始时刀具掉尖或崩刃。
2。车削不锈 钢梯形螺纹
车床上加工不锈钢梯形螺纹,生产效率低,质量不稳定。选用合理的车刀几何角度和切削速度,是保证加工质量提高效率的有效措施之一。车削不锈钢梯形螺纹时,推荐使用刀片为YG6硬质合金,刀杆为45锻钢;切削速度22-25m/min.车削时,工件一端用三爪自定心卡盘夹好,另一端用固定顶尖顶好。车刀刀尖安装高于车床主轴中心0.2-0.5mm;加工时使用切削液.
3.车削大螺距梯形螺纹
车削梯形螺纹,当螺距较小时采用的进刀方式为直接进刀,利用不同刀尖宽度的螺纹车刀,分别进行粗车和精车;对于螺距大于6mm的梯形螺纹,通常先用切槽刀车螺纹 槽,然后用螺纹车刀粗车和精车;加工螺距大于12mm的梯形螺纹时,一般采用剥离的方法.
特在螺距的梯形螺纹 ,如果也用上面的方法把螺纹槽内的材料全部切掉,必要花费很多时间,生产效率又低.这时,采用套料车削法可大大减少加工时间.将小滑板转过一定的角度,让切槽刀沿着齿形斜面进刀,先车出槽 ,然后再在另一个像螺旋弹簧似的螺旋圈,这个螺旋圈可以从工件的一端下来.粗加工后还留有加工余量,再进行最后精加工.
梯形螺纹车刀的顶刃宽度B应等于螺纹牙槽底宽W,所以,可使用公式进行计算,即
B=W=0.366P-0.536ac
三角螺纹 的车削
1.三角外螺纹 的车刀
(1)车削铸铁螺纹用的车刀:
刀片材料:YG6、YG8,刀杆材料为45号钢。
刀具的特点:刀尖强度高,几何角度刃磨方便。
刀削用量:粗车时,u=15-30米/分,t=0.2-0.5毫米;精车时,v=15-25米/分,t=0.05-0.1毫米。
(2)车削钢件螺纹 用车刀
刀片材料:YT5、YT15。
刀具特点:刀具前角大,切削阻力小,切尖角经修正后,适于精车螺纹 。
切削用量:粗车时,v=30-40米/分,t=0.3-0.4毫米,精车时,v=20-25米/分,t=0.05-0.1毫米.
(3)高速强力螺纹 车刀:
刀片材料:YT15
加工材料:45号钢和40Cr钢。
刀具特点:刀具前角具有0.2--0.5X(-5度)的负倒棱,两面三刀侧刃后角有1毫米的刃带.刃带起修光作用和增加刀具的强固性,适于高速切削.
(4)车削合金钢的高速螺纹车刀
刀片材料:YT15
刀具特点:经修正的角尖角为59度30分,过渡刃具有3-4度后角.前角为圆弧形(R=0.144P).沿刀尖具有3度前角,故刀尖强度度高.
切削用量:粗车时,v=24-40米/分,t=0.3-0.5毫米,.精车时,v=45-60米/分,t=0.05-0.2毫米.0
(5)高速卷屑螺纹车刀
刀片材料:45号钢和40Cr.
刀具特点:切尖口磨有1-1.5毫米宽-5---8度的负倒棱,并具有较小的卷屑 台,故刀尖强度好.切屑形成球状,排屑良好.
切削用量:v=50-80米/分,螺距为3毫米,t=0.4-0.6毫米.
车削量刀屑应呈卷屑状.如果出现带状,应及时调整切削深度以达到卷屑.
(6)高速钢螺纹 的精车刀
刀头材料:W18Cr4V,HRC=62-65.
加工材料:碳钢、合金钢.等
刀具特点:刀具两侧面刃磨有1-1.5毫米宽的刃带,作为精车螺纹的修光刃.如时刀具前角增大,应修正刀尖角.适用于精车加工精度较高的三角螺纹 .
切削用量:粗车时,v=10-15米/分,t=0.15-0.3毫米;精车时,v=5-7米/分,t=0.05-0.08毫米.
车螺纹时,应选用适当的冷却润滑液.
(7)高速钢螺纹 的车刀: