两年前的秋天,于秋涛来到德国巴伐利亚州奥迪总部。作为一汽-大众奥迪品牌项目经理,他负责一汽-大众所有奥迪产品的引进、规划和生产。当时奥迪计划在中国长春动工新建一个总装车间,以满足快速增长的市场需求。前一年这个豪华车品牌在中国销量已经超过8万辆,同比增长近40%。
这个投资约10亿人民币的新工厂计划在总部得到高度的关注,总部所有部门的负责人都参与了讨论,因为他们要在中国建一个“全数字化工厂”,作为未来奥迪工厂的标杆。 几年前,数字化工厂还是只存在于人们脑海中的“梦工厂”,现在已经越来越多的出现在现实中。于秋涛说,奥迪的全数字化工厂包含四个层面,一个是数字化的规划,也就是前期设计、布局的数字化,第二就是数字化生产,第三个是数字化的物流,第四个就是数字化的质量保证。 “最初我们做工厂规划方案的时候,用的就是数字化的模拟技术。包括所有的方案设计,包括所有的厂房空间、平面布置都通过计算机先做了虚拟设计。”于秋涛说。 工厂本身的建设就非常复杂。与周围的传统厂房相比,新总装车间采用和鸟巢一样的空间网架结构,屋顶的漫反射玻璃均匀地洒下阳光,能够节省2/3的照明能源。走进网架结构的厂房,看不见“钢铁森林”般的立柱,因为所有设备不是固定在地上,而是吊在网架上,对于结构有着复杂的技术要求。 更复杂的是怎样布置生产线。所谓标杆是这样形成的:工厂设计时就把包括德国、匈牙利以及比利时奥迪工厂的所有经验整合在一起,并吸收日系、韩系企业的精益生产方式理念,参照国内生产体系的特点,融合后取长补短。 9月19日,一汽-大众的全数字化新奥迪总装车间在长春宣布正式投产,于秋涛向《商务周刊》详细解读了这个代表当今最高水平的豪华车总装工厂。 《商务周刊》:作为信息化时代制造业的发展趋势,数字化工厂能够实现更加灵活和柔性的生产,在这个工厂中是如何体现的? 于秋涛:这个工厂年产能10万辆,通过完善、精密的系统控制,我们的个性化生产完全可以做到每辆车都不一样。 因为我们的设备是数字化的,也就是可以通过计算机系统的控制自动调节。以吊具为例,每个的高度都是可以升降的,从第一个工位开始,吊具的整个运行线路和高度都是用计算机控制。具体来说,每一个吊具都有自己的编码,有自己的数据载体,这个吊具在哪个位置,都由计算机系统进行控制,比如在安装车底部管路的工位,那么高度就升到1米7、1米9,如果装车内的仪表、手刹车,就可以降到1米5的高度。而且这个高度根据不同的车型可以编程的,同一个点同一个位置可能装A4L的是1米6,装Q5就变成1米7,根据车型不同调整高度。 还有一个例子,所有拧紧系统都是数字化的。我们车上所有的螺栓,可以说涉及到重要的安全性的螺栓,全都是电控的扳手拧紧。不同的车型,不同的装备要求的扭矩不同,这些数据都是直接输入拧紧机里,这个拧紧机按要求拧紧,然后保存在中央服务器里,这个服务器保存所有的数据最低在15年以上,以便为未来的检测维修提供可追溯的基础数据。 《商务周刊》:这种新的工厂,新的生产方式,对于工人来说,工作的难度是降低了还是提高了? 于秋涛:对工人的要求可以说变低了,变简单了,因为很多事情是由数字化的系统控制、管理。我们的工人只需要一些简单的操作就可以了,相应的劳动强度也降低了,比如一次拧紧需要100牛顿的力,一个工人干一天的活下来,可能胳膊就抬不起来了。用电动扳手只要把工具推到位就OK了,只需要很小的牵引力就够了。 我们的理念是,人是一个情绪化的动物,他可能会随时随地因为不同的情绪影响他做的工作,我们需要在设备上把人的情绪化对质量的影响规避掉。像电动扳手,只要人把设备推过去了,剩下的事情,比如扭的力矩是多大由我的设备保障了。 用人工的话,本来应该拧15牛顿的可能只扭了10牛顿,但通过计算机这种现象不会发生,拧紧的结果也是通过传感器检测的,保证这个力一定会达到要求的力矩,而不会因为人的操作,这个扳手少拧一圈或拧的时候斜了一点造成最后的结果不合格。我们数字化工厂就是能够保证所有的不可控因素都规避掉,最后保证我们的产品质量处于最高水平的状态。 《商务周刊》:也就是说数字化生产更容易控制产品质量。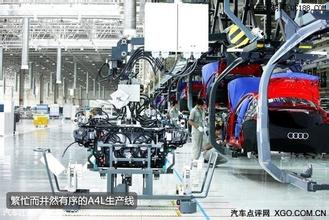
于秋涛:是的。因为质量的控制环节在生产线上就开始同步进行了。每隔一定数量的工位就有一个质量检测点,在这个环节上出现的质量问题直接就消除掉了,而且记录也都保存在计算机系统里。这样我们的车维修量就非常小,这就是数字化的质量控制。 而且整车下线以后我们还有各种检测设备。我们的工厂是世界上最好的工厂,我们所有的设备也是世界上最先进的设备。日系工厂的车轮主要是靠人的经验调整,但我们德系的检测都是通过设定好的外倾、内倾、前倾、后倾等角度,通过测量系统进行控制。检查结果会统一保存到数据库里,在交车之前我们把所有核心数据都要打印出来,然后要在系统里进行检查这个车是否合格,通过扫描车辆的编号,对从第一个工位开始到检测工位结束的所有过程都进行一次检验,看有没有哪个问题没有消除掉或者漏掉了,都合格了我们才能交车。所以说,数字化的质量控制系统是百分之百地做检测,而不是抽检,这在欧洲也还没有实现。 《商务周刊》:新工厂还借鉴了以丰田生产方式为代表的日式生产现场管理,以“看板”方式减少库存、消灭次品。在两个不同的生产体系中,这种借鉴是如何实现的? 于秋涛:说借鉴韩国或者日系企业的理念,也只是一种概念性的东西,具体到细节上和他们还是不一样的。我们把所有能优化的结果都集成到一块了。 在物流系统中,我们第一次尝试用了物流超市的概念,这在奥迪全球都是首次。这个物流系统就是借鉴了日韩生产方式,比如我们也有看板,有一个纠错系统,更好地保证零部件的管理、现场的秩序。具体来说,包括生产的准确性、供货的准确性,都在超市里面用电子看板显示,系统会提示你这个车拿这个件,如果你拿别的零件系统就会报警。 这个物流系统和其他品牌都有所不同,我们奥迪也是第一次这么大规模地用这个操作系统,两年前做生产方案时,总部刚刚形成了物流超市理念,在德国的生产线上做了一个小范围的试验。全面的实施,一汽-大众奥迪新工厂是全球第一次。