中国烧结钕铁硼磁体产业在1985 年前后开始量产,宁波科宁达工业有限公司是中国最早量产的钕铁硼企业。在过去的20 年中,中国的钕铁硼磁体产业有了长足的进步,取得了世界瞩目的成绩。世界钕铁硼磁体的生产中心已经转移到了中国,主要集中在宁波地区、山西太原地区、京津地区等。2000 年全球烧结钕铁硼产量为15090 吨,其中中国5550 吨(占37%),日本7700 吨(占50%),美国1020 吨(占7%),欧洲820 吨(占5%)[1]。2001年中国烧结钕铁硼产量约为6400 吨,2002 年为8000 吨,2003 年达到1.5 万吨,成为世界第一的烧结钕铁硼生产大国[2, 3]。从产量上说,中国烧结钕铁硼在2003 年已占世界总产量的73%,日本、欧洲和美国分别占24.5%、1.8%和0.7%[2]。估计2004 中国烧结钕铁硼的产量在2 到2.5 万吨之间,其中宁波地区(包括浙江其它地区)约1 万吨,太原地区约8 千吨,京津地区约5 千吨,其它地区约2 千吨。而生产能力到今年底应能达到3 万吨。目前我国的钕铁硼生产厂大约有150 家,年产1000吨以上的有10 家左右。
从烧结钕铁硼新厂投资建设和老厂扩建来看,2003~2004 年为一个高潮期。2004 年与2003 年相比,生产能力几乎翻番。预计2005 年到2010 年增长会略为放缓。之所以在2003~2004 年生产能力有较快增长,有三个原因:一是实际需求确实有较快增长,增长的生产能力用来满足国际及国内市场的需求;二是前几年对2003 年日本钕铁硼主要成分专利失效有较高期望;三是我国钕铁硼产品的档次有了很大提高,开拓了更广阔的市场。
专利始终是困扰中国烧结钕铁硼发展的一个重要问题,有关情况见表1。从表1 看,2014 年以后日本无论如何也没有道理以专利为由来限制中国了。实际上除了主要成分专利外,关于钕铁硼成分及工艺方面的专利有很多(几百个),例如Intermetallics Co., Ltd 的橡胶模等静压(RIP)工艺及滚镀(BP Coating)工艺、日立金属的湿法低氧工艺、三德金属和昭和电工的甩带工艺、美国坩埚
公司(已关闭)的高氧含量工艺等。中国在钕铁
* Nd-Fe(Co)-B 各向异性磁性材料的专利;
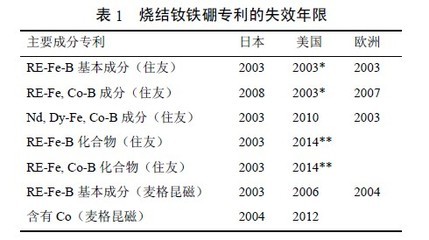
** 美国专利第5 645 651 号含有正方晶结构的化合物专利,至2014 年7 月8 日有效。本专利不仅适用于含有Co 的化合物,也适用于不含有Co 的化合物以及含有Dy 等添加元素的化合物。
硼领域的专利也很多,例如罗阳的“甩带工艺专利”、南开大学周永洽等的“共沉淀还原扩散法制备钕铁硼永磁合金”专利等。所以,可以肯定地说2004 年以后专利的控制会越来越弱,而2014 年以后应该不会起多大作用了。
目前已经购买了住友专利的中国公司有:三环新材料高技术公司、北京京磁技术公司、安泰科技有限公司、北京清华银纳高科技发展公司、宁波韵升强磁有限公司。由于购买了专利,上述公司和中国的其他企业相比在销售上有较多的优势。可以预见,2012 年前后情况会有所变化,专利优势会不再那么明显。因此,从产能上看(考虑到建设周期),2010~2015 年将是中国钕铁硼又一个大发展的时期。
2 产品档次
中国烧结钕铁硼的发展不仅表现在产量上,档次上也有了令人难以置信的提高。正如梁树勇等预见的那样,现在中国的烧结钕铁硼已经大规模进入VCM、MRI、CD pick-up、CD-ROM 等高技术领域。2003 年中国钕铁硼的高技术应用已占到全部产量的30.7%,其中VCM 磁体占1.1%[2]。目前少数厂家已经能够批量生产N53、52M、48H 等高档次产品,达到了世界一流水平。例如,高汝伟等[5]报道的性能如下:a) Br=1.457T(14.57kG),Hci=1148kA/m(14.43kOe),(BH)max=408kJ/m3 (51.3MGOe) ; b)Br=1.32T(13.2kG) , Hci=2035kA/m (25.57kOe) ,(BH)max=320kJ/m3(39.9 MGOe)。至少有5 家企业可以批量生产N50、48M、45H、42SH、40UH 等世界公认的主流高档产品。至于45M、N45、42H 等常规中、高档产品,国内至少有十几家可以生产。实际上,由于激烈的竞争,低档产品已经很难赢利,利润源主要是中、高档产品。预计2005 年中国烧结钕铁硼的高技术应用可望达到40~50%。
这里值得一提的是音圈电机(Voice Coil Motor,VCM)所用的高性能烧结钕铁硼,因为VCM 磁体应用份额的多少能够在一定程度上表明一个国家烧结钕铁硼的生产、应用水平。VCM 磁体在2000年前主要为42M、45M、48M 等牌号的产品,现在主导产品为48M、45H 等牌号。50M、52M、48H也占有一定的市场份额。估计在近五年内基本情况不会有很大变化。VCM 磁体的主要供应商为日本的Neomax 公司(原住友公司)、日本信越、宁波科宁达工业有限公司及日本TDK 公司等。
国内VCM 磁体的发展大致可分成三个阶段。第一阶段为2000~2002 年,此时国内有少数几家公司试图进入低档VCM 市场(例如:42M 产品,韩国、台湾客户等),但由于当时的性能、电镀、氢爆碎等技术尚未成熟,所以未能如愿以偿。
第二阶段为起步阶段,时间为2002~2005 年。此期间有少数中国厂家可以提供少量较低性能的产品给一些小的VCM 客户。有几个较大的钕铁硼磁体厂在尝试通过希捷科技(Segate Technology,Segate)等世界著名的HDD 客户的认证,但直到2004 年底都未成功。值得欣慰的是,在这段时间里,中科三环宁波科宁达工业有限公司在VCM 磁体这一领域取得了巨大的成功。科宁达从2002 年初开始VCM 磁体项目(与Magnequench Ltd.(MQ)合作),在2003 年前后开始大批量供货,主要客户为西部数据(West Digital,WD)、麦拓(Maxtor)、MMI Industries Co. Ltd (MMI)、铭异科技股份有限公司(Min Aik Technology Co., Ltd.)等世界著名的公司。目前的主要产品为48M 及45H,下一个目标为50M、52M、48H 等。计划2005 年达到1.5亿片左右,产值3 亿元左右。
第三阶段为中国VCM 磁体的发展与成熟阶段,时间应该在2005~2015 年。到2015 年底,中
国VCM 磁体的产量应该可以达到世界VCM 磁体总量的50~80%。在这段时间内,中科三环的宁波科宁达工业有限公司、天津三环乐喜新材料有限公司、北京环磁新技术有限公司等都应该有能力生产VCM 磁体。宁波韵升高科磁业有限公司、安泰科技股份有限公司、烟台正海磁性材料有限公司、烟台首钢磁性材料股份有限公司、山西运城恒磁新材料有限公司、杭州永磁集团有限公司、宁波永久磁业有限公司、宁波金鸡钕铁硼强磁材料有限公司、浙江英洛华磁业有限公司等都有可能涉足这一领域。在这一领域最具优势的是中科三环各公司(特别是科宁达)及宁波韵升高科磁业有限公司。科宁达公司的优势在于已经掌握VCM 磁体的制备技术,积累了较为丰富的经验,与MQ 合作,建成了VCM 磁体后加工厂、电镀厂及净房等;韵升强磁的优势在于先进的毛坯设备、一定的规模、一定的经验等。宁波科宁达工业有限公司能够大举进入VCM这一领域,标志着我国钕铁硼企业已经进入高档产品的时代,中国企业只能生产中、低档钕铁硼的时代已经一去不复返了。
3 工艺水平
中国钕铁硼磁体性能档次的快速提高与工艺和设备的进步是分不开的,正是一个又一个的工艺进步奠定了中国烧结钕铁硼大厦的基石。以下以时间为序对此加以总结。
(1)1984~1987 年。这一时期基本上是中国烧结钕铁硼的起步阶段,那时的工艺基本上是“炮
弹式锭模熔炼→鳄破→球磨→管式炉烧结、时效→后加工→磁测→包装”。材料水平基本上是N30、N35 等。
(2)1987~1997 年。在这段时间里中国钕铁硼厂采用了方形双面冷却锭模熔炼,引进了德国
AFG200 气流磨、美国VFS 及ABAR 烧结炉等。气流磨和烧结炉的引进是中国烧结钕铁硼的一个里程碑,使钕铁硼主要的制备工艺技术前进了一大步。在这方面,中科三环、宁波科宁达工业有限公司的王震西、姚宇良等是时代的先驱,为中国钕铁硼的发展做出了重要贡献。在这一时期,日本、欧美等已经开始采用气流磨添加润滑剂工艺、甩带工艺、氢爆碎工艺、双合金法等。中国科学家也开展了这些方面的研究工作,但基本上处于研究阶段,有一些结果也基本上是实验室结果。当然,在这段时间其他相关的方面也取得了很大的进步。例如配方上开始注意Dy、Tb、Nb、Co、Cu、Ga、Mo、W、Al 等元素对磁性能的影响,已经基本上搞清楚了各元素的作用。后加工中的掏孔、轮廓磨、电镀等都有了长足的进步。特别是稀土提取与冶炼技术的进步(可以得到更纯的稀土)对性能的提高也起了很大的作用。
(3)1998~2000 年。梁树勇等[6]报道了将润滑剂(有人称之为添加剂或防氧化剂)成功应用于烧结钕铁硼批量生产并生产出42M、N45 等牌号的产品。他们的工作使中国钕铁硼的工艺水平有了进一步的提高,具有重要意义。添加润滑剂不仅大大提高了气流磨的出料速度,而且可以使剩磁提高20~30mT,磁能积提高16~24kJ/m3。在这段时间内中国钕铁硼企业开始将甩带工艺、氢爆碎工艺及类双合金(主要采用了均匀化处理)工艺应用于小批量生产,并且取得了性能上的
进一步提高。与此同时,烟台首钢、宁波韵升等公司开始购买日本、德国等国外先进的设备,包括甩带炉、氢爆碎炉等。先进的设备为先进工艺的实施提供了基础。
(4)2001~2005 年。这是中国烧结钕铁硼大发展的一个阶段,预计2005 年的产量是2001 年的
4~5 倍。烟台正海、烟台首钢等报道了批量生产N53 等产品,宁波科宁达工业有限公司已经大举进军VCM 等领域,说明中国的烧结钕铁硼企业已经摆脱了只能生产中、低档产品的局面,正在义无返顾地向高端市场进军。这段时间中国较大的钕铁硼厂都已经基本掌握了甩带工艺、氢爆碎工艺并将新工艺应用于批量生产。甩带工艺的关键是合格的甩带炉,如果有合格的甩带炉并得到合格的甩带片,则甩带工艺的掌握并不难。与甩带工艺相比,对氢爆碎(HD)工艺的掌握才是近几年钕铁硼工艺飞跃式进步的关键,这不是一般的里程碑,而是中国钕铁硼发展史上的一块丰碑。是否采用HD 技术是中国烧结钕铁硼与国外工艺技术的最重要差别之一。不论是甩带技术,还是双合金技术等公认的先进技术都离不开HD 技术。HD 技术是高性能、高品质烧结钕铁硼制备中不可缺少的一步。所谓HD 技术就是将铸锭或甩带片用H2 处理(反应可在常温或200℃左右进行,H2 压力一般小于0.3MPa),然后于400~600℃脱氢。经过氢爆碎处理后,钕铁硼的铸锭或甩带片已变得非常疏松,经过中破,然后进气流磨或氢爆碎后直接进气流磨。此时出粉速度是传统工艺的2~3 倍,大大提高了气流磨的效率,降低了成本。氢爆碎后不仅提高了出料速度,而且可以将钕铁硼粉磨得更细(例如2.8~3.5μm。传统工艺一般在3.8~5.0μm。),从而可使成品磁体的晶粒尺寸达到10μm 以下(传统工艺的晶粒尺寸为20~40μm)。晶粒尺寸的变小意味着矫顽力的提高,同时大大提高了磁体的抗腐蚀能力。
4 设备制造水平
毫无疑问,中国钕铁硼的发展为钕铁硼设备制造商提供了很好的机会,大多数厂家也确实赚足了钱,但同时我们也要看到,正是中国许多设备厂家的努力才使中国的钕铁硼有了今天辉煌的成就。
4.1 熔炼炉
熔炼技术基本上由前往后的顺序是:炮弹状(式)锭模、方形双面冷锭模、转盘锭模及甩带。由炮弹状(式)锭模到方形双面冷锭模是一个较大的进步,与炮弹状(式)锭模比双面冷有效地抑制了α -Fe 的析出,所以对提高剩磁有利。目前大多数小厂的主流熔炼方式仍然是这种方式,一般锭子厚度在20~30mm。转盘锭模熔炼对提高熔炼效率有帮助,现在常见的是50kg 和100kg 两种。转盘锭模熔炼锭子的厚度在15mm 左右,锭子表面易凸凹不平,对于一般性能的产品在成本降低上有一定的好处,但对制备高性能产品没有明显优势。如果锭子表面凸凹不平,则难以打磨(特别是许多高性能产品的锭子需要经过均匀化处理时),易产生气孔、沙眼等,同时由于混入一定量的氧化皮而影响磁性能。
甩带炉的研发成功是钕铁硼熔炼设备的一个巨大进步,是中国钕铁硼发展史上的一个里程碑。有了廉价的国产甩带炉,才使甩带工艺的采用成为可能。甩带工艺又称带铸工艺或速凝薄片工艺。这种工艺最早由日本的三德金属(仅提供速凝薄带,不生产磁体)与住友金属采用并获得专利权。带铸工艺的特点在于有效地消除了α -Fe,富钕相均匀并使晶粒得到细化,有益于生产高剩磁及高矫顽力产品。实际上早在1990 年代初,钢铁研究总院等科研院所就已经开始甩带设备的研究,但那时主要目的是制备快淬粉。真正将目标定在烧结用甩带的甩带炉的研制要追溯到1997 年,在这一年沈阳中北真空开始了这项工作。中北真空首先推出的是50kg 双辊甩带炉,这种炉并不太成功,存在带子粘结、厚薄不匀、滚轮卡死等问题。后来改成单辊甩带炉,解决了上述问题,所得带子的质量与国外产品不相上下,与三年前的带子相比[4]更是进步极大。现在的主流甩带炉为150kg、200kg 等。中北真空已经与日本真空合作生产600kg 甩带炉,预计质量上与日本的甩带炉不会有什么差别。现在甩带炉供应商不止中北真空一家,主要集中在沈阳、锦州、北京等地。
4.2 中碎设备
过去中碎主要是鳄破→对辊(或带筛球磨)→锥磨等。现在一般采用粗锤破→(氢爆碎)→锤磨。
新工艺节省了时间,提高了效率。一般一台锤破设备每小时能够处理200kg 左右的锭子,粗粉粒度50~200 目,粒度分布偏宽,细粉太多。如果以后都采用甩带工艺,则直接氢爆碎,无须中碎一步。
4.3 氢爆碎炉
氢爆碎炉的分类[9]有两种方法,一种根据加热方式,另一种根据运动方式。根据加热方式可分为
内热式和外热式两类,根据运动方式可分为静止式及旋转式两类。目前我国国内用于烧结钕铁硼的氢爆碎炉主要有日本岛津、德国NKE POWDERTECHNOLOGY GMBH、太原开源永磁设备有限公司、山西金开源实业有限公司、浙江省奉化百达机床厂、北京博睿华创磁电设备技术有限公司等公司的产品。太原开源永磁设备有限公司、山西金开源实业有限公司是我国专门生产用于钕铁硼氢爆碎的氢爆碎炉的鼻祖,后起之秀为浙江省奉化百达机床厂。太原开源永磁设备有限公司和山西金开源实业有限公司的QS-1 型氢爆碎炉于2001 年出厂,QS-500 型于2002 年出厂。QS-500 型为我国目前的主流产品,现有20 多台应用在各钕铁硼生产厂家。
4.3.1 山西金开源实业有限公司QS-1 型氢爆碎炉
这种氢爆碎炉设计较为简单,成本低,基本组成可以分成两部分:第一部分为桶形不锈钢反应
器;第二部分为加热包式脱氢炉。其形状根据装炉及出炉方式不同,每炉可装100~200kg。冷水浸泡式冷却。由于钕铁硼物料不直接与桶壁接触,所以冷却速度较慢,一般一个循环需要24h 左右。
4.3.2 太原开源永磁设备有限公司QS-500 氢爆碎炉
QS-500 为外热式旋转氢爆碎炉。它的基本组成也是两部分:第一部分为可旋转双口不锈钢反应器;第二部分为对扣加热包式脱氢炉。在安全方面,具有气体操作安全内锁系统,包括爆破盘、卸压阀(两级)、断电自动充氩保护、吸氢负压时自动充氩减缓反应等,加热脱氢为外热式,动密封采取磁
流体密封技术。冷却为喷淋水冷式,成本较低,但水气对环境有害。装炉有两种方式:一种为螺旋喂料,另一种为振动喂料。实际使用中发现装炉不太理想。出炉为螺旋旋转出炉,可直接接料桶,较为方便。由于采用了旋转,所以吸、脱氢彻底、均匀。QS-500 每炉可装600kg,每个循环约15h。
4.3.3 奉化百达BDR300 氢爆碎炉
BDR300 氢爆碎炉为浙江省奉化百达机床厂的第一代产品,它属于外热式、旋转氢爆碎炉,与QS-500 氢爆碎炉有类似之处。从安全上看,与QS-500 氢爆碎炉一样采取了很多措施。其中包括全自动安全互锁功能、爆碎盘、卸压阀、断电自动充氩保护、吸氢负压时自动充氩减缓反应等安全防护措施。从操作及控制方面看,有PLC 控制、温度和压力监控等措施。从氢爆碎效果看,与其它旋转式氢爆碎炉一样,物料吸氢与脱氢彻底、均匀。设计温度800℃,使用温度600℃或600℃以下。处理量约300kg/炉,每个循环约6h。该氢爆碎炉的特点包括如下几点:(1)反应罐水平放置,减小了各个连接法兰出故障的几率,特别是不容易损坏磁流封。(2)反应罐可以由水平变为竖直,并且一端接有法兰,所以可以直接对接加料罐和出料罐。物料不与空气接触,装料及出料都非常简单并且防止了可能的物料氧化问题。(3)第二代产品采用独特的加热系统使物料及反应罐在10min 左右就达到脱氢温度,大大缩短脱氢时间,节约用电。(4)独特的风冷设计使冷却时间缩短到2.5~3h。由于使用空气风冷,与氩气和水冷相比成本较低。
4.3.4 北京博睿华创ZQTL-500I 氢爆碎炉
ZQTL-500I 氢爆碎炉为类烧结炉式氢爆碎炉,属于内热、静止式氢爆碎炉,每炉可处理500kg 物料。整个控制系统为PLC 控制,设有全自动安全互锁功能及断电保护功能;所有气路管道采用专业化进口双保险安全阀设计;设有炉内跟踪控制和炉外采样监控的控制系统,具有完善的报警及防爆措施。
该炉的另一个特点是强大的跟踪记忆功能:可储存多条工艺曲线,可记录全部工艺过程的压力、
温度等,便于工艺分析、质量监控及生产管理。该炉的有效尺寸为?900×L2000mm;设计温度800℃,使用温度室温~600℃;升温速率> 15℃/min;电源380V、50Hz、180kVA。
4.4 气流磨
我国的气流磨基本上都是模仿德国细川阿尔派的设计。从技术发展的角度看,在这方面没有特别的进步。从粒度分布比较看,仍然与细川阿尔派有一定的差距。可是,由于采用HD 锭料或甩带片非常脆,极易磨细,所以对气流磨的要求反而低了,现在的气流磨也基本上能够满足要求。将来应在喂料速度控制、补氧控制等方面做一些改进。宁波科宁达工业有限公司已经购买了AFG400 气流磨,使用情况良好,这可能也是将来大企业的一个方向。
4.5 压机
刚开始生产钕铁硼时使用的是平行压压机,后来基本上都改为垂直压压机,这也是技术上的一大
进步。一般气隙50mm 时的成型定向磁场都大于2T。我们认为今后有两个努力方向:一是采用脉冲磁场,进一步提高磁场,磁场到5T 后剩磁会有进一步的提高;二是全自动压机,包括自动喂料和自动码盘。我们已经看到全自动压机的雏形样机,但用于生产恐怕至少还需要两年。
4.6 烧结炉
4.6.1 三点控温烧结炉
十多年前我们进口了ABAR 炉和VFS 炉,后来许多厂家仿造了这两种炉子。当时这两种炉子仅仅是一般的热处理炉,并非为钕铁硼生产专造。它们的最大缺点是一点控温,所以炉温的均匀性很难调节。经过十多年的发展,中国的烧结炉制造厂家已经基本掌握了专用于烧结钕铁硼的烧结炉制造技术,而且都实现了三点控温。梁树勇等[4]在2002年前后曾经认为我国自己制造的烧结炉与国外无差距,而且由于专门针对钕铁硼工艺设计,所以许多指标优于国外产品,现在看来那时是过于乐观了。由于采用了三点控温,所以前、中、后区的温度确实容易调节了,但我们在使用中发现上、中、下的温差仍然是个很大的问题,看来还有许多工作要做。
4.6.2 分压烧结炉
我们现在基本都是使用真空烧结炉,烧结过程在真空中进行。国外许多厂家采用分压烧结,也就是说在烧结过程中充入少量氩气,但仍保持负压。从理论上讲,由于分压烧结的热传导优于真空烧结,所以烧结时的温度一致性好,而且可以缩短烧结时间。这种新型烧结炉已经出现,到底效果如何需经至少两年的考验。
4.6.3 连续烧结炉
住友等国外大公司都是采用多室连续烧结炉,它的优点在于炉温均匀性、一致性好,能耗低、效
率高。过去我国有些厂家曾经尝试过制造这种多室连续烧结炉,但以失败而告终。究其原因,主要是闸板阀不过关,烧结炉漏气,造成产品氧化。现在日本的产品一般为5 室或6 室烧结炉。6 室烧结炉包括下列各室:(1)预备室,(2)200~300℃脱添加剂室,(3)850℃左右放气室,(4)烧结室1,(5)烧结室2,(6)气淬室。烧结分两室进行是因为整个工艺为连续运行,要求每一步有大致相同的时间。现在中北真空已经与日本真空在沈阳合资建厂,技术上应该没有问题,所以价格较低的连续式烧结炉可望在我国实用化。
4.6.4 微波烧结炉
已经有一些研究单位开始研究将微波烧结用于钕铁硼生产。从原理上讲,微波烧结有利于炉心
部位与炉边部位温度的一致性,同时大大缩短烧结时间,节约能源。目前得到的信息是烧结时间可以缩短到1h。但是这种烧结炉基本上还处于研究阶段,推广应用至少要4~5 年时间。一旦成功,这将是一种革命性的变革。