半干法是利用烟气显热蒸发石灰浆液中的水分,同时在干燥过程中,石灰与烟气中的SO2反应生成亚硫酸钙等,并使最终产物为干粉状。半干法工艺较简单,干态产物易于处理,无废水产生,投资一般低于湿法,但脱硫效率和脱硫剂的利用率低,一般适用于低、中硫煤烟气脱硫。在半干法烟气脱硫技术中主要有喷雾干燥烟气脱硫、循环流化床烟气脱硫和增湿灰循环烟气脱硫等技术。
1. 喷雾干燥烟气脱硫技术
喷雾干燥烟气脱硫是利用喷雾干燥原理,在吸收剂喷入吸收塔后,一方面吸收剂与烟气中的SO2发生化学反应,生成固体产物;另一方面烟气将热量传递给吸收剂,使之不断干燥,在塔内脱硫反应后形成的产物为干粉,其部分在塔内分离,由锥体出口排出,另一部分随脱硫后烟气进入电除尘器收集。喷雾干燥烟气脱硫工艺流程包括:(1)吸收剂制备;(2)吸收剂浆液雾化;(3)雾粒与烟气的接触混合;(4)液滴蒸发与SO2吸收;(5)灰渣排出;(6)灰渣再循环,其中(2)~(4)在喷雾干燥吸收塔内进行。
喷雾干燥烟气脱硫工艺大多采用CaO含量尽可能高的石灰作脱硫剂。石灰仓内贮存的粉状石灰经螺旋输送机送入消化槽消化,并制成高浓度浆液,然后进入配浆槽,配浆槽上设有过滤器,以清除大颗粒杂质。在配浆槽内用水将浓浆稀释到需要的浓度,一般为20%左右,然后用泵打入位于石灰乳贮罐之上的振动筛(网眼直径约1.5mm),除去大颗粒杂质。过滤后的石灰乳流入石灰乳贮罐,再用泵送入高位给料罐备用。喷雾干燥烟气脱硫工艺的关键设备是脱硫塔,安装于吸收塔项部的离心喷雾机具有很高的转速(10000rpm~20000rpm),吸收剂浆液在离心力作用下喷射成均匀的雾粒,雾粒直径小于100μm。这些具有很大表面积的分散微粒,一经同烟气接触,就发生强烈的热交换和化学反应,迅速将大部分水分蒸发掉,形成含水量较少的固体产物。该产物是亚硫酸钙、硫酸钙、飞灰和未反应氧化钙的混合物。由于其未完全干燥,在烟道和除尘器内未反应氧化钙仍将继续与烟气中的SO2反应,使脱硫效率有一定的提高。从喷雾干燥吸收塔和除尘器底部收集的灰渣中含有相当数量反应剩余的氧化钙,大多燃煤飞灰也含有一定碱性物质。为了减少新鲜脱硫剂的耗量,将部分脱硫灰渣再循环是必要的。若FGD系统入口处脱硫剂与SO2的化学计量比为1.5,进行灰渣再循环操作时,可使反应区的实际化学计量比接近3.0,有利于脱硫反应的进行。据报道脱硫灰渣再循环可使系统脱硫率提高10~15%。同时灰渣的再循环改善了传质传热条件,有利于雾粒干燥,从而改善了吸收塔塔壁结垢的趋势。除上述系统外,许多欧洲国家在喷雾干燥脱硫工艺中增设预除尘器和烟气再热装置。烟气进入设置于吸收塔前的预除尘器,把烟气中的大多数飞灰去除。其目的有以下几个方面:(1)防止下游设备由于飞灰带来的磨损;(2) 降低废物处理的体积;(3)由于飞灰的市场已经比较完善,预除尘器得到的飞灰可以出售。预除尘器通常是一台简单的单电场电除尘器。在改造工程中,往往把已有的除尘设备作为预除尘器。
从1980年首台喷雾干燥脱硫装置投入商业运行以来,遇到的主要问题为以下几个方面:(1)容器和管道的堵塞;(2)吸收塔内固体沉积;(3)喷雾器磨损和破裂;(4)烟道和除尘器的腐蚀。这些问题是由石灰浆液或石灰粉末引起的,也是喷雾干燥吸收塔或处理浆液和粉末工业的常见问题。石灰具有容易吸收水气变成坚硬固体的特性,石灰浆会造成堵塞和磨损。另外,由于缺少合理的设计技术,一些问题主要发生在运行初始阶段并与特定的位置有关。容器与管道问题是由于固体沉积以及由此引起的堵塞。这是由于浆液流速小于设计值,管道内存在流动停滞区,使用过量的石灰及飞灰等原因造成的。这些问题导致要周期性地关闭受影响的部件以清除坚固的沉积物。改进的方法包括修改管道设计,提高浆液流速消除流动死角,提高浆液槽泵的吸入短管,改进搅拌和容器隔板的设计,在运行中周期性地转动设备。
在许多喷雾干燥脱硫塔中固体沉积分布从局部往往会扩展到整个塔内壁面上,这是喷雾干燥脱硫工艺需要解决的最重要问题之一。在设计工况下连续运行可冲刷掉少量的局部沉积物,对于大量沉积物则需要关闭吸收塔。导致产生沉积物的主要原因是吸收塔内温度控制不合理,以及运行时喷入的固体浓度小于设计值。由于运行过程中安装在吸收塔出口管道内的热电偶表面逐渐被脱硫产物覆盖,因此读出的温度将变得不准确。研究表明在吸收塔出口温度控制回路中加入入口气体流量和温度的前馈信号,可使吸收塔出口温度更加稳定并且减少固体沉积物。
喷射石灰浆的喷雾器会遇到磨损和破裂的问题,特别是在达到最佳工况前的初始运行阶段。旋转喷雾器以其良好的性能成为喷雾干燥脱硫工艺中使用最普遍的浆液分散器。不过由于机械上比较复杂,与其它类型的喷雾器(如双流体喷嘴)相比,需要更加严格的维护。
除尘器(ESP和袋式除尘器)的腐蚀问题主要与烟气温度低而且湿度高有关。调峰电厂容易遇到这个问题,因为每天它们要经受相当大的负荷变化,而且周末期间停止运行。这将导致每个星期中除尘器的温度多次低于露点温度,形成的酸液在壁面上凝结导致腐蚀。
上述4方面的问题目前已经得到了解决,使喷雾干燥烟气脱硫系统运行的可靠性大大提高,已超过97%,这是20多年来,简化工艺设计和去除系统中多余装置的努力结果,从而使半干法烟气脱硫市场占有率仅次于湿法,列第二位。
2 循环流化床烟气脱硫技术
循环流化床烟气脱硫(CFB-FGD)技术是20世纪80年代后期由德国Lurgi公司研究开发的。目前该技术的200MW烟气循环流化床脱硫系统已投入运行。德国的Wulff公司在该技术基础上开发了回流式循环流化床烟气脱硫技术。此外,丹麦FLS.Miljo公司开发的气体悬浮吸收技术也得到了应用。
循环流化床烟气脱硫系统由石灰浆制备系统、脱硫反应系统和收尘及引风系统组成,其主要设备为流化床反应器、带有特殊预除尘装置的电除尘器、水及蒸汽喷入装置,引风机等设备。其工艺过程为从锅炉出来的烟气进入GSA反应器的底部与雾化的石灰浆混合,反应器内的石灰浆在干燥过程中与烟气中的SO2及其它酸性气体进行中和反应。烟气经旋风分离器分离粉尘后进入电除尘器或滤袋式除尘器,然后符合标准的清洁气经烟囱排放到大气中。含有脱硫灰和未反应完全的石灰的流化床床料在旋风分离器中分离,其中99%的床料经调速螺旋装置送回反应器中循环,只有大约1%的床料作为脱硫灰渣排出系统。脱硫灰的循环意味着未反应的石灰可以继续进行脱硫反应,并且脱硫灰的循环可以更好地分散雾化石灰浆,促进脱硫反应的进行。主要控制参数有床料循环倍率、流化床床料浓度、烟气在反应器及旋风分离器中停留时间、钙硫比、反应器内操作温度等。主要特点如下:(1)没有喷浆系统及浆液喷嘴,只喷入水和蒸汽;(2)新鲜石灰与循环床料混合进入反应器,依靠烟气悬浮,喷水降温反应;(3)床料有98%参与循环,新鲜石灰在反应器内停留时间累计可达到30min以上,使石灰利用率可达99%;(4)反应器内烟气流速为1.83~6.1m/s,烟气在反应器内停留时间约3s,可以满足锅炉负荷从30%~100%范围内的变化;(5)对含硫量为6%的煤,脱硫率可达92%;(6)基建投资相对较低,不需专职人员进行操作和维护;(7)存在的问题是生成的亚硫酸钙比硫酸钙多,亚硫酸钙需经处理才可成为硫酸钙。
循环流化床脱硫塔内进行的化学反应是非常复杂的,多年来人们从不同的角度进行了大量的研究。一般认为当石灰(CaO)、工艺水和燃煤烟气同时加入流化床中,会有以下主要反应发生:(1)生石灰与液滴结合产生水合反应:CaO+H2O → Ca(OH)2 (2)SO2被液滴吸收:SO2+H2O → H2SO3 (3)Ca(OH)2与H2SO3反应:Ca(OH)2+H2SO3 → CaSO3·1/2H2O +3/2H2O (4)部分CaSO3·1/2H2O被烟气中的O2氧化:CaSO3·1/2H2O+1/2O2+3/2H2O →CaSO4·2H2O。
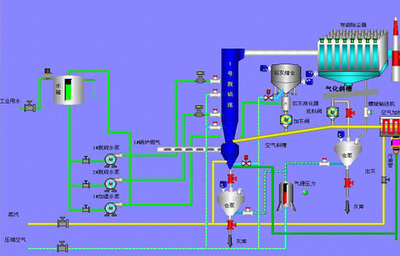
由上述反应可看出,脱硫塔中进行的是气液固三相反应,其反应速率由下述步骤所决定:(1)气相主体中的SO2靠湍流扩散到气膜表面;(2)SO2靠分子扩散通过气膜到达两相界面;(3)在界面上SO2从气相溶入液相;(4)液相SO2靠分子扩散从两相界面通过液膜;(5)液相SO2靠湍流扩散从液膜边界到液相主体;(6)Ca(OH)2固体扩散到液相主体中;(7)Ca(OH)2颗粒的溶解;(8)液相主体中的SO2和Ca(OH)2进行反应。上述SO2和Ca(OH)2的传质是分别同时进行的,并且相互影响,相互促进。Ca(OH)2和SO2反应的活性与浆滴中水分的存在时间有极大的关系。因为这些反应都是在液相中进行的,所以水分的蒸发限制了以上几步在液相中的反应,如步骤(4)~(8)。生成物CaSO3由于在反应界面上产生,它将沉积在表面上,这样随着反应的进行以及颗粒的再循环,部分未反应完全的颗粒表面上就会留下一层惰性产物。通过这些产物层的扩散可能成为反应速度的限制步骤。特别是当反应产物形成一种致密层时,反应速度必然受它的影响。由于流化床中颗粒物存在不断磨损,这意味着反应形成的产物将不断地被剥落,因此,流化床中一般不考虑产物层扩散的影响。
循环流化床烟气脱硫技术是近几年新兴起的具有开发前景的烟气脱硫技术,它具有投资相对较低,脱硫效率高,运行可靠,操作维护方便的优点,是值得进一步开发的脱硫技术。此项技术在国际上已基本成熟,目前在我国处于工业示范阶段,其应用前景广阔。
3. 增湿灰循环烟气脱硫技术
增湿灰循环脱硫技术(NID)是ABB公司在喷雾干燥烟气脱硫基础上发展起来的烟气脱硫方法,它借鉴了喷雾干燥脱硫的原理,又克服了该技术使用制浆系统而产生的弊端。因此,具有投资低而方便可行的特点,用于中小型发电机组,当燃中低硫煤时,脱硫效率至少可达80%。NID工艺设备紧凑、占地小,能方便安装到原有设备上。
NID技术常用的脱硫剂为CaO,要求平均粒径不大于1mm。CaO在消化器中加水消化成Ca(OH)2,然后与布袋或电除尘器除下的大量循环灰进入混合增湿器,在此加水增湿使混合灰的水分含量从2%增加到5%,然后含钙循环灰被导入烟道反应器。含5%水分的循环灰由于有极好的流动性,省去喷雾干燥法复杂的制浆系统,克服了普通半干法活化反应器或喷雾干燥吸收塔中可能出现的粘壁问题。大量脱硫循环灰进入反应器后,由于有极大的蒸发表面,水分很快蒸发,在极短的时间内使烟气温度从140℃左右降至70℃左右,烟气相对湿度则很快增加到40%~50%。这种较好的工况,一方面有利于SO2分子溶解并离子化,另一方面使脱硫剂表面的液膜变薄,减少了SO2分子在气膜中扩散的传质阻力,加速了SO2的传质扩散速度。同时,由于有大量的灰循环,未反应的Ca(OH)2进一步参与循环脱硫,所以反应器中Ca(OH)2的浓度很高,有效Ca/S比很大,且加水消化制得的新鲜Ca(OH)2具有很高的活性,这样可以弥补反应时间的不足,能保证在1s左右的时间内脱硫效率大于80%。由于脱硫剂是不断循环的,脱硫剂的有效利用率达95%以上。最终产物则部分溢流入终产物仓,由气力输送装置外送。脱硫灰可用作水泥混合料、缓凝剂、筑路、盐碱地改良等。NID技术特点主要有以下3点:(1)取消了制浆和喷浆系统,实行CaO的消化及循环增湿一体化设计,这不仅克服了单独消化时出现的漏风、堵管等问题,而且能利用消化时产生的蒸汽,增加了烟气的相对湿度,对脱硫有利。(2)实行脱硫灰多次循环,循环倍比可高达50倍,使脱硫剂的利用率提高到95%,克服了其它干法、半干法工艺脱硫剂利用率不高的问题。(3)脱硫效率高。用纯度90%的CaO作脱硫剂,当Ca/S=1.1时,脱硫效率能大于80%;当Ca/S=1.2~1.3时,脱硫效率可达90%以上。