转炉_转炉 -释义
词目:转炉拼音:zhuàn lú
基本解释
[converter] 一种可以转动的圆筒状炼钢高炉
详细解释
炼钢炉的一种。炉体圆筒形,架在一个水平轴架上,可以转动。也用来炼铜。雁翼《重钢晚霞》诗:“烟囱四处生长,像森林般稠密;高炉、平炉、转炉,像山峰般挺立。”《工人歌谣·小转炉》:“小转炉,张大嘴,没有胳膊没有腿,嘴里喷金花,低头吐钢水。”
转炉_转炉 -概述
转炉(converter)炉体可转动,用于吹炼钢或吹炼锍的冶金炉。转炉炉体用钢板制成,呈圆筒形,内衬耐火材料,吹炼时靠化学反应热加热,不需外加热源,是最重要的炼钢设备,也可用于铜、镍冶炼。转炉按炉衬的耐火材料性质分为碱性(用镁砂或白云石为内衬)和酸性(用硅质材料为内衬)转炉;按气体吹入炉内的部位分为底吹、顶吹和侧吹转炉;按吹炼采用的气体,分为空气转炉和氧气转炉。转炉炼钢主要是以液态生铁为原料的炼钢方法。其主要特点是:靠转炉内液态生铁的物理热和生铁内各组分(如碳、锰、硅、磷等)与送入炉内的氧进行化学反应所产生的热量,使金属达到出钢要求的成分和温度。炉料主要为铁水和造渣料(如石灰、石英、萤石等),为调整温度,可加入废钢及少量的冷生铁块和矿石等。在转炉炼钢过程中,铁水中的碳在高温下和吹入的氧生成一氧化碳和少量二氧化碳的混合气体,即转炉煤气。转炉煤气的发生量在一个冶炼过程中并不均衡,且成分也有变化,通常将转炉多次冶炼过程回收的煤气经降温、除尘,输入储气柜,混匀后再输送给用户。
转炉_转炉 -转炉结构
转炉炉体由炉壳和炉衬组成。炉壳由钢板焊成,而炉衬由工作层、永久层和充填层三部分组成。工作层直接与炉内液体金属、炉渣和炉气接触,易受浸蚀,国内通常用沥青镁砖砌筑。永久层紧贴炉壳,用以保护炉壳钢板,修炉时永久层可不拆除。在永久层和工作层之间设充填层,由焦油镁砂或焦油白云石组成,其作用是减轻工作层热膨胀对炉壳的压力,并便于拆炉。1.炉帽
为了减少吹炼时的喷溅和热量损失以及炉气的排出,故炉帽的形状皆做成截圆锥形或球缺截圆锥形,其炉口均为正炉口,用来加料,插入吹氧管,排出炉气和倒渣。由于炉帽处于高温炉气区,直接受喷溅物烧损,并受烟罩辐射热的作用,其温度经常高达300*400+,在高温的作用下,炉帽和炉口极易产生变形。为了保护炉口,目前普遍采用通入循环水强制冷却的水冷炉口,这样既可减少炉口变形又便于炉口结渣的清除。为防止发生事故,水冷部分应加强维护。
水冷炉口有水箱式和埋管式两种结构。水箱式水冷炉口见图4-1-3,它采用钢板焊接结构,其水箱内焊有若干隔水板,使冷却水在水箱内形成一个回路,同时也起加强筋的作用。这种结构冷却强度较大,制造容易,但是由于焊口易开裂,因此安全性较差。
埋管式水冷炉口如图4-1-4所示,它是把通冷却水用的蛇形钢管埋铸于铸铁中,这种结构冷却强度不如水箱式,但安全性和寿命均比水箱式高。
水冷炉口可用楔与炉帽联结,但由于炉渣的粘结,往往在更换损坏了的炉口时不得不用火焰切割。因此,我国在中小型转炉较多采用卡板焊接的方法将炉口固接在炉帽上。
2.炉身
炉身是整个炉子承载部分,皆采用圆柱型。出钢口通常设置在炉帽和炉身耐火炉衬的交界处。其位置、角度和长度的设计,应考虑出钢过程中炉内钢水液面;炉口和盛钢桶间的相互位置及其移动关系;堵出钢口方便否;能否保证炉内钢水全部倒完;出钢时钢流对盛钢桶内的铁合金应有一定的冲击搅拌能力等。在生产过程中,由于出钢口烧损较严重,为便于修砌、维修和更换,出钢口可设计短些。
3.炉底
炉底有截锥型和球型两种。截锥型炉底制造和砌砖都较为简便,但其强度不如球型底好,故只适用于中小型转炉。球型炉底的优缺点与截锥型相反,故为大型转炉采用。
炉帽、炉身和炉底三段的联结有三种方式:死炉帽活炉底、活炉帽死炉底和整体炉壳。三种联结的型式与修炉方式有关,死炉底和整体炉壳都采取上修,而活炉底的则采取下修。
转炉_转炉 -炼钢转炉
早期的贝塞麦转炉炼钢法和托马斯转炉炼钢法都用空气通过底部风嘴鼓入钢水进行吹炼。侧吹转炉容量一般较小,从炉墙侧面吹入空气。炼钢转炉按不同需要用酸性或碱性耐火材料作炉衬。直立式圆筒形的炉体,通过托圈、耳轴架置于支座轴承上,操作时用机械倾动装置使炉体围绕横轴转动(见图空气底吹转炉示意图)。50年代发展起来的氧气转炉仍保持直立式圆筒形,随着技术改进,发展成顶吹喷氧枪供氧,因而得名氧气顶吹转炉,即L-D转炉(见氧气顶吹转炉炼钢);用带吹冷却剂的炉底喷嘴的,称为氧气底吹转炉(见氧气底吹转炉炼钢)。在应用氧气炼钢的初期还使用过卡尔多转炉和罗托转炉,通过炉体回转改善炉内反应,但由于设备复杂,炉衬寿命短未能获得推广。
转炉_转炉 -炼铜转炉
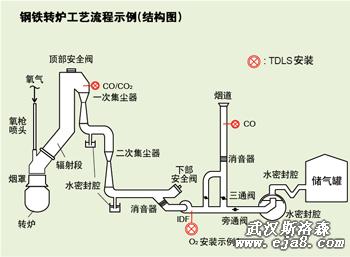
一般为卧式转炉用于处理铜锍,通过鼓入空气把冰铜氧化吹炼成粗铜,也用于吹炼冰镍。(见铜、镍)(见彩图卧式炼铜转炉──把冰铜吹炼成粗铜的设备、150吨氧气顶吹转炉)
转炉_转炉 -转炉钢包喷溅
一、喷溅机理转炉使用的氧化剂主要是氧气,纯度>99%。使用压力为6~12kgf/cm2通过吹氧来降低钢水中的碳含量。并氧化其它元素。碳氧反应的方程式为:
[C]+[O]={CO}↑+Q
反应生成CO,并放出大量的热。本炉冶炼终点含C0.10%。剔除锰铁及碳化硅进入钢中的碳,冶炼终点碳低于0.05%。说明本炉钢是过氧化钢,根据钢中碳与氧的乘积为一常数
[C][O]=m
这一原理,说明本次钢中含有大量的[0],钢中氧与投入包底的碳化硅突然反应,产生大量的CO气体,将钢水、钢渣喷出。同时,由于钢水过氧化,钢中氧含量高,钢中氧的溶解度随着温度的降低而下降,随着温度的下降钢中的氧大量析出,产生大量的气体,也是造成大喷的主要原因。
二、预防对策
1、钢水过氧化是产生喷溅的主要原因。因此,如何避免钢水过氧化是预防钢水大喷的根本措施。
2、 炉前在冶炼操作时,应采取的措施是增大供氧强度,采用多孔喷头,低枪位操作,这样可以降低渣中FeO含量从而降低钢中氧含量,提高一次拉碳命中率,应尽量减少补吹。加入合金脱氧时,应按照先弱后强的顺序,先加入硅铁,然后加入锰铁,以保证良好的脱氧效果。
3、保证拉碳准确,避免过低量的碳,然后补加碳粉或SiC来增碳,从而降低钢中的氧含量。
4、加入碳粉或碳化硅时,不要将碳粉或碳化硅一次性加入包底,以防被钢包底部渣子裹住,钢水翻入后,不能及时反应,待到温度达到碳氧反应条件后,急剧反应,另外,在钢包水中不能自动开浇,用氧气烧眼引流时,大量的氧气进入钢包中,打破钢包内原有的平衡,钢包内原有存在的大量气体,在外界因素的导致下,突然反应而导致大喷。
5、钢包要洁净,以防钢水注入钢包前期温度过底,碳粉或碳化硅与钢中氧不反应,待温度升高后,突然反应造成大喷。
6、炉前要加强吹氩搅拌,通过吹氩,来均匀钢水成份、温度,确保气体和夹杂物上浮,保证吹氩时间大于3min,吹氩压力保证钢包内钢水微微浮起为最佳,钢水翻花太大,钢包内钢水渣层被破坏,钢水吸气,使钢水二次氧化,钢水不翻花,吹氩搅拌效果不好,达不到去气去夹杂的效果。
7、加强终脱氧力度,凡终点碳低于0.05%个时,应加大硅铝钡量用,将硅铝钡用量提高到0.5~1kg/t。
8、连铸浇铸前必须将包盖扣好,钢包沿要清理好,以防止包盖不严,钢水、钢渣从缝隙中喷出,并在适当增加大包包盖的宽度。
9、防止钢包喷溅的关键是炉前避免出过氧化钢。因此,规范炉前冶炼操作是杜绝过氧化钢出现的主要措施。
10、顶吹转炉吹炼低碳钢种,可以直接一次拉碳,但为了一次有效地去除磷、硫,并使终点温度达到钢种要求,在吹炼低碳钢时,都要采用高拉调温一次补吹的工艺操作。
11、第一次拉碳时,钢中含碳量最好控制在0.16%~0.20%的范围内,倒炉测温、取样,根据炉温确定冷却剂加入数量,根据含碳量确定补吹时间。
12、 第一次拉碳时的炉渣碱度为3.4~3.6。
13、注意控制好炉渣,早化渣、化好渣,全程化透。通过调节枪位促进化渣。
14、第一次倒炉时要尽量多倒渣,可以加入石灰和白云石调温,如果加入调温剂的数量较多,可以在开始氧化时分批加入。
转炉_转炉 -负能、煤气回收
1、转炉炼钢工序能耗实现负值――负能炼钢在转炉内,把铁水炼成钢的过程,主要是降碳、升温、脱磷、脱硫以及脱氧和合金化等高温物理化学反应过程,其工艺操作是控制供氧、造渣、温度及加入合金料等,以获得所要求的钢液并浇铸成钢锭或连铸坯。氧气顶吹转炉炼钢法的特点之一是不需要外来热源,根据物料和热平衡计算:以铁水的物理热和化学热为主要热收入,抵消金属和炉渣的含热量以及各项热损失外,还有剩余热量。因此常将废钢、铁矿石和石灰石等作为冷却剂加入炉内以平衡热量防止炉温过高。
1.1炼钢过程的能量消耗
炼钢过程需要有足够的能量输入才能完成,通常要消耗电力、氧气、燃气、惰性气体、虚缩空气以及水、蒸汽等。以宝钢一期工程为例,详见表1。
1.2炼钢过程能量的释放
在吹炼过程中,碳氧反应是冶炼过程始终存在的一个重要反应,反应的生成物主要是C0气体(浓度约为85%~90%),但也有少量碳与氧直接作用生成CO2,其化学反应式为
2C+O2→2CO↑
2C+2O2→2CO2↑
2CO+O2→2CO2↑
在冶炼过程中炉内处于高温,碳氧反应形成的CO气体也称转炉煤气,温度约在1600℃。此时高温转炉煤气的能量约为1GJ/t,其中煤气显热能约占1/5,其余4/5为潜能(燃烧时转化为热能,不燃烧时为化学能),这就是转炉冶炼过程中释放出的主要能量。因此,转炉煤气回收利用是炼钢节能降耗的重要途径。
1.3炼钢工序能耗实现负值分析
炼钢工序能耗是按生产出每吨合格产品(钢锭或连铸坯)所用的各种能量之和扣除相应回收的能量(标煤)进行计算的。
消耗能量>回收能量时,耗能为正值
消耗能量-回收能量=0时(称“零”能炼钢)
消耗能量<回收能量时,耗能为负值(称“负”能炼钢) >
1.4实现负能炼钢是可能的
转炉炼钢过程中释放出的能量是以高温煤气为载体,若以热能加以度量分析,具体表现为潜热占83.6%,显热占16.4%,详见图3。显然,煤气所拥有的能量占总热量中的绝大部分。从图2中也可看出回收煤气对降低炼钢工序能耗所起的作用。因此,要做到负能炼钢必须回收煤气,而且应尽可能提高回收煤气的数量和质量。
1.5实现转炉负能炼钢必须回收煤气
1.6实现负能炼钢的主要技术途径
(1)采用新技术系统集成,提高煤气回收的质量与数量;
(2)采用交流变频调速新技术,降低炼钢工序大功率电机的电力消耗;
(3)改进炼钢(包括连铸等)操作水平,降低物料、燃料消耗;
(4)提高管理水平及人员素质,保证安全、正常、稳定生产。
2、转炉煤气回收技术
2.1转炉煤气净化回收主要代表流程
中国于1966年在上钢一厂30t转炉上首先实现了煤气回收,是湿法流程,简称OG法,主要采用两级文丘里型煤气除尘器,贮气为湿式煤气柜,至今中国已回收煤气的企业均为湿法流程(图4)。此流程基建技资较低,操作运行简单、安全,但运行费用相对较高,要附设除尘污水处理设施。
另一种干法流程,简称LT法(图5),为宝钢三期250t转炉引进奥钢联技术建设的煤气回收装置。转炉煤气净化采用干式静电除尘器,贮气为干式煤气柜。此流程基本建设投资较高,运行费用较低,操作较为复杂,没有污水处理设施,将与宝钢250t转炉同时投产。
2.2中国转炉煤气回收技术水平与国外先进水平的比较
①线性矩形可调喉口文丘里除尘器;
②可调喉口液压伺服装置;
③炉口微差压自动调节系统;
④快速三通切换阀;
⑤大管径文丘里型煤气流量计;
⑥煤气回收自动控制装置;
⑦煤气成分自动分析装置。
2.3回收煤气的节能潜力巨大
自1966年中国开始回收转炉煤气以来,经历了30年,到1996年已有20个企业回收了煤气(表4),占应回收煤气企业的51%。全行业转炉煤气回收利用率平均为51%,重点钢铁企业为70%,中小骨干企业仅为6%。如果目前还没有回收煤气的19个企业尽快增添回收设施,采用新技术装备,初期回收先按中等水平要求,即每吨钢回收65m3,煤气热值为1800×4.18kJ/m3,每年回收的煤气折合标煤可达34万t。已做到低水平回收的17个企业,用新技术进行技术改造,把回收水平提高到较高水平,即每吨钢回收70m3,煤气热值为1950×4.18kJ/m3,则每年多回收的煤气折合标煤可达16万t。上述二者之和,将达到每年回收能量约40万t,上述36个企业转炉炼钢工序能耗(标煤)将平均下降9.2kg/t,节能潜力是巨大的。
转炉负能炼钢是先进炼钢技术的重要标志之一,是炼钢工艺、装备、操作以及管理诸方面先进水平的综合体现,也是节能降耗、降低生产成本、提高企业竞争力的主要技术措施。实现负能炼钢也是一项艰难的科技攻关系统工程,需要将许多先进技术集成、配套,尤其离不开企业现代化的科学管理和生产,必须千方百计提高转炉煤气回收的数量与质量。
转炉_转炉 -转炉烟气净化与回收
1 回收基本原理1.1烟气的收集、冷却和净化
转炉烟气离开炉口时温度为1 400~1 500℃,主要采用循环水冷法令其迅速冷却。烟气经过众多毛细管环绕的活动烟罩、上部固定烟罩和汽化冷却烟道后,冷却至800~1 000℃,然后经溢流文氏管(以下简称“一文”)进行饱和冷却降温、除尘,此时温度已降至75℃左右。冷却后的烟气经重力脱水器进入矩形线性可调文氏管(以下简称“二文”),进行精除尘。此时,烟气与喷入二文内的水滴高速碰撞,由于扩散、惯性作用,烟气中的尘粒与水珠结合后凝聚而被除下。二文采用矩形“R-D”线性可调文氏管,通过阀板(米字阀)调节其开度,控制罩内差压。回收时,将罩内烟气压力调节至微正压(一般约为0~20 Pa),以控制空气吸入量(即控制O2的吸入量),减少烟气中CO的燃烧,使回收的煤气浓度增高。
1.2 烟气的抽取、放散及回收
煤气鼓风机是烟气除尘系统的重要设备,依靠它的强大抽吸能力将吹炼产生的大量烟尘抽走。淮钢风机通过液力耦合器调速,其转速根据生产工艺进行调整(淮钢烟气鼓风机高速为2 700 r/min;低速为800 r/min),动力源采用防爆电机。一般情况下,在转炉吹炼期,鼓风机升至高速;非吹炼期,降至低速。在鼓风机的烟气出口处,设有煤气分析仪,录检测到CO含量>40%,O2含量<1.5%时,烟气送入煤气加压站,作为燃料储存,否则引至烟囱放散。
2 主要设备选型与系统基本配置
转炉烟气净化回收自动控制系统,采用西门子SMATIC S7-400作为主站,挂接ET200M远程站,I/O模板选用S7-300系列,主从站间采用PROFIBUS-DP网通信,主干环网选用SIMATICNET。软件平台选用WINDOWS 2000 PROFESSIONAL,PLC编程环境采用Step7 V5.2,上位监控软件采用WIN CC V5.2,网络通信采用Soft Net软件。从运行效果看,硬件系统运行稳定可靠,软件系统刷新速度快,实时更新性好,配合报警与趋势功能,极大地满足了操作人员对于数值监测,设备控制以及数据记录的需要。
3 控制要求的实现
3.1 基本控制流程
在整个烟气净化与回收的过程中,由于烟气温度很高,且属易燃易爆气体,一旦出现泄漏将出现不可估量的后果,所以在控制方式上对自动化要求很高。
3.2 主要控制回路
(1)炉口微差压控制。采用闭环PID调节回路,将炉口微差压的检测值作为过程值,设定值一般在10 Pa左右,利用闭环调节二文阀芯开度。由于炉口微差压调节的好坏,直接影响煤气回收的质量,所以要求将比例调节值P和积分调节值I调节到使输出较为灵敏的数值处。此外,降罩后进行调节,抬罩后将二文阀芯开度设定到50%。
(2)风机转速控制。风机的全程自动调节取决于两点,即兑铁时刻和出钢时刻。当OG系统收到顶吹“兑铁”信号后,负机自动升至高速,吹炼完毕,转炉转至出钢角时,风机自动降为低速。风机高低速的转换,必须平滑,实现斜坡速度上升或下降,否则电流变化过猛,会对电机造成损害,缩短电机寿命。
(3)三通阀组连锁控制。三通阀组是决定煤气回收、放散的核心装置,阀组的控制也是OG系统中比较复杂的环节。在这一环节中,包括对三通阀体的控制,对水封逆止阀以及旁通阀的控制,对N2吹扫B1阀、B2阀、D阀的控制以及对冲洗电磁阀的控制。
4 尚待完善提高的环节
本设计完全满足了炼钢车间对于烟气净化与回收系统的工艺要求,控制系统运行稳定可靠,极大地方便了操作人员对于整个OG系统的监控。但纵观整体设计,存在以下两点不足:
(1)二文喉口处的喷水量直接决定着除尘效果的好坏,因这里总有大量烟尘通过,极易堵塞,厂家在这里设计了氮气捅针。操作工定时操作捅针,对二文喉口喷水处进行清堵处理。但这项上作琐碎易忘,导致堵塞后的除尘效果不好,冒出大量黄烟。在今后的设计中,应将这一过程加入PLC自控系统,以便定期自动完成清堵工作。
(2)自控系统很大程度上依赖于仪表测量到的准确数据。由于本系统处于高温、高粉尘环境中,所以某些位置的仪表易出故障,导致操作工无法正确了解各段设备的情况,不但直接影响除尘效果,更易发生意想不到的危险。所以今后在设计这类工况下的仪表时,务必在选型和安装位置上仔细斟酌,以便能够长期测量到准确的数据。