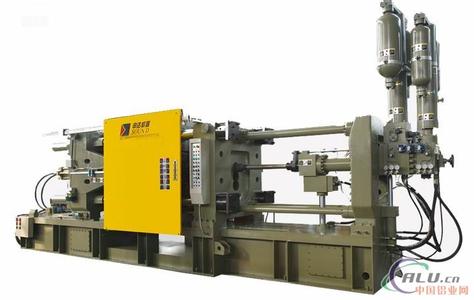
压铸机就是在压力作用下把熔融金属液压射到模具中冷却成型,开模后得到固体金属铸件的一系列工业铸造机械,最初用于压铸铅字。随着科学技术和工业生产的进步,尤其是随着汽车、摩托车以及家用电器等工业的发展,诸方面出发,压铸技术已获得极其迅速的发展。
立式压铸机_压铸机 -压铸机
压铸机型压铸机就是在压力作用下把熔融金属液压射到模具中冷却成型,开模后得到固体金属铸件的一系列工业铸造机械,最初用于压铸铅字。随着科学技术和工业生产的进步,尤其是随着汽车、摩托车以及家用电器等工业的发展,又从节能、节省原材料诸方面出发,压铸技术已获得极其迅速的发展。
立式压铸机_压铸机 -目录
压铸机的分类压铸技术工艺的发展简史最新方向压铸机的分类及其工作方式各类压铸机的工作方式选用压铸机的基本原则压铸机的使用与维护SAJS350矢量变频器在压铸机的应用特点压铸机安全操作规程展开
编辑本段压铸机的分类压铸技术工艺的发展简史压铸的起源众说不一,但据文献报导,最初用于压铸铅字。早在1822年,威廉姆?乔奇(WillamChurch)博士曾制造一台日产1.2~2万铅字的铸造机,已显示出这种工艺方法的生产潜力。1849年斯图吉斯(J.J.Sturgiss)设计并制造成第一台手动活塞式热室压铸机,并在美国获得了专利权。1885年默根瑟勒(Mersen-thaler)研究了以前的专利,发明了印字压铸机,开始只用于生产低熔点的铅、锡合金铸字,到19世纪60年代用于锌合金压铸零件生产。压铸广泛用于工业生产还只是上世纪初,应用于现金出纳机、留声机和自行车的产品生产中。1904年英国的法兰克林(H.H.Franklin)公司开始用压铸方法生产汽车的连杆轴承,开创了压铸零件在汽车工业中应用的先例。1905年多勒(H.H.Doehler)研制成功用于工业生产的压铸机、压铸锌、锡、铜合金铸件。随后瓦格纳(Wagner)设计了鹅颈式气压压铸机,用于生产铝合金铸件。
1927年捷克工程师约瑟夫?波拉克(Jesef
Pfolak)设计了冷压室压铸机,由于贮存熔融合金的坩锅与压射室分离,可显著地提高压射力,使之更适合工业生产的要求,克服了气压热压室压铸机的不足
之处,从而使压铸技术向前推进了一大步。铝、镁、铜等合金均可采用压铸生产。由于整个压铸过程都是在压铸机上完成,因此,随着对压铸件的
质量、产量和扩大应用的需求,已对压铸设备不断提出新的更高的要求,而新型压铸机的出现以及新工艺、新技术的采用,又促进压铸生产更加迅速地发展。例如,
为了消除压铸件内部的气孔、缩孔、缩松,改善铸件的质量,出现了双冲头(或称精、速、密)压铸;为了压铸带有镶嵌件的铸件及实现真空压铸,出现了水平分型
的全立式压铸机;为了提高压射速度和实现瞬时增加压射力以便对熔融合金进行有效地增压,以提高铸件的致密度,而发展了三级压射系统的压铸机。又如,在压铸生产过程中,除装备自动浇注、自动取件及自动润滑机构外,还安装成套测试仪器,对压铸过程中各工艺参数进行检测和控制。它们是压射力、压射速度的显示监控装置和合型力自动控制装置以及电子计算机的应用等。
近40年,随着科学技术和工业生产的进步,尤其是随着汽车、摩托车以及家用电器等工业的发展,
又从节能、节省原材料诸方面出发,压铸技术已获得极其迅速的发展。压铸生产不仅在有色合金铸造中占主导地位,而且已成为现代工业的一个重要组成部分。近年来,一些国家由于依靠技术进步促使铸件薄壁化、轻量化,因而导致以往用铸件产量评价一个国家铸造技术发展水平的观念改变为用技术进步的水平作为衡量一个国家铸造水平的重要依据。编辑本段最新方向压铸生产不仅在有色合金铸造中占主导地位,而且已成为现代工业的一个重要组成部分。近年来,一些国家由于依靠技术进步促使铸件薄壁化、轻量化,因而导致以往用铸件产量评价一个国家铸造技术发展水平的观念改变为用技术进步的水平作为衡量一个国家铸造水平的重要依据。例如我国的较好的压铸机品牌就有“力劲、伊之密、宝洋”等...压铸机的分类及其工作方式压铸机的分类方法很多,按使用范围分为通用压铸机和专用压铸机;按锁模力大小分为小型机(≤4000kN)、中型机(4000kN~10
000kN)和大型机(≥10000kN);通常,主要按机器结构和压射室(以下简称压室)的位置及其工作条件加以分类。
压铸机分热压室压铸机和冷压室压铸机两大类。冷压室压铸机按其压室结构和布置方式又分卧式、立
式两种形式。热压室压铸机与冷压室压铸机的合模机构是一样的,其区别在于压射、浇注机构不同。热压室压铸机的压室与熔炉紧密地连成一个整体,而冷压室压铸
机的压室与熔炉是分开的。
立式压铸机_压铸机 -有以下基本分类:
热室压铸机冷室压铸机
常规热室压铸机
卧式热室压铸机
立式冷室压铸机
卧式冷室压铸机
全立式冷室压铸机组成
立式压铸机_压铸机 -压铸机由下列各部分组成
(1)合模机构驱动压铸模进行合拢和开启的动作。当模具合拢后,具有足够的能力将模具锁紧,确保在压射填充的过程中模具分型面不会胀开。锁紧模具的力即称为锁模力(又称合型力),单位为千牛(kN),是表征压铸机大小的首要参数。
(2)压射机构
按规定的速度推送压室内的金属液,并有足够的能量使之流经模具内的浇道和内浇口,进而填充入模具型腔,随后保持一定的压力传递给正在凝固的金属液,直至形成压铸件为止。在压射动作全部完成后,压射冲头返回复位。
(3)液压系统
为压铸机的运行提供足够的动力和能量。
(4)电气控制系统
控制压铸机各机构的执行动作按预定程序运行。(5)零部件及机座
所有零部件经过组合和装配,构成压铸机整体,并固定在机座上。
(6)其他装置先进的压铸机还带有参数检测、故障报警、压铸过程监控、计算机辅助的生产信息的存储、调用、打印及其管理系统等。
(7)辅助装置
根据自动化程度配备浇料、喷涂、取件等装置。编辑本段各类压铸机的工作方式立式冷室压铸机的工作方式
压室7呈垂直放置,而上冲头8处于压室上方(图上方的位置),下冲头10则位于堵住喷嘴5孔口处,以免金属液浇入压室内自行流入喷嘴孔。模具的开、合动作呈水平移动,开模后,压铸件留在动模。工作步骤如下:
(1)合拢模具;
(2)以人工或其他方式将金属液浇入压室;
(3)上冲头以较低的压射速度下移,进入压室内及至刚接触金属液液面;
(4)上冲头转为较高的压射速度压下,而下冲头则与上冲头保持着中间一段存有金属液的相对距离同步地快速下移;
(5)当下冲头下移至让出喷嘴孔口时,正好下到最底部而被撑住;于是,上、下冲头一同挤压金属液高速向喷嘴孔(直浇道6的一部分)喷射;
(6)金属液通过由喷嘴、浇口套4、定模的锥孔和分流器2组成的直浇道6,从内浇口3填充进入模具型腔;
(7)填充完毕,但上冲头仍保持一定的压力,直至型腔内的金属液完全凝固成压铸件1为止;浇道和压室内的金属液分别凝固为直浇口和余料饼9;
(8)上冲头提升复位;同时,下冲头向上动作,将尚与直浇口相连的余料饼切离;
(9)下冲头继续上升,把余料饼举出压室顶面,再以人工或其他方式取走;
(10)下冲头下移复位至堵住喷嘴孔口;
(11)打开模具,压铸件和直浇口一同留在动模上,随即顶出并取出压铸件;一旦切离余料饼之后,开模动作可以立即执行,也可以稍缓至适当的时候执行,与下冲头完成上举和复位的动作无关;
至此,完成一次压铸循环。
卧式冷室压铸机的工作方式
压室7呈水平放置,压射冲头5处于压室最右端虚线位置。模具的开、合动作呈水平移动,开模后,压铸件留在动模。工作步骤如下:
(1)合拢模具;
(2)将金属液以人工或其他方式浇入压室;
(3)压射冲头按预定的速度和一定的压力推送金属液,使之通过模具的浇道3,从内浇口2填充进入模具型腔;
(4)填充完毕,冲头保持一定的压力,直至金属液完全凝固成为压铸件1为止;这时,浇道和浇口套6(没有浇口套的模具在该处即为连体压室)内的金属液也同时凝固,成为浇口和余料饼4;
(5)打开模具,冲头与开模动作同步移动,从而推着余料饼随着压铸件和浇口一同留在动模而脱离定模,到达一定的距离时,冲头便返回复位;
(6)开模后,压铸件、浇口和余料饼留在动模上,随即顶出并取出压铸件;
至此,完成一次压铸循环。
全立式冷室压铸机的工作方式
压室5垂直放置在机器的下部,模具的开、合动作为上下移动,故称为全立式压铸机。通常模具的动模固定在上方,开模后,压铸件留在动模。工作步骤如下:
(1)将金属液以人工或其他方式浇入压室;
(2)合拢模具;
(3)冲头6上移压送金属液,通过浇道3、分流器4,从内浇口2填充进入模具型腔;
(4)填充完毕,冲头保持一定的压力直至金属液完全凝固成为压铸件1为止;这时,浇道和压室内的金属液也同时凝固,而压室内的便成为余料饼7;
(5)打开模具,冲头与开模动作同步向上移动,从而使余料饼跟随压铸件和浇口一同随着动模上移而脱离定模,到达一定的距离时,冲头便下移复位;
(6)开模后,随即顶出并取出压铸件;
至此,完成一次压铸循环。编辑本段选用压铸机的基本原则压铸机的选用,对压铸生产过程中的产品质量、生产效率、管理成本等诸多方面,有着十分重要的影响。为此,合理地选择适用的压铸机,是一项技术性和经济性都很强的工作。
热室压铸机的特点目前生产中,多数采用常规的热室压铸机。市场供应的以锁模力小于4000kN的机器为主导,更多的则是锁模力在1600kN以下,而锁模力大于4000kN的很少。其特点如下:
(1)通常以低熔点合金的压铸为主,而以锌合金最为典型;
(2)以小型压铸件的生产为宜,中、大型压铸件不宜采用热室压铸;
(3)填充进入模具型腔的金属液始终在密闭的通道内流动,氧化夹杂物不易卷入,对压铸件的质量较为有利;
(4)压铸过程的自动化容易实现;
(5)由于不需要浇料程序,在正常运行的状态下,生产效率较高;
(6)压射比压稍低,并且压射过程没有增压阶段,但对小型、薄壁件影响较小;
(7)压射冲头、浇壶、喷嘴等热作件的寿命难以掌握和控制,失效后更换较为费时;
(8)更换或修理熔炉时,要拆装热作件,增加了辅助时间;
(9)对于高熔点合金的热室压铸,目前仍以镁合金较为适宜,而用于镁合金的热室压铸机,同样存在上述的特点。
立式冷室压铸机的特点(1)适合于锌、铝、镁、铜等多种合金的压铸;
(2)生产现场中用量较少,并以小型机占多数;
(3)压室呈垂直放置,金属液浇入压室后,气体在金属液上面,压射过程中包卷气体较少;
(4)压射压力经过的转折较多,使压力传递受到影响,尤其在增压阶段,因喷嘴入口处的孔口较小,压力传递不够充分;
(5)方便于开设中心浇口;
(6)机器的长度方向占地面积较小,但机器的高度相对较高;(7)下冲头部位窜入金属液时,排除故障的工作不方便;
(8)生产操作中有切断余料饼和举出料饼的程序,降低生产效率;
(9)采用自动化操作时,增加从下冲头的顶面取走余料饼的程序。
卧式冷室压铸机的特点(1)适合于各种有色合金和黑色金属(目前尚不普遍)的压铸;
(2)机器的大小型号较为齐全;
(3)生产操作少而简便,生产效率高,且易于实现自动化;
(4)机器的压射位置较容易调节,适应偏心浇口的开设,也可以采用中心浇口,此时模具结构需采取相应措施;
(5)压射系统的技术含量较高;
(6)压射过程的分级、分段明显并容易实现,能够较大程度地满足压铸工艺的各种不同的要求,以适应生产各种类型和各种要求的压铸件;(7)压射过程的压力传递转折少;
(8)压室内金属液的水平液面上方与空气接触面积较大,压射时易卷入空气和氧化夹杂物;对于高要求或特殊要求的压铸件,通过采取相应措施仍能得到较满意的结果。
全立式冷室压铸机的特点(1)广泛用于电机转子的压铸,多为中小型机器;
(2)此类压铸机比同吨位其他压铸机器的占地面积小,但高度较高;
(3)金属液进入模具型腔时转折少、流程短,压力损耗小;
(4)浇注金属液时,需越过模具分型面,应保证液滴不会滴在模具分型面上;
(5)压射机构在下方,更换压室和维修工作都不方便。
选用压铸机的基本原则(1)了解压铸机的类型及其特点;
(2)考虑压铸件的合金种类以及相关的要求;
(3)选择的压铸机应满足压铸件的使用条件和技术要求;
(4)选定的压铸机在性能、参数、效率和安全等方面都应有一定的裕度,以确保满意的成品率、生产率和安全性;
(5)在保证第4点的前提下,还应考虑机器的可靠性与稳定性,据此来选择性价比合理的压铸机;
(6)对于压铸件品种多而生产量小的生产规模,在保证第4点的前提下,应科学地选择能够兼容的规格,使既能含盖应有的品种,又能减少压铸机的数量;
(7)在压铸机的各项技术指标和性能参数中,首要应注意的是压射性能,在同样规格或相近规格的情况下,优先选择压射性能的参数范围较宽的机型;
(8)在可能的条件下,尽量配备机械化或自动化的装置,对产品质量、生产效率、安全生产、企业管理以及成本核算都是有益的;
(9)评定选用的压铸机的效果,包括:成品率、生产率、故障率、维修频率及其工作量、性能的稳定性、运行的可靠性以及安全性等。
选型前的技术测算工作选型的原始要素包括压铸件的图样、实物、合金种类、最大外廓尺寸(长×宽×高)、净重、平均壁厚、最大壁厚、最小壁厚、需要抽芯的方向及个数、需要抽芯的最大长度以及特殊结构。压铸件的使用条件和技术要求(包括后续加工工序)。
生产大纲需求量(月度、季度或年度)、压铸生产的工作制度。
(1)初定压铸机的锁模力测算模具分型面上的金属投影面积,设为A(mm2),通常包括压铸件
(按型腔数)、浇道系统、溢流系统和压室直径等4个部分的面积的总和(当有真空抽气道时应另加)。根据压铸件的技术要求选用增压比压,设为
pz(MPa);模具分型面上金属投影的胀型力,设为F1(kN),则
F1=A×pz
动、定模合拢楔紧斜面(含抽芯机构)在合模方向的分力的总和,设为F2(kN);合模方向的胀型力的总和,设为F0(kN),于是
F0=F1+F2
选择的压铸机的锁模力,设为F(kN),同时考虑安全系数k(一般取0.85~0.95),测算时,选择压铸机的锁模力F应大于胀型力F0,即
F>F0/k
(2)查对已选的压铸机与模具体积及安装尺寸的匹配情况①压铸机4根大杠(又称拉杠)的内间距
应大于模具的横向与竖向的模板外廓尺寸;②压铸机可调的模具厚度尺寸应在模具总厚度(含定模、动模和动模座)的范围之内;③压铸机的开合模行程应满足压铸
后能够顺利取出压铸件所需要的开模距离;
(3)查核压铸机的压室能够容纳的金属液的重量①估算浇入压室的金属液的重量G0(g或
kg),包括压铸件(按型腔数)、浇道系统、溢流系统和余料饼等4个部分的总和;②根据已初步选定的压室直径,查阅机器样本或机器说明书中关于该直径的压
室允许容纳的最大金属液重量G(g或kg);③查核时,应满足
G>G0。
经过上述的初步测算,便有了预选压铸机的型号和规格的技术基础。在正式设计模具时,选用的技术参数可能会有些差异,只要稍作调整就能解决。
估算压铸生产的节拍压铸的生产节拍按一个压铸工作循环作为计算单位,通常从合模开始,经过各种动作和各个环节,直至下一次合模为止,即作为一个工作循环。这个工作循环所需的时间,称为每模需要的时间,以“s/模”表示。压铸生产时,每模需要的时间由下列几个部分组成。
(1)机器一次空循环时间压铸机按机动顺序所作的每一个空循环所需的时间称为一次空循环时间。
对于热室压铸机,包括:合模、压射、压射回程、开模、顶出和顶出返回诸动作所用的时间的总和,是为一次空循环时间。
对于立式冷室压铸机,包括:合模、压射、压射回程、下冲头切料并举料、下冲头返回、开模、顶出和顶出返回诸动作所用的时间的总和,是为一次空循环时间。
对于卧式冷室压铸机,包括:合模、压射、开模、冲头跟出、压射回程、顶出和顶出返回诸动作所用的时间的总和,是为一次空循环时间。
对于全立式冷室压铸机,包括:合模、压射、开模、冲头上举、压射回程、顶出和顶出回程诸动作所用的时间的总和,是为一次空循环时间。
(2)压铸操作需用的时间浇料的运行时间(指冷室压铸机,有手工的、机械的和气压式的);
润滑压射冲头的时间;
对模具喷涂润滑剂、等候润滑剂挥发、清理模具等操作所用的时间;
取件时间;
对于立式冷室压铸机,下冲头举起余料饼至高于压室顶面后,取走余料饼的时间;
检查压铸件的时间(人工目测时加入);
放置铸入镶件至模具内的时间(有这一操作时加入)。
(3)工艺需要的时间金属液浇入压室后等待静置的时间(指冷室压铸机);
压射终了需持续施压的持压时间;
压射填充完毕,压铸件凝固过程所需的延续留在模具内的留模时间;
抽芯动作占用的时间(有手工的活镶块或液压抽芯时加入)。
(4)其他原因造成的追加时间因模具结构复杂,需要增加操作程序或工艺程序造成的追加时间;
因模具的原因(如模具结构不合理、旧模具)而不能顺利操作造成的延迟时间;
因压铸件产生变形,需要采取补救措施(如加长留模时间)造成的追加时间;
因其他原因造成的追加时间。
测算生产节拍时,根据实际需要选择应加入测算的项目。每模型腔数多于1时,在按上述项目测算的结果的基础上,再酌情追加时间,但不需按型腔数的倍数增加。压铸机生产能力的测算(1)测算用的基本要素每模型腔数设为N,用“型腔数/模”表示。
单位时间的压铸模数根据估算的生产节拍(s/模),测算时,换算为每小时压铸的模数(模/h),设为M。
根据各个企业自行安排的工作制度,确定班、日、周、月、季和年的工作时间,可以分别计算,也可以按年度计算,设单台压铸机的工作台时数为T,计算单位以“h”表示。
影响压铸的成品率的因素很多,成品率的高低,直接关系到压铸机生产能力的测算,设为C(小于1)。
其它不固定的因素,设为K(小于1),如:新模具或修复的模具的试模、新产品模具的工艺参数调整与试验、因周边设备(熔炉或保温炉等)出现故障、机器检修后的试机以及动力系统的检修或临时性失效等。
(2)测算单一品种压铸件的压铸机生产能力压铸件的需求量设为Q,计算单位用“件”表示。机器的生产能力测算时的计算单位与生产大纲对应,如:月度、年度等,设为Q0。
测算机器的生产能力,按下式计算:Q0=N・M・T・C・K。
将需求量Q与机器生产能力Q0进行比较:当Q0≥Q时,只用1台机器可以满足需求;当Q0<Q时,则按Q/Q0的倍数增加压铸机的台数。
(3)测算多品种压铸件的压铸机生产能力按各个品种个别测算所选的压铸机的型号和规格以及该压铸机的Q0,然后与各自品种的生产大纲的需求量Q加以比较:
①当不同品种可以用相同类型和规格的压铸机时,将这些品种的Q加以合并计算,再确定压铸机的台数;
②当不同品种必须分别选用不同类型和规格的压铸机时,则各自确定所选的压铸机的台数。
综上所述,压铸机的选型工作十分繁琐,初选时只能用估计与预测的方法,其准确性则与掌握压铸知识的程度以及实践经验有关。由于压铸件的品种多、门类广、要求高,产量大,这里介绍的选用原则和测算方法可能还不够全面,仅作基本参考之用。编辑本段压铸机的使用与维护冷室机主要用来生产熔点较高的铜、铝及镁(厚壁)等合金的压铸件。热室机用来生产熔点较低的锌、锡、铅及镁(薄壁)等合金的压铸件。与冷室机相比,由于热室机的压射室直接浸在合金溶液中工作,可省去浇注操作,因此工作循环周期短,工作效率高。
为了保证压铸机的正常运行,应在正确的使用的同时,还应进行科学的维护工作[5]。因此,必须根据说明书的要求和相关的规定,制订出机器的使用操作规程和维护管理制度,特别是安全规程,专人负责,认真贯彻落实,严禁违章作业。1每日操作维护(1)清理机器上杂物和所有滑动表面上的灰尘、污物,对非自动润滑的滑动摩擦面进行润滑,检查保持润滑油箱内油量正常;
(2)检查液压油(液)容箱中的液位和管路有无渗漏现象,各连接紧固件有无松动;
(3)查看压力表指示是否正常,安全装置及行程开关是否正常;
(4)检查液压系统的压力、液压油(液)温度和颜色是否正常;
(5)查看自动润滑系统工作是否正常,特别是曲肘销套润滑情况;
(6)检查压室和冲头损伤情况,并及时清理和润滑;
(7)检查冷却系统是否正常;
(8)检查机器在运行中有无异常振动与噪声,及时进行处理。2每周(约40小时)操作维护(1)清理机器上的脏物,特别注意合模机构的曲肘部分;
(2)润滑油箱保持有充足的润滑油,检查润滑系统的润滑功能;
(3)检查安全防护装置及行程开关是否正常,及时修理和紧固;
(4)检查并紧固各连接紧固件;
(5)检查液压系统有无渗漏,蓄能器充氮气的压力变化(有无漏气);
(6)检查压射位置和大杠螺母位置是否与调定位置有变化并及时调好;
(7)检查电磁阀和操作按钮等元件的紧固情况。3每月操作维护(1)对机器进行一次较彻底的清理;
(2)清洗过滤器滤芯;
(3)检查大杠与导套间隙是否正常,大杠及导轨有无拉伤,遇有拉伤时应及时用油石修平;
(4)全面检查和上紧液压缸和液压管路连接紧固件(包括蓄能器的固定);
(5)检查电气箱、操纵箱等密封情况,清理其内附着尘物,上紧各元件及电线连接件;
(6)检查或更换有损伤的电线和元件;
(7)检查润滑系统的润滑功能;
(8)检查紧固机器定板大杠螺母的紧固螺钉;
(9)在首次启动机器或大修后首次启动满300
h,应清洗更换滤芯,将液压油(液)重新过滤(过滤程度按机器说明书规定),并且对机器的油箱也应重新清理,然后加注经过过滤的液压油(液);以后每运转
3000~4000
h,检查液压油(液)质量合格后才能重新过滤加入,否则应更换新的液压油(液);液压油(液)污染度等级极限VASⅡ,对比例系统为NAS8级。
压铸机常见故障及排除故障现象产生原因排除方法1.系统无压力或压力不足①液压泵转向不对
②溢流阀调整不当或损坏
③液压泵故障
④管路内外泄漏量大
⑤吸油(液)不足(油/液面低,吸油/液管堵塞或漏气)①调整电机转向
②重新调整或更换新阀
③修理或更换
④检修管路和元件
⑤补充油(液),检修吸油(液)管路2.系统供油(液)量不足①油(液)箱油(液)位过低,吸油(液)不足
②液压泵故障或泵转速低
③泵、阀、液压缸及管路泄漏量大
④液压控制阀动作失灵
⑤液压油(液)粘度过大或过小
⑥回油管口在液面以上吸进空气
①补充油(液),检修吸油(液)管路
②检修更换液压泵,提高泵转速
③检修相应元件及管路
④检修或更换
⑤更换液压油(液)
⑥改进回油到液面下3.液压油(液)温度过高①冷却水未打开②冷却器积垢或故障
③循环过程无用高压溢流过多
④液压系统内泄过大
⑤液压泵故障
⑥液压油(液)粘度过大、过小
⑦油箱散热不足①接通冷却水
②清洗或检修、更换
③调整工作程序,检修调节溢流阀
④检修或更换元件
⑤检修更换液压泵
⑥换液压油(液)
⑦改善散热部件4.振动噪声异常①液压泵故障
②溢流阀故障
③液压泵电机不同轴
④油(液)位低,吸油(液)管堵塞或漏气
⑤液压油(液)污染
⑥系统管路配置不当,造成振动或共振①检修或更换
②检修或更换
③调节同轴度
④补充油(液),检修吸油(液)管路
⑤换液压油(液)
⑥合理布置元件和管路,改进固定方式5.合模及压射缸爬行①空气进入液压系统
②液压缸和运动件导向、润滑不良
③液压泵压力和流量不匀
④液压缸密封阻力、弯曲、表面拉伤等
⑤控制阀开口过小或故障
⑥液压油(液)粘度过大①检修改进系统,排出液压缸内空气
②检修、改善导向,适当给以润滑
③见1、2条的的排除方法
④检修油缸
⑤适当调节或检修
⑥换液压油(液)或提高液压油(液)温6.机器不合模①护门未关到位,联锁行程开关未动作
②合模阀未动
③合模机构动作受阻
④模具型芯未插到位,行程开关未动
⑤液压系统压力不足①检查排除护门故障和行程开关
②检查电磁阀是否通电或卡死,修复
③检查清除障碍
④检修
⑤见1条的排除方法7.合模不到位(曲肘伸不直)①合模开档调节不当,锁模力过大
②模具分型面上有粘着物,低压保护开关起作用
③液压系统压力不足
④合模机构故障①适当调小开档
②清除障碍物,检查保护行程开关
③见1条的排除方法
④检修8.慢夺射不动作①合模不到位,行程开关未动作
②慢压射阀故障
③压射头卡住①见7条的排除方法
②检修阀和控制电路
③检修或更换压射室和压射头9.无快压射或快压射速度不足或下降过大①快压射阀故障,转换开关未动作
②蓄能器压力不足,氮气泄漏或活塞卡死
③快压射阀开口不足①检修快压阀射阀和控制电路
②检修蓄能器或充氮
③调大开口10.快压射后无增压①增压阀故障
②液压系统压力低于蓄能器充气压力①检修增压控制阀及控制线路
②见1条的排除方法11.增压压力下降过快直到无增压①压射油缸内漏大
②增压活塞杆与浮动活塞密封处泄漏或增压行程不足①检修或更换密封件
②检修12.增压冲击峰值过大或增压迟后过多①增压阀开口过大
②增压控制阀节流过小①适当关小阀口
②适当开大节流口13.压射不回程①压射阀故障
②跟出未到位,返回行程开关未动作①检修压射阀和控制线路
②检修(见8条之③的排除方法)14.压射头拉伤快或易卡死①压射室与压射缸活塞杆不同轴②压射室与浇口套不同轴或端面结合有缝隙
③压射头冷却不足
④压射室或压射头损伤①检修调整同轴度
②检修两者同轴度和端面
③改善冷却系统
④更换新件或修复编辑本段SAJS350矢量变频器在压铸机的应用特点S350系列是新一代高性能矢量变频器,有如下特点:
■采用最新高速电机控制专用芯片DSP,确保矢量控制快速响应
■硬件电路模块化设计,确保电路稳定高效运行
■外观设计结合欧洲汽车设计理念,线条流畅,外形美观
■结构采用独立风道设计,风扇可自由拆卸,散热性好
■无PG矢量控制、有PG矢量控制、转矩控制、V/F控制均可选择
■强大的输入输出多功能可编程端子,调速脉冲输入,两路模拟量输出
■独特的“挖土机”自适应控制特性,对运行期间电机转矩上限自动限制,有效抑制过流频繁跳闸
■宽电压输入,输出电压自动稳压(AVR),瞬间掉电不停机,适应能力更强
■内置先进的PID算法,响应快、适应性强、调试简单;16段速控制,简易PLC实现定时、定速、定向等多功能逻辑控制,多种灵活的控制方式以满足各种不同复杂工况要求
■内置国际标准的MODBUSRTUASCII通讯协议,用户可通过PC/PLC控制上位机等实现变频器485通讯组网集中控制编辑本段压铸机安全操作规程1.开动电动机前,首先将泄压阀手柄放在泄压位置,待电动机正常运转后,再放开泄压阀柄。
2.压射前一定要把模型先加热到规定的温度,然后才可以压入金属溶液。
3.模具分型面接触处与浇口处,应使用防护挡板,操作人员必须戴防护眼镜。操作人员不得站在分型面接触处的对面。以防金属液体喷溅伤人。
4.禁止带明火物品靠近油箱。油箱温度超过设备运行规定温度时,应用水冷却。
5.从压铸模上取下铸件与浇冒口时,应使用工具。取下铸件后,应及时清除铸型上和通气孔内粘附的金属残屑。
6.工作完毕时,必须停住油泵,关闭所有阀门。如系采用保温炉对金属液保温者,应关闭电源,停止保温炉上的通风设备。