3.2.10 自动化"自动化"是丰田准时化生产体系质量控制的重要手段。为了完美地实现准时化生产,生产过程中依次流往后工序的零部件必须是百分之百合格的制品。因此,零部件制品的质量检测和控制是极为重要的。每当有不合格制品出现或有异常现象发生时,机器会马上自动停止运行。丰田公司的"自动化"是制品质量检测控制和质量保证体系中的一个组成部分,它不是指用机械代替人工,而是指一整套防止在机器或生产线上大量产出不合格制品的方法和手段,是一种"自动异常检测控制系统"。所谓"自动机器",是指有自动停机装置的机器设备。每当有不合格制品出现或有异常现象发生时,机器会马上自动停止运行,以便使作业人员查找出现异常的原因。在丰田公司,几乎所有的机器设备都装有这样的自动化检测控制装置,从而有效地防止了大量不合格制品的产生。3.2.11 良好的外部协作关系在专业化分工高度发达的现代化工业社会里,分工协作所产生的社会自然力,对提高劳动生产率有着重要的作用。丰田公司的专业化分工协作是世界闻名的。丰田公司约80%的零部件是由分包协作企业生产供应的。在一个由成百上千家企业共同合作完成的产品生产过程中,企业之间良好的、协调的合作是非常关键的。特别是丰田准时化生产所特有的"拉动式"生产组织方式,必须有协作企业的理解和配合支持,只有在协作企业群体内部的成员企业共同致力于完善这种生产条件的情况下,才可能产生出应有的效力。因此,良好的外部协作关系是准时化生产又一个重要支撑。丰田准时化生产所特有的"拉动式"生产组织方式,必须有协作企业的理解和配合支持。3.3 丰田准时化生产要点丰田准时化生产的主要目的在于降低成本,从而提高利润。这里,成本的概念不仅包括制造成本,同时也包括资本成本、销售成本和管理费用。为了达到降低成本之目的,最重要的手段就是制止过量生产,杜绝各种浪费,并对市场需求的变化做出迅速而有效的反应。这样的理想是凭借着准时化生产而实现的,即在必要的时刻生产必要数量的必要产品或零部件。为了实现准时化生产,丰田公司采用了"拉动式"生产组织控制方式,即把传统的"送料制"改为"取料制",从而有效地制止了过量生产,实现了生产的准时定量化。看板管理是"拉动式"生产组织控制方式的重要工具。与生产需要有关的产品数量、种类、生产时间等信息,均由看板从生产过程的下游传递到其上游。为了有效实施看板管理,生产过程必须实现均衡化,即总装配线和后道工序都必须而且能够在数量上和种类上均匀地从前道工序领取零部件或物料及物品。这样的均衡化生产要求必须以"多品种、小批量"方式进行。生产批量的减少和品种变换的频繁,要求必须缩短生产前置期,特别要实现设备的快速装换与调整,从而保证能够在低成本的情况下,小批量地生产各种产品或零部件。"小批量、多品种"的均衡化生产凭借着设备的快速装换与调整而得以实现。但是,这种生产方式所带来的零部件制品的小批量频繁的运输,必然增加运输成本。显然,为了减少运输成本,工序设计和设备合理布置是必不可少的。生产单元式设备布置,为多技能作业员的出现提供了条件。这些成为单件生产、单件传递方式的基础,从而为减少工序间的在制品储备、减少用工、加速物流、提高制品质量、提高劳动生产率创造了条件。标准化作业是实现单件生产、单件传递的重要手段。它把在标准周期时间内,每一位多技能作业员所应承担的一系列作业标准化,以便保证在同一个生产单元内的所有作业员都能够在标准周期时间内完成自己的全部作业,达成生产单元内的生产平衡。由百分之百合格品和"不让不合格品进入下道工序"所支撑的准时化生产,可以由全面质量管理和"自动化"得以确保。这里的"自动化"是一种"自动异常检测控制系统",其作用是确保质量,防止大量不合格品的产生。改善活动是丰田准时化生产发生效力的最基础支撑。"改善无止境"是丰田生产方式的一个重要特性。大量的日常改善活动,使丰田生产体系不断地向合理化的终极迈进。最后,尊重人性,调动人的积极性,培养人的责任感和自主精神,以及良好的企业外部的协作关系,是丰田准时化生产成功的软性支撑。显然,它们对任何组织都是重要的,但对丰田准时化生产尤其重要。3.4 准时化生产技术支撑体系的逻辑:实例分析某上市公司于2009年启动精益化改善,经慎重选择,初步选择占销售额比重较大的A产品系列作为改善试点线。其生产地布局如图2-6所示。该系列产品细分的型号有100多种,经ABC分析,其A1、A2、A3型号占该产品系列销售额90%以上,故选取此三种型号为重点改善对象。要及时应对市场需求的频繁变化,该企业以往的做法只能是尽可能备足存货。经观测,三种型号产品一次排产均为100件,由班组所有工人同时在线装配,理论生产周期约一周。大批量排产导致在制品过多、产成品库存过高(平均近三个月周转一次!),频繁的插单延长批量生产周期成为常态。结果导致资金占压、现场浪费严重、成本高居、质量不稳定、交货吃紧(暂时不需要的出现大量积压库存、同时常常出现急需的订单插单生产),影响产品的市场竞争力(连续两年销量下降)。改善的核心在于尽快实现三种产品的准时化生产,以消除浪费、实现柔性生产,提高产品市场竞争力。此时若贸然实施看板管理(每天按发货数量的信息指示安排生产),将给现场造成巨大混乱,必须进行系统的配套改善。第一,生产计划若仍然采取每次100台的模式下达,现场生产组织获取的信息仍然是批量生产的信息,现场班组无从确定当天的实际排产数量。改善的要点是实现均衡计划,每天按销售预测后的平均日产量下达生产计划(并进行微调),及运用"均衡生产计划"排产,生成均衡的生产排产信息。经价值流图分析,三种产品日均需求量分别为8台、7台、5台,一个工人可以完成一天的生产量。改善的第一目标是实现一个工人日生产平均入库量分别为8台、7台、5台,即实现按日需求量及时生产出成品。第二,即使均衡排产,由于所有供应商仍采取批量供货方式,零部件经常出现积压与缺货并存的情况,无法保证均衡生产的正常进行。改善的要点是与供应商沟通,尽可能按新的均衡生产计划供应,并保证供应环节不出现延迟交货等意外情况。第三,现场质量检验环节手法较落后,仍习惯沿用大批量生产下的检验模式,没有及时发现不良品的能力(自动化),且零部件质量不稳定,会意外中断均衡生产过程,最终导致当天生产不足,次日赶计划的混乱状况。改善的要点是实现检验与生产的同步化,需要改善检验部门与生产部门的协同作业,并提高供应商的质量标准。第四,现场布局和作业台布局严重不合理,小批量生产将导致每台产品平均搬运工作量剧增,现场阻力巨大。改善的要点是重新规划生产现场布局,"取替"物流浪费。第五,三种产品同一天生产,原有适应大批量生产的备料等切换速度非常慢(仓库与生产现场的脱节、备料流程点数等环节浪费严重),将产生巨大的换序时间浪费,会遇到现场工人的抵制。第六,三种产品同一天由一个工人生产,需要其具备三种产品的生产技能,并需要其能够独立完成所有工序的作业(多能工)。但当时多数工人不具备此种能力。改善的要点是要求该班组工人成为多能工。第七,现场作业没有统一标准,不同工人作业时间存在较大差异,同一个工人作业时间也不稳定,将导致日生产进度的较大波动,影响及时交货。改进的要点是制定操作标准,使作业时间可控。上述七个问题,环环相扣,互相制约,要最终实现准时化生产,必须全面解决这七方面问题。而其中的大部分问题(作业标准、多能工、换序、布局方案、检验同步化等),唯有现场工人和班组长才能给出最有效地改善方案。实际的改善实施过程中,首先确立相信、尊重和依靠现场员工的基本原则,对其进行精益生产改善手法和精益思想的持续培训,设立提案奖励制度,与员工一起讨论和实验各种可能的改善方案,使员工逐渐积极参与到现场改善过程中。其次确认和实施第一步改善流程,和现场员工一起讨论、制定和实施了现场浪费分析、作业标准、工作台布局方案、同步质量检验方案、多能工培养方案和小批量生产方案,经半年时间,实现了初步的均衡化生产。半年改善效果显著,三种产品在制品降低50%以上,产成品库存降低70%以上,生产周期缩短50%以上,质量、成本、交货期得到巨大改善。
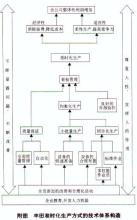