《机械制造技术基础》是2010年3月1日化学工业出版社出版的图书,作者是林艳华。本原机械制造专业的三门主课(金属切削原理及刀具、金属切削机床及机械制造工艺学)中的基本内容,加以提炼、充实和更新,在1996年编写成的《机械制造技术基础》内部教材。该教材适于54学时,曾试用过三届,效果良好,基本上满足了新的教学要求;但也发现了一些不足之处。本书内容对从事机械设计、机械加工、加工控制及有关工程管理的技术人员来说,都是必不可少的知识。
机械制造技术_机械制造技术基础 -图书信息
・书名:机械制造技术基础
作者:林艳华出版社:化学工业出版社
出版时间:2010-3-1
ISBN:9787122076342
机械制造技术基础
开本:16开
定价:25.00元
机械制造技术_机械制造技术基础 -书籍信息
作者:杨宗德 主编
ISBN:10位[7118045225] 13位[9787118045222]
出版社:国防工业出版社
出版日期:2006-8-1
定价:¥35.00 元
机械制造技术_机械制造技术基础 -内容简介
本原机械制造专业的三门主课(金属切削原理及刀具、金属切削机床及机械制造工艺学)中的基本内容,加以提炼、充实和更新,在1996年编写成的《机械制造技术基础》内部教材。该教材适于54学时,曾试用过三届,效果良好,基本上满足了新的教学要求;但也发现了一些不足之处。为此,我们针对教学中所发现的问题,对原内部教材作了较大范围的改写,遂编成了此正式出版的《机械制造技术基础》一书。
本书内容的取材,侧重机械制造方面的基本知识、基本原理和基本方法。包括金属切削过程的物理现象及其规律,切削刀具的功用、性能和常用加工设备的传动、构造,以及有关加工质量、工艺装备、工艺规程等方面的必备知识。此外,还辟有单独一章,专门讲述现代制造技术的基础内容――数控加工及其编程等问题。本书内容对从事机械设计、机械加工、加工控制及有关工程管理的技术人员来说,都是必不可少的知识。
机械制造技术_机械制造技术基础 -目录
《机械制造技术基础》
第一篇金属切削基础知识绪论
第一章金属切削过程的基础知识
1.1基本定义
1.1.1切削运动与切削用量
1.1.2刀具切削部分的基本定义
1.1.3刀具角度的换算
1.1.4刀具工作角度
1.1.5切削层参数与切削形式
1.2刀具材料
1.2.1刀具材料应具备的性能
1.2.2常用的刀具材料
1.2.3其它刀具材料
本章小结
思考题与练习题
第二章金属切削过程的基本规律及其应用
2.1金属切削过程的基本规律
2.1.1切削变形
2.1.2切削力
2.1.3切削热与切削温度
.2.1.4刀具磨损与刀具使用寿命
2.2金属切削过程基本规律的应用
2.2.1工件材料的切削加工性
2.2.2切削液
2.2.3刀具几何参数的合理选择
2.2.4切削用量的合理选择
2.3目前金属切削发展的几个前沿方向
2.3.1高速高效切削
2.3.2绿色切削
2.3.3微细切削
本章小结
思考题与练习题
第二篇零件加工工艺与装备
第三章零件加工工艺的基本概念与知识
3.1零件机械加工的目标与内容
3.2机械加工工艺基本概念
3.2.1生产过程
3.2.2工艺过程
3.2.3生产纲领与生产类型
3.3工件定位原理
3.3.1六点定位原理
3.3.2定位方式和定位元件
3.3.3定位符号及其标注
3.4定位基准的选择与定位误差的计算
3.4.1基准的分类
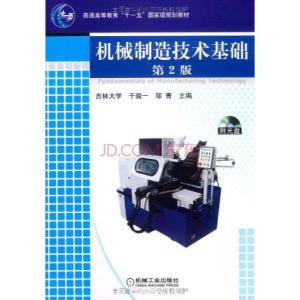
3.4.2定位基准的选择
3.4.3定位误差及计算
3.4.4定位误差的组成
3.4.5各种定位方法的定位误差计算
3.5工件的夹紧
3.5.1夹紧力的方向
3.5.2夹紧力的作用点
3.5.3夹紧力的大小
3.6工件的装夹与获得加工精度的方法
3.6.1工件装夹方式
3.6.2零件获得尺寸精度的方法
3.6.3零件获得形状精度的方法
3.7机床运动分析
3.7.1机床的分类
3.7.2机床的型号编制
3.7.3机床的主要技术参数
3.7.4机床运动分析
3.8零件工艺规程制订的基本原则与步骤
3.8.1工艺规程及其应用
3.8.2机加工零件的结构工艺性
3.8.3加工阶段的划分
3.8.4工序的划分
3.8.5工序的安排
3.9加工余量、工艺尺寸链、经济加工精度
3.9.1加工余量的概念
3.9.2影响加工余量的因素
3.9.3确定加工余量的方法
3.9.4工艺尺寸链
3.9.5经济加工精度
本章小结
思考题与练习题
第四章回转体零件加工工艺与装备
4.1车削加工方法
4.1.1车削概要
4.1.2车床的主要技术参数与类型
4.1.3车刀结构与材料
4.1.4车床用夹具与附件
4.2磨削加工方法
4.2.1外圆磨床
4.2.2无心外圆磨床
4.2.3内圆磨床
4.3孔加工机床与刀具
4.3.1钻床
4.3.2镗床
4.3.3孔加工刀具
4.4回转体的加工工艺案例分析
4.4.1数控车床加工的典型零件
4.4.2复杂形状的零件加工
4.4.3ca6140型车床主轴加工工艺分析
本章小结
思考题与练习题
第五章非回转体零件加工工艺与装备
5.1铣削加工
5.1.1铣削加工方法概述
5.1.2铣削参数和铣削方式
5.1.3铣刀的类型及用途
5.1.4铣刀角度
5.1.5铣床的类型及用途
5.2刨削和插削加工
5.2.1刨削加工方法概述
5.2.2插削加工方法概述
5.2.3刨刀与插刀
5.2.4刨床与插床
5.3拉削加工
5.3.1拉削加工方法概述
5.3.2拉刀
5.3.3拉床
5.4磨削加工
5.4.1平面磨削
5.4.2成形磨削
5.4.3非回转表面加工用磨床
5.5非回转表面加工中工件的装夹
5.5.1非回转表面加工用夹具的结构
5.5.2加工非回转表面时工件的安装
5.5.3铣床夹具特点及设计要点
5.5.4非回转体在磨床上的装夹
5.6非回转表面加工分析与工艺应用
5.6.1非回转表面加工分析
5.6.2非回转零件的加工工艺案例分析
本章小结
思考题与练习题
第三篇机械加工质量
第六章机械加工精度
6.1机械加工精度的基本概念
6.1.1加工精度与加工误差
6.1.2研究加工精度的方法
6.2影响加工精度的因素
6.2.1加工原理误差
6.2.2机床误差
6.2.3工艺系统受力变形
6.2.4工艺系统的热变形
6.2.5工件残余应力引起的变形
6.3加工误差的统计分析
6.3.1加工误差的分类
6.3.2分布曲线法
6.3.3点图法
6.4提高加工精度的途径
6,4.1减少误差法
6.4.2误差补偿法
6.4.3误差分组法
6.4.4误差转移法
6.4.5“就地加工”法
6.4.6误差平均法
6.4.7误差补偿法
本章小结-
思考题与练习题
第七章机械加工表面质量
7.1机械加工后的表面质量
7.1.1表面质量的含义
7.1.2表面质量对零件使用性能的影响
7.2机械加工后的表面粗糙度
7.2.1切削加工后的表面粗糙度
7.2.2磨削加工后的表面粗糙度
7.3机械加工后表面层的物理力学性能
7.3.1机械加工后表面层的冷作硬化
7.3.2机械加工后表面层金相组织的变化
7.3.3机械加工后表面层的残余应力
7.4控制加工表面质量的工艺途径
7.4.1减小残余拉应力、防止磨削烧伤和磨削裂纹的工艺途径
7.4.2采用冷压强化工艺
7.4.3采用精密和光整加工工艺
7.5机械加工过程中的振动问题
7.5.1振动的概念与类型
7.5.2机械加工中的强迫振动
7.5.3机械加工中的自激振动
7.5.4减少工艺系统振动的途径
本章小结
思考题与练习题
第四篇机器装配工艺
第八章机器装配工艺
8.1机器装配基本问题概述
8.1.1各种生产类型的装配特点
8.1.2零件精度与装配精度的关系
8.1.3装配中的连接方式
8.2保证装配精度的方法
8.2.1互换法
8.2.2选配法
8.2.3修配法
8.2.4调整法
8.3装配工艺规程的制订
8.3.1装配工艺规程的内容
8.3.2装配工艺规程的制订步骤和方法
本章小结
思考题与练习题
机械制造技术名词术语中英文对照
参考文献
机械制造技术_机械制造技术基础 -文摘
版权页:
插图:
前面几节分析了各种主要因素对机械加工精度的影响,这些分析属于局部的、单因素的性质。生产过程中影响加工精度的因素往往是错综复杂的,有时很难用单因素来分析其因果关系,而要用数理统计方法来找出解决问题的途径。
6.5.1 系统误差与偶然误差的概念
各种单因素的加工误差,按其性质的不同可分为系统误差与偶然误差。
1.系统误差
当顺次加工一批零件时,大小保持不变或者是有规律变化着的误差称为系统误差。前者是常值系统误差,后者是规律性变化的系统误差(变值系统误差)。例如,用一把直径小于规定尺寸0.02的铰刀,铰出的所有孔的直径都比规定尺寸小0.02,这种误差就是常值系统误差。又如车轴时,由于车刀磨损,车削出来的轴直径就一个比一个大,轴直径的增大是有一定规律的,所以刀具磨损引起的误差就属于规律性变化的系统误差(变值系统误差)。再如工艺系统的热变形,也属于变值系统误差。
2.偶然误差
在加工一批零件中,这类误差的大小和方向均是无规律地变化着的,有时大,有时小,有时正,有时负。这类误差称为偶然误差。例如,用一把铰刀加工一批零件的孔时,在相同的条件下,仍然得不到直径尺寸完全相同的一批孔,这可能是毛坯硬度不均匀、加工余量有差异、内应力重新分布引起变形等因素所造成的,这些因素都是变化不定的。虽然偶然误差引起的原因是各种各样的,它们的作用情况又很复杂,但可以应用数理统计方法找出偶然误差的规律,并加以控制。 --此文字指其他 平装 版本。
机械制造技术_机械制造技术基础 -作者简介
司乃钧,1938年12月生,北京人,大学文化,哈尔滨理工大学工业技术学院机械系室主任,教授。主编9本大学专科全国统统教材,由高教出版社和机械工业出版社出版发行;1980年获机械部优秀教材二等奖。主审全国统编教材5本,由高教出版社和机械工业出版社出版。发表论文20余篇。1991年获黑龙江省优秀教学成果一等奖;1993年获国家级优秀教学成果二等奖;1996年获国家教委优秀教材一等奖。
许小村,女,1964年5月出生,哈工大博士,教授,硕士生导师。1986年毕业于哈尔滨工业大学锻压专业,获学士学位。1991毕业于哈尔滨工业大学机制专业,先后获得硕士、博士学位。1986年到哈尔滨科技大学任教至今,主讲“金属工艺学”、“机械概论”“现代工业技术概论”。主持完成省科技攻关项目2项:“超硬磨料磨削用软片开发研究”和“胶接式切削工具开发研究”,主持完成校青年基金项目1项:“复杂形面超硬磨料工具开发研制”。参研(排名2、3)完成省、市级科研项目6项:“可转位涂层气门座铰刀及磨轮”、“新型多功能输送泵系列开发”、“内冷式螺旋孔钻头开发研制”等。获中国机械工程学会科技进步奖一等奖1项(“切屑形成与折断的机理、虚拟现实、预报系统及其应用”排名14)、三等奖1项(“可转位涂层气门座铰刀及磨轮”排名2),获机械部教育司科技进步一等奖2项(“气门座工具开发”“新型多功能输送泵系列开发”排名2、4),获机械部教育司科技进步二等奖1项(“超硬磨料磨削用软片开发研究”排名1)。获哈尔滨科技成果储备库二等奖1项(“可转位涂层气门座铰刀及磨轮”排名2)。现在主持在研黑龙江省科技攻关项目1项“浮动式模具抛光机开发”,主持在研黑龙江省教育厅一般科研项目一项“汽车模具精加工工艺研究”。参研黑龙江省科技攻关项目一项“超硬磨料磨削软片关键技术研究”(排名2)。发表论文23篇,被SCI、ISTP检索各一篇。出版着作2部:《超硬磨料特种磨具制作技术》《数控铣刀CAD/CAE/CAM技术》。
机械制造技术_机械制造技术基础 -序言
本书是根据教育部颁发的《工程材料及机械制造基础课程教学基本要求》编写的。主要用于高等工科院校机械类、近机类专业的本科生教材,也可作为工程技术人员的参考用书。
本课程属于专业(技术)基础课,通过本课程的学习,使学生熟悉或掌握有关机械制造技术的基础知识、基础理论、基本技能和工程应用。本书体系完整、内容充实、结构合理,理论性和实用性并举,力求做到重点突出、内容少而精,使教材清晰、形象,易于讲授和自学。本书强调理论联系实际,注重强化能力和技术创新精神。
本课程实践性很强,学习前应有一定感性知识,因此应在工程训练(或金工实习)后进行讲授。学生通过工程训练或金工实习,熟悉了各种主要切削加工方法的操作过程,所用设备、工具、夹具和量具的基本原理和大致结构,并对毛坯或零件加工工艺过程有了一定了解,在此基础上学习本书,才能达到本课程教学预期的目的和要求。
机械制造技术_机械制造技术基础 -后记
本书是教育科学“十五”国家规划课题――“21世纪中国高等学校应用型人才培养体系的创新与实践”机械类子课题的研究成果,是应用型机械类系列教材之一。结合课题的立项研究,应用型机械类系列教材组成了教材编写委员会,负责整套教材的编写组织工作。编写委员会成员如下:
主任:刘迎春
副主任:宁立伟 熊志卿 王华 周骥平 唐国兴 李建启
姚必强 王林鸿
委 员:刘明 杜瑞成 方新 钟守炎 于惠力 朱志宏 徐文宽
蔡小梦 陈立德 舒小平 王安民 刘庆国 李建华 孙如军
邢邦圣 余五新 蒋同洋 倪宏昕 耿跃宏 胡琳 田忠友
傅志红 何法江 曹晓明 续海峰 曾励
编者在此谨对编写委员会在教材编写过程中提供的指导和帮助表示衷心感谢。