2000年前雄称日本六大钢铁公司的新日本钢铁(新日铁)、川崎制铁(川铁)、住友金属
工业(住金)、日本钢管(NKK)、神户制钢所(神钢)和日新制钢(日新),随着日本经济的衰退,他们经过认真研究和探索,寻求了一条新的生存发展之路---合并重组资源共享。
日本的六大钢铁公司重组成两个集团统一组织经营和生产。具体的组织构成如下:
(1)NKK与川铁的合并
NKK与川铁的合并事宜于2001年5月宣布,2001年12月21日公布了合资经营的计划,合并后的公司名称为JFE(J-Japan,F-Fe,E-Engineering)集团,于2002年10月成立持股公司。
JFE集团公司由现川崎制铁董事长江本宽治担任董事长职务,日本钢管总经理下坦内洋一就任总经理。2003年4月成立下属钢铁、工程技术、城市开发、半导体、研究开发等5个股份分公司。重组后的钢铁主业公司---JFE钢公司由现川崎制铁总经理数土文夫担任总经理职务,现日本钢管副总经理半明正之出任董事长,现日本钢管副总经理土手重治就任JFE工程技术公司总经理。
生产经营计划合并后年粗钢生产能力为2500万吨,规模与新日铁持平。通过设备重组调整后,将减少产量200万吨。通过统一经营,到2005年降低成本800亿日元。其中自然减员6000~7000人,减少费用300亿,降低生产、维护、运输成本和设备集中减少费用200亿。到2006年3月销售额与现在持平的话,可获利润2000亿日元(2002年3月单纯预计利润为零)。
合并后共分3个生产基地。一个是以京浜(NKK)和千叶(川铁)为主的东日本钢铁厂;另一个是以水岛(川铁)和福山(NKK)为主的西日本钢铁厂;第三是知多制造所钢管生产基地。
(2)新日铁阵营
日本铁老大新日铁在经济不景气的持续下,为了维持老大地位,不得不考虑新时期的适应对策。
在NKK与川铁将于2002年10月正式成立合营公司前,新日铁也加紧了与其它公司的联合事宜商谈。2001年12月4日发布了与神钢合作的消息,11日接受了住金的合作要求,22日同意与日新制钢合作。至此,一家由4家公司组成的钢铁联合体即将正式形成。该联合体今后将主要在半成品铁源的相互调剂供给、原材料的采购、物流的共用、设备的集中优化报废以及不锈钢的开发等领域进行合作,以降低生产成本和提高收益,与NKK-川铁集团进行抗衡。预计将在2003年内出台具体的措施和计划。
新日铁当时除了加强国内的联合外,还抓紧了与国际上一流大钢铁公司,如法国于济诺尔、韩国浦项、中国宝钢、中国台湾中钢公司等公司的联系与战略性合作。
日本钢铁设备制造厂重组情况
日本钢铁设备厂家先于钢铁公司的重组,早已开展了大量的合并重组,并已开始了营业和技术方面的实质性合并活动。
(1)设计、制造和工艺的组合体
2001年5月开始的JSP(JapanSteelPlantech)公司由日立造船、住友重机和日本钢管3家公司共同出资组建。旨在日本和海外设计、制造和销售钢铁设备方面占一席之地。已进入了宝钢的厚板连铸机项目的角逐。
(2)老牌轧机制造厂的强强联合体
2001年12月21日由三菱重工业和日立制作所发布了两家公司各出资50%,于2002年4月1日正式组建全面联合钢铁设备的设计和供货的销售公司,同时将资本金增加3倍,以提高在订货活动中的信誉,组成在轧机领域独占鳌头的阵营,已经活跃在了上海一钢的不锈钢工程。另外还兼并了宇部兴产的平整机部分,使轧制线设备更精锐、更完善。
从日本当时钢铁工业的重组措施可以看出,通过强强联手,减少整个行业不必要的恶性竞争,在业内形成寡头竞合的局面,完善了整个日本钢铁工业的供应链,这样极大的提高了日本钢铁工业的核心竞争力。在行业整合过程中,以资本为纽带,以优化供应链为考量,综合考虑到业务和资本各个方面的关联。只有这样才能发挥整个行业的合力,得到最大的收益。
日本轧制理论和轧辊的发展
1、轧制解析
众所周知,日本的轧制技术以理论为基础,始终处于世界先进水平。为解析板材轧制中的板材形状和中间凸度的原理,对轧机的弹性变形条件和被轧材的塑性变形条件进行了联立求解。采用将弯曲和剪切挠曲的材料力学模型进行扩展或校正的方法对各种类型轧机进行解析的方法已基本确立。另一方面,关于材料的塑性变形,采用了三维解析法,使解析由二维理论向高精度解析发展。在解析法的发展方面,有采用数值计算法忠实解析变形的所谓三维解析法,有刚性和塑性FEM,有弹性和塑性FEM,尤其是还有为缩短计算时间而将上述方法进行组合的解析法。
在孔型轧制方面,一般说来纯理论处理是极为困难的。作为一种简便的方法,虽然可以采用所谓的矩形换算法把孔型轧制替换为适当的矩形断面材的扁平轧制,但无法获得高精度。提高精度用的实验式和半理论式在简单推测随孔型和轧制条件变化时的变形特性和负荷特性方面依然是一种有效的方法,但目前一般是采用FEM解析。由于FEM的出现,使材料的三维解析变得可能。它不仅可以用于板材的解析,而且还可以用于型材、棒线材和管材的轧制力、轧制载荷、轧制力矩和宽展的求解。三维FEM解析作为一种有效的解析工具已得到人们的认可。
人们期待着今后能向轧制温度解析和将轧制加工时的材料组织变化,尤其是将轧制缺陷解析系统组合起来的综合轧制理论方面发展。
2、变形阻抗
变形阻抗值是计算轧制载荷和轧制力矩时的重要物理特性值。日本钢铁协会轧制理论研究会已对变形阻抗值的研究数据进行了充实和收集,并采用数学模型进行了研究。
在热变形阻抗方面,采用考虑到多道次高速连续轧制时的累积应变效应的变形阻抗公式进行计算后,显著地提高了热变形阻抗值的预测精度。为把考虑到材料组织变化的轧制理论进行扩展,希望能建立对材料的硬化、恢复和再结晶等现象同时进行跟踪的理论体系,积累一些与合金成分相对应的能对冶金现象进行定量化的数据。
在冷变形阻抗方面,通常是采用考虑到温度和应变速度相互关系的动态变形阻抗公式进行计算。
3、轧制润滑和轧辊
随着冷轧速度的高速化(最大2800mpm),为获得摩擦系数的定量值,开发了高速轧制模拟装置和双圆筒滑动试验机,严格计算流入油膜的厚度,对轴与轴承等的热胶着进行了评价,提出了表面光泽度的推定和控制系统,并对轧制润滑油进行了改进。作为工作辊材质,一般是将高碳Cr系锻造材进行表面淬火后,使微细碳化物在完全变为马氏体的基质中大量析出,形成硬度高的组织,但由于轧制方面的要求越来越高,因此加快了对镀Cr和喷镀WC-Co来提高耐磨性的研究和高速钢及陶瓷新材质的研究。轧辊表面的加工也从喷丸清理变为电火花加工,或采用电子束和激光束等进行加工,使轧辊表面加工得更加均匀、轧辊形状更加妥当。
在热轧过程中,确保材料的咬入性能,提高轧辊的耐磨性,防止轴与轴承等的热胶着是重要的课题。目前轧辊一般是使用高速钢,但希望开发出高载荷轧辊和轧制工具,以适应更大的压下轧制要求。
提高轧辊和轧制工具的耐磨性、抗事故性和抗桔皮状缺陷性是轧制技术飞速发展所不可缺少的重要技术,从减轻环保压力的观点来看,这些技术要素今后也是很重要的。
日本钢板轧制理论和技术发展
1、连续轧制和直接连接轧制
日本自1968年开发了森吉米尔式多辊轧机的全连续式串列式冷轧机(TCM)和1970年开发了四辊轧机的全连续式TCM以来,轧机的连续化已取得很大的进展。目前日本国内的主要轧机都实现了完全连续化。由于完全连续轧机的技术可以和轧机的上下工序连接,因此1986年开发出了酸洗-TCM-连续退火成套设备。完全连续化的开发包括了轧制生产计划可以随意变化、稳定焊接技术、带材稳定移动技术、前进方向可变装置等。在冷轧的连续化之后,1996年首次在世界上开发出了热轧的连续化技术。它是在粗轧结束后将前后轧材在进入精轧机前进行焊接,使精轧机在无切头切尾的状态下进行无头轧制的技术,解决了产品前后端部的质量问题,同时使极薄钢板和新材质钢板的生产技术变得有可能。
自1989年将50~100mm厚的薄板坯连铸机和轧机直接连接的紧凑式轧机诞生以来,其建设数量逐年增加,目前在日本以外的国家中至少已建设了50套。紧凑式轧机的特征是设备投资少、交货期短,可进行没有水冷滑轨造成黑印的等温轧制,如果采用长的板坯,还能进行半无头轧制,可以预计今后其应用将越来越广,同时能进一步提高产品质量。另外,将来带钢连铸机应用的趋势引人关注。
2、新型轧机
关于轧机辊距的控制,轧辊项弯装置是关键。众所周知,日本以20世纪70年代后期出现的六辊变速轧机(HC轧机、UC轧机)为契机,开发了交叉辊薄板轧机(PC轧机)、双轴承座顶弯装置(DC-WRB)、在小直径工作辊上装有侧支撑辊的六辊FFC轧机、Z-Hi轧机、多辊型CR轧机、KT轧机、轧辊本身具有可变凸度型的VC轧辊、TP轧辊、NIPCO轧辊,还有采用在线磨削的轧辊磨床(ORC)等,这些新型装备为世界轧制设备的发展做出了很大的贡献。另外,还研究开发了采用1机架多道次轧制技术的各种轧机,但其应用仅限于特殊材的轧制。
3、板材中心凸度部分和板材形状的控制
板材轧制时的中心凸度部分和板材形状的控制是对同一现象进行控制的技术。由于前者的控制精度在数微米至数十微米就可以了,而后者的控制精度应在0.1μm或小于0.1μm,因此被视为不同的技术。在对比较厚的钢板进行热轧时要控制板材的中心凸度部分,冷轧时要将中心凸度部分比率保持一定,在考虑形状后进行薄壁化轧制。虽然这是常规操作法,但由于板材端部容易产生三维变形,因此开发了控制边缘凸度的技术。例如,有采用立辊轧机减少边缘损失的方法;在轧机上下辊之间使圆盘状水平辊向板的两边挤压,一面约束宽度一面进行轧制的方法;还有采用带有锥度工作辊的轧机和交叉辊轧机进行轧制的方法。因此,可以预计今后仍将积极利用三维变形的技术来控制板材中心凸度部分。
在形状控制方面对板厚(轧辊间隙形状)控制的精度要求非常严,这是因为只要控制精度有一点点的偏差,板材就会出现板厚偏差很大的形状缺陷。陡度在0.5%以下,就可以视为形状良好,延伸率偏差为6.2×10-5(6.2Iunit),1mm板厚的压下量偏差为0.06μm。因此,实现高精度轧制当然离不开轧辊的局部矫直和材料的横向移动所产生张力的缓和稳定作用,但在轧制过程中使轧辊间隙形状和板材的中心凸度部分一致是控制形状的基础。轧辊挠曲、热凸度、母材形状、机械试验值的偏差和轧辊磨耗等会对轧辊间隙形状和板材中心凸度部分产生影响。为精确控制形状,必须对从低次函数到高次函数这一大范围内的形状偏差进行修正,因此将新型轧机的形状控制传动装置进行组合,采用多变量控制理论等复杂而又精密的控制方法进行形状控制的趋势将进一步增大。
4、板厚控制
随着钢板加工自动化程度的提高,为排除加工过程中的故障,用户对钢板制品的板厚精度要求越来越高。将支撑辊的油膜轴承替换为滚柱轴承,采用高性能油压压下装置消除和控制轧辊偏心已取得很大的发展。作为轧机用传动装置,所有AC传动装置都形成了标准数字化控制。AC传动装置的优点是,
自1953年日本钢铁产量超过战前以来,经济高度发展,产量飞速提高。20世纪70年代初期产量超过了1亿t,成为世界屈指可数的钢铁大国,其后产量一直保持在1亿多吨,并努力使生产技术处于世界领先水平。
日本钢铁工业的发展以战后从欧美各国引进技术为基础,通过迅速对其进行改进和创新,开发了具有自主知识产权的技术。在轧制工艺方面,20世纪60年代至70年{BANNED}发了高速轧制技术,20世纪70年代至80年{BANNED}发了连续轧制技术,自20世纪80年代以后,开发了轧制尺寸精度高、产品质量高和不受工艺过程约束的轧制技术及应用这种技术的新型轧机。最近以适应环保要求为目的的轧制工艺引人注目。以下主要就20世纪80年代以来日本开发的具有自主知识产权的轧制技术的发展历程进行概述。
在结构上已完全采用电刷、单机容量增大,在性能方面已达到高精度、高应答化、可变速度范围扩大。
在以往的板厚控制装置中有自动测量调整装置(AGC)、监视AGC、FFAGC和游标尺AGC。在最新的串列式轧机中,在此基础上还开发了轧机速度数字化控制、轧辊偏心控制、机架间的无干扰控制和在线板厚变化控制等技术。尤其是为使连续式轧机能在不停机的情况下对轧机入口侧依次焊接的钢种、板厚、板宽不同的材料进行连续轧制,因此通过抑制张力过度变化,协调地改变各机架的轧辊位置、轧制速度等在线板厚变化控制技术是很重要的。由此可大幅度减少板材穿过轧机和切头切尾落料造成的轧辊损伤和板材等外品,同时提高对小批量订货的适应能力。另外,它也是紧凑式轧机实施无头轧制所不可缺少的技术。
5、平面形状和板宽控制
在厚板和热轧钢板生产工艺中,板宽浇注技术在20世纪80年代就已确立其基本技术。在厚板生产方面有大幅度提高合格率的平面形状控制新技术MA(MizushimaAutomaticPlanViewPatternControlSystem)轧制法和附设的接近水平轧机的立辊轧机设备。MAS轧制就是对各种钢板在轧制终了后的平面形状控制变化量进行预测,根据预测的变化量,给出轧制过程中板坯厚度形状,最终将平面形状变成矩形的方法。热轧时实现将连铸机和轧机有效直接连接的板坯宽度定径技术、大幅度提高热轧钢板宽度精度的热轧板宽度控制技术、精轧时利用机架间的立轧机和张力控制来提高尺寸精度的技术、尤其是采用冷轧TCM和冷轧工艺线的板宽控制技术等都是日本开发的领先于世界水平的独有技术。
日本钢管轧制理论和技术发展
在最近20年的发展中,首先应举出的是无缝钢管用钢坯的连续浇铸技术。随着圆钢坯质量的提高和制管技术的进步,采用热挤压法生产的13%Cr钢和奥氏体系不锈钢已改变了轧制方式。最近已开发了圆坯连铸和制管、热处理直接连接的技术。
1、穿孔轧制
使用方钢坯的PPM(压力辊穿孔机)已被替换为使用圆钢坯的斜辊穿孔机。在穿孔方法变化中值得注意的是圆锥形穿孔机和被称作交叉穿孔机的交叉辊穿孔机的发展。圆锥形穿孔机的优点是具有旋转锻造的效果和抑制圆周方向剪切变形的作用,因此可以抑制钢管内面的缺陷,可用于难加工性材料的穿孔,尤其是可以用于扩孔和薄壁穿孔。采用普通穿孔机时,壁厚/外径比(T/D)的极限为大约6%,而采用圆锥形穿孔机时能进行T/D为3.2%的薄壁管穿孔。
2、拉伸轧制
芯棒式无缝管轧机已向大型化和紧凑化方向发展。机架数由7~9机架减为4~5机架,穿孔机和芯棒式无缝管轧所需的能源消耗共计可减少20%左右。
在芯棒式无缝管轧机的控制技术中,为减少其后在张力减径机中管端壁厚的切头损失,开发了管端预先减薄成形技术,即用芯棒式无缝管轧机预先将管端减薄的成形技术,并在钢管轧机上首次采用了油压压下装置。
3、减径轧制和定径轧制
虽然在最终调整外径的减径轧制和定径轧制方面没有值得特殊介绍的技术发展,但大口径定径机有许多也采用了三辊式定径机。采用三辊的缺点是辊距无法变更,因此机架的台数多,但最近出现了辊距可变的轧机,还提出了四辊减径机的想法。今后芯棒式无缝管轧机和定径机及张力减径机的直接连接技术也将引起人们的关注。
以上所述的钢管领域中的高合金穿孔用芯棒的开发和芯棒及毛管坯导槽润滑剂的开发等与摩擦学技术有很大的相互关系,因此希望长寿命化技术有进一步的发展。
日本型钢轧制理论和技术发展
以第一次石油危机为契机,型钢生产也由转炉-铸锭-开坯,变为转炉-连铸。型钢的轧制技术有采用轧制工字梁用异形坯生产多系列型钢的技术和采用板坯轧制H型钢的技术,型钢轧机用的坯料已改为连铸坯料。最近10年,钢轨、钢板桩和H型钢等大型型钢的轧制技术已取得了显著的发展。
1、外部尺寸一定的H型钢
随着建筑结构件生产技术的高度发展,断面性能高且经济性好的外部尺寸一定的H型钢采用斜辊轧制的方法和缩小H型钢腰部高度的轧制方法已应用于实际。前者在精轧前为使腰部外部尺寸保持一定,扩大了腰部内部尺寸;后者为在精轧机内使腰部高度保持一定,缩小了腰部高度。结果,能在线变更水平辊宽度的辊身宽度可变水平辊和立辊轧机孔型深度可变的偏心立辊轧机也应用于实际。另外,由于在万能轧机上采用了油压压下装置,因此轧机变得非常紧凑。随着断面的大型化,普通的单臂式矫直机已无法满足要求,开发了双臂式矫直机,但由于存在着占地空间大和轧辊更换操作复杂的问题,因此需进一步改善。
2、宽幅钢板桩
以往宽幅钢板桩以400mm宽的U形钢板桩为主,一般是使用连铸板坯在3~4架的二辊式轧机上由8~10个孔型反复轧制而成。还开发了在H型钢轧机作业线上不更换H型钢轧制用机架,只更换轧辊生产钢板桩的方法。另外,随着工程的大型化和提高施工效率的需要,600mmU形钢板桩和900mm宽的帽形钢板桩已能商业化生产。
3、钢轨
钢轨一般是在数架二辊式轧机上采用孔型轧制的方法进行生产的。随着对产品尺寸、质量要求的不断提高和降低轧辊成本的需要,采用万能轧机进行中轧和精轧的技术已成为主流。钢轨的磨损主要是线路曲线部与车轮凸缘部的摩擦磨损,因此在1994年将钢轨全部换成上部整个断面经在线热处理后的钢轨,作为防止磨损的措施。
另外,以阪神大地震为契机,在厚板生产领域发展的TMCP法和氧化金属喷镀技术已开始应用于建筑用钢材的生产,TMCP极厚H型钢、低屈服比外部尺寸一定的H型钢和耐火H型钢已能商业化生产。
日本棒线材轧制理论和技术发展
在棒钢和线材轧制中为追求提高生产率、提高尺寸精度和产品质量满足市场需求,开发轧机的尺寸可调轧制和控冷控轧等新功能的工作取得了进展。
1、无头轧制
棒线材产品的种类非常多,因此开发了一种热方坯焊接后连续轧制的设备(配置了直流式对焊机和去毛刺装置),该设备投资小、无短尺和尺寸不齐现象、实现大单重卷、可消除轧废时间、增加产量等。其应用范围今后将进一步扩大。
2、高速轧制和控制冷却
线材精轧的特征是变形速度快、从孔型间通过的时间短,由于设备紧凑,因此轧制后必须快速冷却,它也可作为控制材质的手段。
在20世纪80年代左右,最高轧制速度为60~75m/s,90年代左右提高到100m/s,目前已达到100~120m/s,大大提高了线材的生产率。润滑技术的改善和轧机刚性的提高为此做出了很大的贡献。
由于优化了线材的轧制温度和轧制后的冷却速度,因此可以省略冷锻用钢的软化退火。另外,为降低汽车等行业使用的机械用结构钢的成本,非调质化技术已取得很大的发展。尤其是从地球环保的观点来看,无铅易切削钢已应用于实际。
3、高尺寸精度和尺寸可调轧制
为实现高精度、尺寸可调轧制,因此在现有轧机上安装了控制系统(软件),通过控制轧辊的旋转数来控制张力、调整精轧尺寸,还有的是采用定径机等硬件设备的方法。后者采用二辊方式大大提高了轧机的刚性,能进行±0.1mm的高精度轧制,同时通过调整轧辊的压下,能在大约1mm的范围内进行尺寸可调轧制。尤其是,还开发了具有宽展小的三辊、四辊式定径机,能根据棒线轧制的需要和轧制环境进行选择。
随着全球钢铁生产能力的大幅增长以及产品需求结构的变化,日本钢铁业决定调整投资战略,优化产品结构,减少通用普通钢材的投资和生产,将投资重点放在高附加值产品的开发和生产上,以提高日本钢铁产品在国际市场上的竞争力。
日本钢铁业认为,如果全球钢铁产能不断增长,市场供求关系将发生逆转,供大于求导致价格暴跌的问题难以避免,因此有必要调整钢铁业投资战略,逐步淘汰或减少建筑用型钢和板模钢以及其它中低档通用钢材的生产,增加对汽车、船舶、电子机械、电器所需的高档钢材的投资。
日本钢铁业同时认为,应加强同中国这个世界最大钢材消费市场的合作,建立海外生产基地和销售渠道,减少钢铁贸易摩擦。
日本十年来钢铁技术开发代表性成果
1.铁水预处理工艺的重组
为取代过去在铁水罐车和铁水包内进行的预处理,各厂开发成功各种用转炉的预处理法(H炉法、SRP法、NRP法、MuRc法、LD-ORP法),大幅提高了脱磷效率,减少了对外排渣。个别工厂已实现全部铁水预处理。
2.环境友好型精炼工艺
由于环保意识的提高,十分重视减少钢渣外排技术的开发,使钢渣外排总量达原来的1/2,突出的如彻底脱硅的零排渣工艺。还开发成功含碳渣用于烧结矿和铁水脱硫,钢渣制砼用于护岸材,用含铁粉尘制球团矿等再生利用技术。有的厂已作到了炼钢固体废物为零。
3.电磁力应用技术的革新
从初期的电磁搅拌和局部作用的电磁制动发展到后期的可适应钢水的加减速而切换的电磁设备、在铸坯宽度方向均匀磁场的静磁场制动以及结晶器内钢水流动的模拟计算软件。
4.高质量技术
不断进行提高产品质量的技术开发,坚持了洁净钢技术开发。在硬件方面,二次精炼中增加燃烧器后使RH多功能化,开发成功连铸坯防止裂纹缺陷的技术。在软件方面亦开发成功预测产品质量的技术,使轴承钢中的含氧量由1994年的5ppm降到2001年的4.7ppm,最好时达3ppm左右。
5.高速连铸技术
在国际上薄板坯高速连铸法飞跃发展的10年间,日本的薄板坯连铸仍未实用化,只是在后期为适应钢铁需求的增大而提高了现有连铸机的生产效率,出现了单机月产超过20万t的连铸机,拉速已达3m/min水平。关于带钢连铸,各厂均开展了研发工作,最终只在新日铁光厂的不锈钢生产上实用化。
日本钢铁行业铁矿石战略
澳大利亚和巴西的矿产资源相当丰富,而且铁矿石纯度较高,是日本的主要进口来源国。日本企业通过直接投资或参股的形式,在澳大利亚与巴西拥有很多矿山的股份。这样,铁矿石涨价的影响很大一部分都可以由其对矿山的投资回报来弥补。
除了可以利用对矿山的投资来补偿钢铁制造成本上升所造成的损失以外,日本钢铁制造企业还通过合资、参股、战略联盟等形式进行全球布局,降低成本的同时,也分散了投资风险;而且,绕开了很多贸易壁垒,可以更直接、更充分地分享各国经济成长果实。
同时,为适应新的市场变化,日本调整了其钢材进出口结构:出口高档、高附加值钢材产品,进口低档和一般附加值产品。从表面上看,其出口数量下降了,进口数量增多了,但实际上出口价值金额、单价却在大幅增涨。
这样,日本企业既控制了钢铁产业链的上游,同时,通过产品升级、对外投资、战略联盟等手段,又控制了高端钢铁等高利润钢铁产品制造行业。因此,铁矿石等初级原料的涨价,可以达到压缩初级钢铁产品的利润空间的目的,将初级钢铁产品的利润进行转移,从而在打击对手的同时实现了自己的利润最大化。
日本钢铁行业环保技术发展情况
根据政府颁发的多项环保法规,日本钢铁业于1996年制订了“关于环保的志愿行动计划”,规定2010年比1990年耗能减少10%的目标。炼钢工序应采取的措施为:减少热损失、加强热回收的节能;推进渣和粉尘的3R以使填埋量最小化;利用其它产业的废物等。现已据此开展了工作,重点简介如下:
1.炼钢工序节能
通过混铁车的大型化、推广钢水包加盖作业、改善钢水包物流以缩短循环时间、应用钢水温度管理系统等在提高生产能力的同时并减少热损失。还利用低导热率的MgO-C砖、微孔绝热材料、使用中空骨料的低热容不定形耐火材料等以减少散热损失。在钢水包烘烤方面采用了蓄热式燃烧器以大幅降低燃耗等。
同时还进行了有关的技术开发,如附有感应加热装置的混铁炉,达到比电炉还高效的熔化废钢的水平;调整高炉、转炉、连铸间的能力差以提高炼钢工序的物流效率;在电炉工厂设钢水贮存装置,利用夜间低谷廉价电化钢,以便白天炼钢节电和大幅降低成本。在热回收方面,利用转炉煤气导管冷却水的低温余热和氨水的非等温蒸发、凝缩特性进行发电,发电效率比常规低温发电高40%以上,属世界首例。
2.钢渣利用
日本钢渣年发生量达1200万t,由于碱性高且成分不均匀,过去多作填埋处理。20世纪90年代前期的发生量和排出量均呈上升趋向,近10年来由于铁水预处理和厂内利用量的加大开始趋于下降。铁水预处理的发展是钢渣发生量下降的主要原因。钢渣的热利用除有效利用显热外,还可简化渣处理工序,如脱碳炉渣在不锈钢熔融还原炉的热利用。LF炉的还原渣在电炉热利用时,既可降低石灰单耗,又可提高电炉脱磷效率。但从整个社会的环保观点看,还应大力开发钢渣在水泥原料和土木建筑方面的用途。
3.粉尘利用
转炉首先应改进氧枪喷头和操作以减少粉尘的产生。在大规模再生利用技术方面,已开发成功环形炉和纵型炉。作为小规模利用法的DSM工艺系将电炉粉尘和还原渣用重油、氧气燃烧加热熔化为渣块作路基材利用,粉尘中的Zn、Pb等金属则作为二次粉尘回收后作原料利用。电炉粉尘亦可在真空下加热还原以回收ZnO,后将残渣氧化铁制成球团供电炉利用。在粉尘热利用方面,除横型热旋风炉可用于不锈钢熔融还原炉外,作为简易利用方法,可将电炉除尘器粉尘和铝渣、废油混合造粒后返回电炉利用,还有将粉尘从水冷喷头吹入炉内利用的方式。
4.废耐火材料
除用于生产耐火原料外,还有将MgO-C、MgO、白云石系的废耐火材料用于转炉、电炉、LF炉等代替生石灰、烧成白云石作造渣剂。此外,亦可作路基材利用。
5.其它产业的废物利用
过去,纸浆废料和铝渣均作为炼钢工序的保温材料和造渣剂利用。近年,新日铁广?厂转炉采用了部分废轮胎片代煤,连轮胎中的子午线钢丝亦得到有效利用,年用量达6万t以上。
公司案例:新日铁公司经营战略
1、技术领先战略 由于钢铁市场环境瞬息万变,新日铁通过改变经营方式,向公司内外明确提出了企业远景,制定了挑战技术革新、与社会和谐发展等4项企业理念,其中一项就是:向技术创造和技术革新挑战,技术上引领世界。
2、保证原材料长期稳定供应 由于全球原材料(特别是铁矿石、冶金煤、焦炭)市场供应紧张,为保证原材料的长期稳定供应,包括日本、韩国和印度在内的亚洲钢铁联合企业纷纷与海外的原料供应商签订长期供货合同,抑或出资收购矿山部分股份,抑或出资参与新矿山的开发。
2004年,新日铁与全球最大的铁矿石供应商CVRD签订了长达10年的供货协议。根据协议,新日铁每年可获得900万t的铁矿石供应。新日铁已与印度主要铁矿石出口商V.SDempo 公司和V.M.Salgaocar兄弟公司签订4~5年长期协议,协议规定从2家公司分别进口150万t和100万t铁矿石。而且有消息称,新日铁已购买里奥廷托集团位于昆士兰矿山8%的股权。2005年6月份,新日铁出资从美国金属及煤炭国际公司(AMCI)手中收购了澳大利亚两座冶金煤矿(CarboroughDowns煤矿和GlenniesCreek煤矿)5%的股份。根据协议,新日铁在今后10年内,可得到总量为1200万t的冶金煤。Carborough Downs煤矿为地下开采,预计2006年上半年投产,年产量150~200万t,将来年产量有望提高至400万t。而Glennies
Creek煤矿也为地下矿,1999年投产,目前年产量为170万t,几年后将增至280万t。新日铁和浦项双方还与加拿大EVCP(Elk Valley Coal Partnership)公司就Elkview煤矿的权益达成一致协议,协议包括新日铁和浦项将分别获得Elkview煤矿2.5%的股权,并参与该煤矿产能建设。
2005年3月,由新日铁率领的日本财团和美国投资基金WL-Ross&Co.LLc投标三井矿业公司。日本产业再生机构在三井矿业公司中占有52%的股份,为了重整三井矿业公司,计划出售已发行股票中的33%。由于三井矿业公司将于2006年春季重新启动北九州的一座焦炉,且与新日铁签署了为期10年的焦炭供应合同,因此日本财团在投标中占据优势。
3、加强企业问合作,提高市场竞争力
自从2003年4月JFE控股公司正式运营以来,日本钢铁业形成两强对立的竞争局面。为提高自身的竞争力,新日铁不断加强与住友金属和神户制钢之间的合作。2005年3月份,3方相互持股。根据协议,新日铁持有住友金属工业公司5.01%的股份,持有神户钢铁公司2.05%的股份;住友金属持有新日铁1.81%的股份,持有神户钢铁2.05%的股份;神户钢铁持有新日铁0.41%的股份,持有住友金属1.71%的股份。
2005年6月份,新日铁、住友金属和神户制钢3家公司进一步扩大合作,此次三方具体合作的主要内容是:①共同利用住友金属和歌山高炉设备;②新日铁和神户制钢分别向东亚联合钢铁公司(住金钢铁和歌山公司的控股公司)出资10%和2%的股份。东亚联合钢铁公司是住友金属、中国台湾中钢和住友集团的合资企业,成立于2003年7月,拥有位于日本西部的住友金属的和歌山钢厂。在完成对东亚联合钢铁公司的出资后,住友金属开始向新日铁供应板坯,2005年4~9月供应3万t,不久还将向神户钢铁供应。2009年,随着和歌山厂又一座高炉的扩建完成,供应新日铁和神户钢铁的板坯将翻一番,达到每年100万t。
为加强相互间的资金合作,新日铁在中山制钢公司的持股比例将从现在的1.3%提高到5%。同样,中山制钢公司也将提高在新日铁中的持股比例。而且,2004年底,两家公司宣布合资建立一家生产钢筋的公司。新公司的资本额为4.9亿日元,其中新日铁控股60%,中山制钢持股40%。新公司于2006年3月投产,月产钢材5.5万t。
为扩大销售,2005年新日铁与Blue Scope结成联盟,新日铁将利用BlueScope在建筑材料市场(主要在亚洲)上的加工设施和销售网络,加工、推销和销售其战略钢板Super Dyma(镀镁铝锌钢板)。
4、抢先变化,并为自觉变化而努力
为应对全球普通不锈钢产品的供应过剩,同时为满足造船、电机行业对高级不锈钢产品的需求增加,2005年新日铁•住金不锈钢公司投资24亿日元,扩大不锈钢中板产量。该公司决定于2006年7月将八幡厂不锈钢中板的年生产能力由10万t提高到13万t,并增加酸洗设备和质量检测生产线,主要是考虑适应中国和中东地区对LNG装置和造船方面日益兴旺的市场需求。
为应对需求坚挺而供不应求的汽车用钢材,2005年新日铁出资50亿日元收购三菱制钢在室兰厂生产特钢的电炉,该电炉月产特钢可达2万t。
截止到2005年5月中旬,新目铁君津钢厂厚板车间累计轧制量已达到5000万t。该厚板车间投产时间为1968年3月,虽然用了整整37年时间才达成这样的产量,但在日本所有厚板厂中还是第一家。君津钢厂厚板车间除生产造船用钢外,1983年新增设控制冷却设备(CLC),这为以后开发建设和桥梁、海洋结构、管线用钢以及产品批量生产发挥了很大的作用。目前,厚板市场需求旺盛,预计今后用户对高级钢产品的需求还将进一步提高。君津钢厂厚板工厂奋斗目标是:通过不断提高制造实力和劳动生产率,不管是通用产品还是高级钢产品都要满足用户多方面的需要,为建成全球第一的厚板工厂而努力。
随着2006年欧洲电子和汽车行业实施新的环保法规,预计不含6价铬的钢板需求将急剧增长。为此,2005年9月份,新日铁宣布计划从2006年3月31日起完全停止生产含铬电镀锌钢板。该产品主要应用于电子、办公设备和汽车行业。目前,新日铁每月生产6万t电镀锌板,但需要指出的是有80%以上的产品不含铬。
5、海外投资,稳定钢铁市场、扩大出口 新日铁和中国宝钢、欧盟阿赛洛等大钢厂在中国合资的汽车板项目已于2005年5月投产。对于该项目,宝钢拥有新公司50%股份,新日铁持股38%,阿赛洛集团拥有12%股份。新日铁约投资1000亿日元,年产冷轧板170万t,其中80万t为耐蚀性镀锌板;新日铁不仅和中国宝钢协作,还和国际上极具实力的大钢厂协作,以形成“强强联合”,如在欧洲,和世界最大的钢铁企业阿赛洛集团互相提供汽车板生产技术,并共同供应日欧汽车厂高质量汽车用板。
而且还与韩国浦项互相持股,共同开发钢铁技术.2005年,随着新日铁与浦项公司的合作期限即将到期,为进一步巩固在全球钢铁业中的牢固地位,双方根据近5年来的合作成果,在详细评估了双方合作内容的基础上,决定进一步延长战略合作协议,即合同执行时间从当初的5年延长到10年。通过在共同研究、技术交流、原料采购、海外投资和人才培养5个方面的进一步合作,以强化双方战略合作关系。
新日铁国际协作的内因在于维持钢铁市场平稳,如在亚洲,若新日铁和浦项、宝钢三大钢厂为扩大钢材销售而无序竞争时,势必造成互相杀价,无谓消耗;现在采取协作,尽量避免无谓竞争,属于“安全保障条件条约”。
2005年9月,新日铁商事决定在越南河内成立一家公司产能达4000t/m的钢材服务中心。该服务中心由新日铁商事持股90%,新日铁持股10%。9月将开工建设,该中心主要加工冷轧卷、硅钢和涂层板,将于2006年6月投入生产。该中心所需原料全部由日本的新日铁提供。2004年6月,新日铁商事下属的新日铁西贡卷材中心投入生产,该卷材中心位于越南南部的越南新加坡工业园,产能达1500t/m。
6、面对焦炭价格暴涨,努力扩大高炉喷煤量,降低成本 2005年,由于焦煤、焦炭价格暴涨,新日铁君津厂抓紧扩大高炉喷吹煤粉改造。该厂有3座高炉,年产钢达1000万t以上。为大力降低成本,首先以多使用价廉的高炉喷煤部分替代价格昂贵的焦炭,预计吨铁喷煤量可从2004年的120kg增加到2005年的160kg。君津厂对焦煤中掺废塑料炼焦十分重视,今年还拟将焦油用于塑料原料,既可降低成本,又有利于环保。
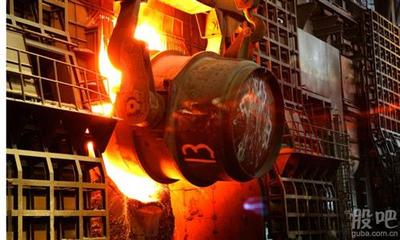
7、多元化经营。培养新的经济增长点 新日铁计划在千叶君津厂30万m2的空地上筹建购物中心,该购物中心总计有10万m2的营业面积,预计于2007年春天营业。这将是日本最大的购物中心之一。新日铁开始邀请相关公司成为购物中心的承租人。购物中心可停放5000辆车,可容纳超市、餐厅、影城和矿泉疗养地等一系列设施,以重新刺激君津地区的个人消费。
日本钢铁工业空间格局动态演化
日本钢铁工业空间分布基本态势的动态演化,可从大型钢铁联合企业的空间分布的变化观察到。大型钢铁联合企业的空间分布及其变化为:最初是以原料地指向型为主的八幡、釜石、室兰,进而在作为钢铁产品主要消费地(京浜、阪神、北九州)的工业地带内的尼崎、广田、小仓、船町、京浜,而第二次世界大战后则主要为大都市地域(包括京浜、阪神工业地区在内)及其周围地区的千叶、水岛、加古川、名古屋、界、君津、大分、吴和福山等地集中配置。
1973年石油危机以来,开始改变从前以规模经济为标志的大量生产体制,高能耗、低附加价值的钢铁工业发展势头骤减,钢铁厂家不再新增高炉,而转向缩减生产成本,提高产品质量与品种。八十年代以来,伴随着日元升值,国际竞争力下降,开始关闭工厂、削减人员,向钢铁以外的领域拓展。随着高炉工厂的关闭、合并等,钢铁工业越发体现出在空间上集中于大城市圈及其周围地区。大型钢铁联合企业一般是属于利用大型专用船舶运进煤炭、铁矿石等原料,在具有水深15m以上接岸条件的填海造地上配置的临海工厂,即大多都是位于距旧海岸线1~2km处的地域。
日本钢铁工业发展与空间格局演化机制分析
1 、产业结构转化等所引起的钢铁工业竞争条件的变化
日本钢铁工业发展主要取决于钢铁工业竞争条件。钢铁工业竞争条件在很大程度上受产业结构状况的影响。日本经济高度增长以来,产业结构出现了明显的重化学工业化。从1955年到1970年,日本重化学工业企业数、从业人员数以及产值占整个工业的比重分别从18.6%、37.4%、44.6%增加到占28.4%、49.6%、62.3%。其中机械工业增长极为迅速,上述比重从分别占8.7%、18.5%、14.7%增加到占14.8%、31.2%、32.4%。机械工业是钢铁工业产品主要耗用部门,机械工业的急速发展促进了对钢铁工业产品的需求,从而有利于钢铁工业竞争条件的改善,加速了钢铁工业的发展。但进入70年代以来,以下环境条件的变化引起日本钢铁工业竞争条件发生变化,导致钢铁工业发展减缓乃至停滞:第一为工业发展的重点从以大型装置型产业转向高级组装型产业,产业结构向轻型化方向进展。第二为随着日元升值,劳动力成本上升,装置型产业向新兴工业化国家与地区转移扩散。例如韩国粗钢产量从1976年的351.1万t,增加到 1994年的 3 374.5万t,连铸比达97.8%,超过日本两个百分点,其中,浦项综合制铁粗钢产量已接近日本最大钢铁企业新日本制铁。这样,韩国等新兴工业化国家的大型装置型产业的发展,致使日本该产业的竞争性减弱,出口减少,进口增加。出口减少致使有效需求减少,限制了生产的发展。第三为国内制造业钢铁产品需求市场的缩小,致使生产萎缩。一方面由于许多国内制造业向海外转移,国内“空洞化”现象普遍,另一方面,国内制造业的结构转化也使得大量消耗钢铁工业产品的产业如造船等规模缩小,这些大大地加剧了国内钢铁市场的萎缩。
2 、市场地域结构以及钢铁企业市场分割战略变化
日本钢铁工业空间格局的演化则是由大型钢铁联合企业为竞争国内市场所实施的市场分割战略的结果。日本钢铁工业制品的80%左右以国内市场为销售对象。在地域上主要在从关东到北九州之间的太平洋地带,关东与关西各占半壁江山,各主要钢铁工业企业为了有效分割日本国内市场,均采取了东西基地的布局形式。后随国内市场态势的变化,工业产品的销售地域开始逐步从关西转为关东。钢铁工业产品的有效需求地域,也随着金属、机械工业配置的变化(集中于关东地区以及中京地区)和人口向三大都市圈集中而伴随的建筑业用钢铁产品的需求地域重点向东部转移,最大的钢铁消费地域(东日本)成了日本钢铁工业新设、改扩建、或保留高炉的重点地域。相反,关西地区尤其是北九州地区,以及北海道地区的高炉成为大型钢铁联合企业关闭的对象或预选者。另外,钢铁工业空间格局的演化还受到处于不同区位以及不同时期建设的钢铁企业在生产技术水平以及能否适应钢铁产品结构高级化发展方面的影响。1995年末全日本共有高炉42座,其中运转高炉30座,运转率为71.4%,但在高炉容量4000m3以上的大型高炉 17座中,有 15座运转,运转率为 88.2%。大型高炉一般是六十年代以来建设,且布局在临海的大城市及其周边地区,而其他地区的较小型高炉较易成为钢铁企业关闭的对象。另一方面,日本钢铁工业产品结构不断升级,粗钢中特殊钢、钢材中特殊钢钢材的比重不断增加,1965年特殊钢占粗钢的9.2%,而1980年则占15.2%,1995年更占18.9%。相对较新的钢铁企业由于设备新,又多位于大城市周边,容易得到获取高水平的技术人员以及高技能的劳动力,将在竞争中处于相对领先地位,从而对钢铁工业空间格局的演化产生作用。
3 、原、燃料等生产要素组织与供给的变化
近代日本钢铁工业建立初期,是以依据于自身的原料、燃料供应为前提的。日本的第一座洋式高炉在釜石铁矿成立是因为釜石铁矿具有铁矿石、燃料木炭、粘土原料、石材以及作为水车动力源的水力条件等方面的优越条件。作为现代钢铁工业成立标志的八幡制铁所,为原、燃料运输方便,选择八幡村的临海区域配置工厂区,使日本钢铁工业企业开始了从内陆铁山转为临海配置。其后1907年在北海道的输西(室兰),建起了以北海道石狩煤田的炼焦煤为依托的另一原料地指向的大型钢铁工业企业。在本世纪初期(日本明治、大正年代)的钢铁工业是明显的原料地(燃料地)指向,代表的制铁所有八幡,釜石和室兰。
从1930年开始到1945年,日本军国主义政治下的军事工业发展对钢铁需求的增加,相继在作为钢铁产品主要消费地的阪神、京浜等工业区域内建设新的钢铁联合企业,是因为当时的日本钢铁工业开始利用国外主要是亚洲地域的原料及燃料,港口区位是运费最小的区位。第二次世界大战后钢铁需求以及国外原料来源都发生了很大变化,进一步加强了使钢铁工业企业在位于临近工业区域中的主要消费市场区域集中。铁矿石、炼焦煤的国外依存日益增强,铁矿石与炼焦煤的海外依存度都达到了近100%,进口原、燃料的来源发生较大变化,开始主要依赖澳大利亚、巴西、加拿大、美国等澳洲、美洲国家,这导致日本钢铁工业企业呈现典型的临海区域集中配置。
4、工业基础条件状况的影响
钢铁工业是典型的装置型产业,特别是大型的钢铁联合企业,用地面积大,用水多,因此用地、用水等工业基础条件也在一定程度上决定钢铁联合企业的微观配置。日本是多山的国家,人口密度大,地形复杂,因此适合大型钢铁联合企业的用地保证在一定程度上影响钢铁工业的空间配置。因此,考虑到铁矿石与炼焦煤运输便利等,在临海利用填海造地等接岸地域配置了大型钢铁联合企业,住友金属鹿岛制铁所就是一座在临海利用填海造地配置大型钢铁联合企业的代表例子。鹿岛地区是茨城县综合开发振兴计划(大纲)中的鹿岛滩沿岸地域综合开发计划——临海工业地带造成计划的指定地域,同时以能够提供广阔的用地与丰富的用水,以及通过公共投资先行进行了港口建设,加之距重要工业地区(消费地)的京浜地区仅 80 km的地理位置优势,因此使得住友金属工业决定在鹿岛建设大型钢铁联合企业。
5、产业政策与地域政策的影响
日本钢铁工业发展受产业政策、地域政策的影响。在本世纪 20年代后期(日本昭和年代),为适应日本军国主义扩充军备的需要,产业政策向包括钢铁工业在内的军事工业倾斜,从而使钢铁工业有了急速发展。“二战”结束时日本钢铁工业几近瘫痪,然而,战后由于导入向钢铁工业在内的重化学工业倾斜的生产方式以及由于朝鲜战争引起钢铁产品等的需求增加,日本钢铁工业奇迹性地实现了复兴。进入高度经济增长期后,以“设备投资带来设备投资”这样的生产资料生产部门的“内部循环”式发展的产业政策下,产生了国内庞大的生产用机械需求以及个人收入增多带来的作为个人耐用消费品的机械(家庭用小汽车等)的需求等,都带来了国内对钢铁工业产品的需求快速增长,拉动钢铁工业的发展。然而由于受两次石油危机以及进入八十年代以来的日币升值的影响,日本产业结构政策向高附加价值的高加工度产业倾斜,同其他原材料工业一样,钢铁工业出现了停滞与衰退,销售额以及付加价值额在制造业中的比重急剧下降。
地域政策对钢铁企业在用地取得、供水、交通等方面影响很大。象水岛、鹿岛分别是新产业都市和工业整备特别地区指定地域,在用地取得上得到了诸多政策上的优遇,可以取得需要的广阔用地,因此均成为日本最大钢铁联合企业的配置地域。
综上所述,日本钢铁工业发展与空间格局演化的拉动力是钢铁市场需求。钢铁工业发展,是钢铁工业企业适应外界环境条件变化的结果,大型钢铁联合企业为维持竞争优势以及实施市场分割战略引起钢铁工业空间格局演化。日本钢铁工业发展与空间格局演化的推动力首先是钢铁工业竞争条件和原、燃料等生产要素组织与供给状况,前者受产业结构、相关产业发展及变化。后者受技术进步的深刻影响。其次是企业的市场分割战略以及工业基础条件状况。前者受市场地域结构发展及变化、后者受技术进步的深刻影响。同时产业政策、地域政策在程度不同地影响着钢铁工业的发展与空间格局演化。
早在1901年,日本就建立了拥有炼铁、炼钢和轧钢等完整工序的钢铁联合企业。第二次世界大战后,日本政府对钢铁工业实施倾斜政策,使日本钢铁工业在1950-1967年间得到迅速发展。1973年日本钢产量达到1亿吨。1993-1995年,日本一直是世界第一大产钢国。日本钢铁工业与其他工业一样,直接受日本经济产业省(原通商产业省)管辖,具体部门为下属制造产业局,有关钢铁工业的政策则由经济产业省通商政策局负责制定。制造产业局负责管辖钢铁工业、有色金属工业和化学工业等基础材料工业,并推动这些工业的健全发展。制造产业局下设的钢铁科负责有关钢铁工业的具体事项。通商政策局负责全面推动有关企业制度的改革、规章制度精简和经济结构改革,在努力创造新的产业领域、具有国际吸引力的新事业和投资环境的同时,全面规划和提出宏观经济政策。
“二战”后为了振兴日本工业,日本政府还采取了向煤炭工业倾斜的政策。煤炭工业在其后的发展过程,由于日本国内优质煤炭较少或开采成本过高,因此逐步消亡,目前只剩下有限的几个政策性保护煤矿。而日本钢铁工业则受惠于政府的倾斜政策,得到了迅速发展。
1958年,在通产省的行政指导下,日本实施了主要钢生产管制,并与钢铁企业一起为稳定市场实施了公开销售制度。此外,面对20世纪60年代初的结构性经济箫条,日本通商产业省产业结构审议会特殊钢分会于1960年向特殊钢行业提出了关于行业体制整顿、企业合并和实现什么集中的“劝告”。日本政府也于1962年颁布了《特殊钢业的合理化对策》。该“对策”提出了诸如提高生产率与质量、强化企业基础实力和综合能力、构筑廉价且稳定地获得优质原材料的体制、改善流通、整理与统一有关特殊钢的标准和确立出口体制等基本方向。“对策”对特殊钢行业必须实现的具体目标提出了建议,从而使日本特殊钢行业度过了难关。
1977年,日本通商产业省产业结构审议会钢钢部设置了平、电炉设备分会。1983年,该委员会指导钢铁行业在1987年以前自主处理了相当于380万吨生产能力的设备,以实现市场的供需平衡。一次为契机,日本钢铁业还相继出现了一些资产重组和企业合并。
总之,日本钢铁工业的发展与日本政府及其所制定的政策有着极其密切的关系。其特点是,第一,政策主要围绕有关国计民生的大型钢铁联合企业来制定,兼顾其他中小型钢铁企业。政府对中小企业采取行动时以《中小企业法》为准绳来实施。第二,在处理政府与企业关系中有一个中立的公正交易委员会。它既不代表公司或企业,起到缓冲、监督和促进对话的作用。第三,针对不同的行业采取不同的政策。例如,在1971年进行钢铁行业改革时,日本政府不同意干预行业减产措施,而主张结成行业协调组织由行业自身进行协调。而1976造船业不景气时,政府则主张造船业采取减产措施。第四,政府反应及时,判断准确,落实彻底,效果也比较显著。例如,1974年日本通产省“钢铁、化工行业一年只批准一项设备投资的决定,并得到首相认同”的措施等,得到很好的贯彻。第五,日本钢铁公司或企业清楚地认识到自己所处的地位和利害关系,因此愿意配合政府解决存在的问题。所结成的企业间协调联合体充分发挥了应起的作用。之所以列出从1970年以来日本政府及其机构与日本钢铁工业的各种联系,是因为1973年日本的钢产量创历史最高纪录。在此之前,日本钢铁工业存在需要加以整顿的各种迹象。
近几年,日本政府对钢铁行业的干预减少,这是因为钢铁工业内部已形成了对付各种来自外部和内部已形成的机制,能自发和主动地采取措施。最近对日本钢铁行业一个中国的政策支持是,在会计制度上承认“单独结算”和“合并结算”,为日本钢铁企业的进一步发展打下了基础。
日本钢铁工业用耐火材料的现状
日本钢铁工业用耐火材料,如炼铁,铁水预处理,转炉,盛钢桶,中间包和连铸用耐火材料,开发使用了各种优质,高效,环保型耐火材料,大幅度提高了使用寿命和降低了耐火材料单耗。如高炉主出铁沟耐火材料单耗降低了15%;泡泥单耗降低了12%;铁水预处理专用炉的寿命达到了8000—13000炉次;转炉使用寿命稳定在8000—9000炉次;盛钢桶使用寿命提高到原业的4—5倍;中间包使用寿命最高达到2000次以上;连铸用长水口使用寿命达到了30次和40次。
日本经济在这10年间非常不景气,钢铁行业为了加强国际竞争力和增加收益,生产体制采取合并,系列化等集约管理,合理配置人员,推进了经济合理的操作。另外,加速了向高级钢和特种钢的转变。
耐火材料行业为了适应钢铁工业用户的需求,在提高耐火材料的耐用性,可靠性,可作业性的同时,大幅度地降低了生产成本。另外,积极进行环保型耐火材料的开发。
日本高强不锈钢现状与发展方向
日本已开发了能满足用户要求的具有优良耐热性、耐蚀性等特性的新型不锈钢,并且大多数钢种已在各个领域得以应用。高强度不锈钢就是其中之一。
《日本工业标准》中较早规定通用型高强度不锈钢,随着用户对电子机械相关材料需求的多样化,这类通用型不锈钢已无法充分满足要求。因此,进一步提高不锈钢强度,抑制其加工性和韧性的下降,避免高强度材料通常存在的疲劳特性变差,是日本正在积极研究的主要课题。
不锈钢的强化手段,有加工强化、析出强化、晶粒细化强化、固溶强化和相变强化等。日本冶金专家认为,要使不锈钢达到一定的强度,同时改善其他特性,必须综合应用上述强化手段和采用现代化的加工处理技术。
避免不锈钢韧性和疲劳特性下降的有效方法之一,是减少钢中的氧、硫等非金属杂质。在以无磁性作为重要特点的高强度纯奥氏体不锈钢中,这些杂质是产生凝固裂纹和热轧表面缺陷的原因之一。为了最大限度地减少不锈钢γ晶界处的硫化物,应进一步提高高纯度化精炼技术水平,以实现钢质的超低硫化。另外,析出物和析出形态对改善高强度不锈钢 的韧性也至关重要,应采用化学计算法控制析出物以抑制韧性下降,这也需要提高钢液精炼技术水平。
为了解决平整冷轧材的加工性和韧性差的问题,日本专家在调整γ 相稳定性的同时,不使钛和铌等形成粗大的碳氮化合物,开发了利用添加硅、铜或硅、钼产生形变硬化和时效硬化的新型不锈钢,并已作为薄壁型用高强度材料投入实用。针对有关平整冷轧材存在一焊接就软化的缺点,日本专家将M相进行逆相相变处理,获得的超细晶粒(平均晶粒直径为0.5微米)双相钢在焊接时不软化,从而开发了强度为1000N/mm2、延伸率为20%的高强度不锈钢。此外,日本专家还开发了具有较高强度、良好加工性以及有磁性的多相钢(平均晶粒直径为5微米)。这种不锈钢主要用作软盘芯材。
日本高强度不锈钢今后的发展方向是:将材料研究和精炼技术研究相结合,达到强度与加工性、韧性的更高层次的平衡,同时降低制造成本,注重环境保护,以开发出性能更优异的新材料。
日本钢铁工业企业情况
日本钢铁工业曾经是日本经济最重要的支柱产业之一。早在1901年日本就建立了拥有炼铁、炼钢和轧钢的钢铁联合企业,第二次世界大战后,日本政府对钢铁工业实施倾斜政策,使日本钢铁工业在1951-1967年期间得到迅速发展,1973年钢产量即已达到一亿吨水平,从1993-1995年日本一直是世界第一大产钢国,从1996年起,中国成为世界第一大产钢国, 2003年日本粗钢产量为11051.4万吨,位居世界第二位。
日本钢铁行业现有公司和企业共约400余家,这些公司和企业大致可分为三类:
1.大型钢铁联合企业。其中包括被称为五大钢铁联合企业的新日本制铁公司、JFE、住友金属工业公司、神户制钢公司和日新制钢公司等。这些公司形成了日本钢铁工业的核心。
2.独立或相对独立的钢铁联合企业,如东京制铁公司等。有一部分从属于大集团,如山阳特殊制钢公司等。
3.小型专业生产企业。一般只生产或加工单一产品。第二类和第三类公司或企业在原料和销售方面对大型钢铁公司有着一定的依赖关系,并保持着千丝万缕的联系。
日本钢铁业不断采纳和应用世界最新技术,同时对将来有可能应用的新技术不间断地进行着开发与研究,比如目前普遍采用的技术有烧结炉的排烟脱硫技术、焦炉采用CDQ、高炉炉顶压差发电(TRT)、高炉喷煤、废钢预热、各种钢包精炼技术、薄板坯连铸技术、热轧无头轧制技术、交叉辊轧制技术等,使其无论在技术上、产品质量上以及生产效率等方面均处于世界领先地位。
日本政府机构与钢铁工业的关系
钢铁工业与其他工业一样直接受经济产业省(原通商产业省)这一政府部门管辖,具体窗口是下属的制造产业局(原基础产业局),有关钢铁工业的政策则由通商政策局负责制定。
制造产业局:管辖钢铁工业、有色金属工业和化学工业等基础材料工业,并推动这些工业的健全发展。下设钢铁科负责有关钢铁工业的具体事项。
通商政策局:全面推动有关企业制度的改革、精简规章制度和经济结构改革。在努力创造出新的产业领域和有国际吸引力的新事业和投资环境的同时,全面计划和提出宏观经济政策。
二战以后为了振兴日本工业,日本政府在宏观政策上采取了向钢铁工业和煤炭工业倾斜的政策。煤炭工业在其后的发展过程中,由于日本国内优质煤炭较少或开采成本过高,因此逐步消亡。目前只剩下有限的几个政策性保护煤矿。而钢铁工业则受惠于政府的倾斜政策,得到了迅速发展。
1958年在通产省的行政指导下实施了主要钢材生产管制,并与钢铁界一起为稳定市场实施了“公开销售制度”。面对六十年代初的结构性经济萧条,“通商产业省产业结构审议会特殊钢小委员会”于1960年向特殊钢行业提出了关于行业体制整顿、企业合并和实现生产集中的“劝告”。政府也于1962年颁布了《特殊钢业的合理化对策》。如前所述该“对策”中提出了诸如提高生产率与提高质量,强化企业基础实力,强化企业集团的综合能力,构筑廉价且稳定地获得优质原材料的体制,改善流通,整理与统一有关特殊钢的标准和确立出口体制等基本方向。对特殊钢行业必须实现的具体目标提出了建议,从而使特殊钢行业渡过了难关。
1977年“通商产业省产业结构审议会铁钢部会”中设置了“平电炉设备小委员会”,1983年该委员会指导钢铁行业至 1987年自主处理了相当于380万吨能力的设备,以实现产品市场的供需平衡。以此为契机相继发生了一些追求经济性的资产重组或一些公司、企业的合并。
日本钢铁联盟在钢铁工业中的作用
日本钢铁联盟是一个社团法人。它由经营炼铁、炼钢、轧制及其他与钢铁有关的64家公司(企业)、68家商社和6个团体为会员组成。其从事的事业以追求钢铁行业的健全发展和为日本的经济增长和提高人民生活水平做出贡献为目的。它的政府对口单位是经济产业省制造产业局钢铁科。
钢铁联盟所从事的工作范围如下:
1.进行与推进钢铁生产、流通、贸易及消费有关的调查研究;2.促进和加强钢铁技术开发及推广;3.进行与钢铁行业环境、安全有关的调查研究和措施实施工作;4.与钢铁行业劳动及经营的改进和合理化有关的调查研究;5.推进与钢铁有关的标准化工作;6.推进有关钢铁交易合理化的工作;7.推进有关振兴钢铁贸易有关的政策实施;8.收集及提供与钢铁有关的信息;9.向政府及有关机构表明、申述与钢铁行业有关的意见,答复一些问题。10.除上例以外,还有其它为实现本联盟目的所必要的事业。
伴随日本行政机构的改革进程和各行业结构改革以及大型钢铁企业内部改革的不断深入,日本钢铁联盟也从1994年左右开始着手进行改革,并于1997年初基本完成。
此改革主要围绕以下三个内容进行:1.对各委员会和事务局的设置进行分析研究,并进行重新设置。其直接结果是原38个委员会减少至18个委员会;2.新设置标准化中心;3.修订人事和分配制度。
钢铁工业在日本经济中起着举足轻重的作用。从钢铁联盟(和钢铁协会)的办公地点设在日本经团联(经济团体联合会,日本最重要的经济组织)会馆就可见一斑。经团联的会长 (董事长)长期由钢铁界人士担任,除九十年代有一段时间由其他行业(松下电器公司、丰田汽车公司)担任外,最近又由新日铁公司董事长担任会长。因此钢铁行业的意见一直对政界有着重要影响。
钢铁联盟对日本钢铁工业发展所起的作用是很大的。对于钢铁行业内公司、企业间关系的协调,钢铁产品进出口的协调,新设备的研制、新技术的开发,钢铁标准的制修订和国际接轨,钢铁统计,国际合作等方方面面钢铁联盟都发挥了巨大的作用。特别是在钢铁行业的历次结构改革中其作用不可小看。
为了让日本政府采取的经济措施和补充财政预算更合理地实施,钢铁联盟代表钢铁界于2000年向“经团联”提出了74项废除不合理法律、法规和规定的意见和建议,2001年除去已解决的项目后又提出了31项意见和建议。
1.在钢铁工业的结构改革中,政府根据市场和行业情况及时予以指导,钢铁联盟协调各专业行业协会及时采取措施。
2.专业行业协会有很强的行业自律作用。重行业利益,并无地方利益的影响。
3.各大钢铁公司有相对的独立性。尽管动作有快有慢,但措施都很坚决和果断。并有着全行业共存亡的决心。
4.钢铁联合企业在钢铁工业中仍保持绝对的优势和相应的竞争力。与此同时适当地发展了短流程工艺。在此过程中政府没有进行过多的干预。
5.在发展多种经营时,充分认识到必须在与钢铁工业所采用的先进技术相关的领域发展,因此发展得最快的是工程项目领域。
6.日本钢铁公司与其他日本公司在国外实施项目中所采取的立场一样,相互协调不互相拆台,也避免相互撞车。
7.日本钢铁工业结构改革所需费用全部是由民间(企业)负担的,政府没有直接出一分钱。但是在政策上给予了必要的支持,特别是在融资方面。
日本钢铁行业的环境保护
上世纪60至70年代日本工业迅速发展,其成就令世人瞩目。钢铁工业的生产在1973年也达到顶峰,粗钢产量创历史最高纪录。然而这个时期也正是日本环境污染最严重的时候,其中最典型的事例是由于公害引起的“四大公害诉讼”。此即由于工厂废水中的有机水银引起的熊本县水俣病案诉讼,新泻县水俣病案诉讼;由于工厂废水中的Cd引起的“痛痛病”案诉讼和四日市哮喘案诉讼等。引起了日本举国上下的关心和注目,日本政府也及时采取了相应的措施。
现在世界各国人们到日本访问时很难将眼前的优美环境与30年前的情景相联系,但这是的的确确发生过的事实,已足以使发展中国家引以为戒。
这样巨大的变化使人们对日本环境保护的法律、法规、措施、技术等产生极大的兴趣。在此仅就日本钢铁行业的环境保护情况作一粗略介绍。
(一)环境保护相关政策
日本有关环境保护的法律制定、体制确立及其发展经历了如下几个阶段:
1.法律、法规创立期(上世纪50年代至60年代后半期):日本第一个有关环境保护的条例是1949年东京都制定的东京都防止公害条例。其后国家在1958年制定了“公共水域水质保护法”、“工厂废水排放管理法”,1962年制定了“工厂废气排放管理法”,1967年制定了“公害对策基本法”,随后陆续制定了“大气污染防止法”(1968年)、“噪音管制法”(1968年)、“对公害造成的健康损害进行补偿的特别法”(1969年)和“公害纠纷处理法”(1970年)。
2.体系确立期(1970年前后):1970年日本国会审议并批准了14个有关环境保护的法律。该次国会在日本被称之为“公害国会”。这些法律有:“公害基本对策法”(部分修订)、“道路交通法”(部分修订)、“噪音管制法”(部分修订)、“废弃物的处理及清扫法”(旧“清扫法”全部修订)、“下水道法”(部分修订)、“事业主负担防止公害事业费法”、“海洋污染防止法”、“农药管制法”(部分修订)、“有关人体健康的公害犯罪处罚法”、“农用土地土壤污染防止法”、“水质污染防止法”(已有的有关水质的二个法废止)、“大气污染防止法”(部分修订)、“自然公园法”(部分修订)、“有毒物及有害物管制法”(部分修订)。
3.调整期(70年代至80年代后半期):1971年成立了环境厅,对环境保护进行一元化的领导。在这期间实现了无过失损害赔偿责任的法制化(对“大气污染防止法”和“水质污染防止法”进行部分修订);设定了比美国严格约七倍的N02环境基准;制定了“公害健康损害补偿法”(是对由于公害而致使健康受到损害者的行政制度上的救济);对NOx固定发生源规定开始(第一次,至1983年为第四次);制定“环境保护长期计划”。
4.第二次创立期(80年代后半期至今):在该期对SOx排放总量进行了规定,对NOx排放量进行了第三次、第四次强化修正,在与水质有关方面引入了COD总量规定。在此期间废止了“公害对策基本法”,制定了“环境基本法”。
(二)相关组织
日本钢铁联盟是以主要钢铁公司为会员的公益法人,通过下属由会员企业人员组成的各执行委员会推动环境保护事业。先后成立了“工厂废水委员会”(1958年),“工厂环境公害委员会”(1967年,现更名为“工厂”),“钢铁行业NOx防除技术开发本部执行委员会”(1973年),“钢铁渣资源化委员会” (1973年,目前已取消)。于1989年成立了“地球环境问题对策委员会”。
日本钢铁产品进出口结构持续优化
日本是亚洲地区和世界上最大的钢材生产国和出口国之一,其主要出口市场是中国等亚洲国家。随着最近几年中国和韩国等亚洲国家的钢铁工业的发展,亚洲钢铁市场的供求状况开始发生变化。为适应这一市场变化,日本对其钢材进出口结构进行了调整:出口高档、高附加值钢材产品,进口低档和一般附加值产品。从表面上看,其出口数量下降了,进口数量增多了,但实际上出口价值金额、单价大幅增长。
日本在减少对亚洲一般钢材出口的同时,大量增加高档钢材出口量。以汽车用高档钢板为例,日本对韩国和中国的汽车用高级钢板出口量已分别占中、韩国两国进口量的40%以上,对泰国、马来西亚的出口量占泰、马两国进口总量的60%多。但以吨数为标准,日本钢材出口量则自去年以来呈现下降现象。日本钢铁企业经过2000年~2002年的结构调整后,产品结构优化以及产品向高档化、高附加值化发展已经取得了明显成效。同时,日本特殊性能钢材的出口量也在大增。如日本产刀具用钢占国际市场份额的50%多,日本产汽车发动机内用特殊钢、油箱用特殊防腐蚀钢、尾气排放管用特种钢等市场的占有率分别达76%、83%和89%,几乎处于垄断地位。为了降低铁矿石、煤炭和钢铁生产辅料的消耗,减少大气污染,日本钢铁企业在扩大高档、高附加值钢材产量和出口量的同时,扩大一般钢材、低附加值钢材的进口量,将它们用作高级钢材的生产再加工材料,从高低附加值差价、能源和原材料消耗下降、环保效益增加等中获得收益和利润。
日本钢铁企业进行企业结构和产品结构调整后,日本国内的一般钢材产品出现供不应求现象,进口量明显增加。如今年年初,因汽车用一般钢板供货量不足,丰田要自宝钢进口;日产、本田也不得不压产或停产几天,并要求韩国钢铁企业紧急支援车用钢板。2002年,日本自韩国进口钢材194.6万吨,2004年增加为235.9万吨。亚洲国家中,中、韩两国是日本进口钢材的主要供货国。2005年1月份,日本总计进口钢材78万吨,其中自亚洲的进口量为64万多吨,同比分别增长44%和55%,从中国的进口量为27.8万吨,从韩国的进口量接近30万吨;而从欧盟和美国的进口量分别仅为1.4万吨和2600吨。
日本2005年进口增加较多的钢材品种主要是建筑用钢材、汽车用冷轧钢板、家电用钢板、镀锌钢板和彩涂板等产品。韩国东部制钢对日本的这类钢材出口量由2002年的2.8万吨扩大为去年的10.8万吨;联合钢铁的出口量由2.6万吨增加为5.8万吨。其中,彩板的出口量由3300吨增加为2.1万吨。
日本钢铁产品进出口结构的变化会进一步深化:出口高档产品的比重将大大增加,同时,一般钢材的进口量继续扩大。