目前,在模具加工中,电火花加工技术占有重要的地位。现代社会,终端产品更新的速度很快,对模具加工提出了更高的要求。在保证模具质量的前提下,对模具的加工效率和成本要求越来越苛刻。
GF阿奇夏米尔在60年的放电加工机床制造历程中、始终引领每次的产业浪潮和产业升级,在业界赢得得很高赞誉。在电火花加工中,大面积加工和深窄槽加工是很常用的应用,是重点也是难点。GF阿奇夏米尔的数控电火花成型机床FO350SP很好了胜任这一难题。
FO350SP机床集合了阿奇夏米尔60年电加工技术之精华,经历几代传承,成为电加工机床的一代经典机床。仅在中国市场,就有数千台机床在使用中。
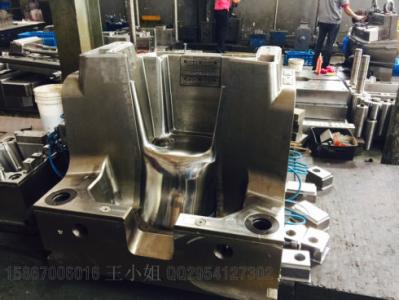
大面积加工
在成型加工中,大面积加工的难点在于如何在保证表面质量的前提下,最大可能提高加工效率。众所周知,放电加工中最不希望出现拉弧和积碳现象从而形响加工表面质量。在大面积加工中尤其难于控制这种不良放电现象。电火花是一种由点到面逐步放电而达到去除材科的加工手段。体现在大面积加工中,就要保证每一次的火花控制都要一致,不出现积碳和技弧现象,这需要脉冲电源、数控系统和机床精度的完美结合。早在20年前,瑞士夏米尔公司就成功解决了拉弧现象,从此“夏米尔纹”成为业界的标准火花纹。粗糙度不是以Ra值来标注,而是以夏米尔公司的CH 值来体现。瑞士夏米尔也是业界第一个以10%误差这种精确化表示加工表面一致性的公司。以前只在高端机型上配备的SPAC防短路专家系统,现在标配在 FO350SP机床上。在电火花精加工中,电极和工件之间会形成“一层碳层”以“研磨”工件的加工过程。但是,如果不能精密控制,就会造成“积碳”现象,加工表面就会不均匀。SPAC监测每一次火花放电,一旦监测到“不良”放电,就会瞬间产生大电流击碎“碳块”,而从避免积碳。
以上图的加工实例来说明。中间的“GF”大面积加工面积大概15平方厘米,要求加工到粗极度CH10 (RaO.4微米)。最后的加工结果是在不同区域和不同方向上测量,粗糙度都在RaO.4-0.42微米范围内。
有人可能会说这是“慢工出细活”。这句话在20年前是对的,但是在今天的FO350SP机床上却完全是“不仅活细,而且很快”直接位于Z轴加工头的右边的第三代精修电源摸块,更靠近加工区域,从而更加精确的控制每个火花,最重要的是,大大提高了精加工的效率。同时FO350SP机床配备的新的平动专家系统也功不可没。之前的平动系统是一种等速的摇动加工,并不智能。新的平动专家系统,运用新的计算原则,根据摇动平面的去除材料的不同智能地调节摇动的速度。这样的结果是每一次设定加工结束后不留“死角”,从而不影响后续的加工速度。另一方面,这样的智能平动方式也为表面质量的一致性打下了基础,在上面的例子中,F0350SP机床用了一租一精两个电极、总的加工时间仅8小时15分钟。
深窄槽加工
深窄槽加工也是电加工的一个难点。由于加工深度很深,造成废液排屑困难,形成短路,影响加工效率。同时,由于电极容易在尖角部造成很大的损耗,在这样的加工条件下,更是损耗巨大。这个加工问题要解决三个问题:排屑问题,损耗问题和加工效率问题。FO350SP 配备高速Z轴,高达15米/分钟,通过Z轴的高速运动形成抽吸达到废屑排出的效果。结合第四代的自适应放电专家系统,FO350SP机床并不把效率浪费在单纯的Z轴高速运动中。根据加工深度的变化,加工状况的不同,Z轴有时急促而且密集的在工件上高速加工,有时快速的拉抬Z轴排出废屑瑞土机床传统的高精密床身结构对高速Z轴运动是依然保持高精度的火花间隙控制奠定了坚实的基础。最新配备“零”损耗模块,极大地降低了电极的损耗。以下面的加工例子来说明。电极尺寸10*1毫米,加工深度25毫米。最终粗糙度CH24 (Ra1.6微米)。
从图中可以看出第一个电极的尖角部有一点损耗,第二个则极少。总的加工时间仅2小时12分钟。IQ模块的原理是在电极表面形成一层“保护层”以达到减少电极损耗。所以,它对石墨电极的质量和粗细无关,大大降低了电极的成本。
综上所述,经典的FO350SP机床必能在中国市场上再奏华关乐章。由大天加工中心 http://www.hzdtsk.com 整理发表,转载请注明